前回の3事例に引き続き、大企業を含めたIoT導入事例やツールを参考に紹介したい。
④ 三菱電機 電力をきめ細かく可視化し節電
昨今、IoTを用いて電力の使用状況を細かく「見える化」し、無駄な電力のさらなる排除が可能になっている。
三菱電機では、電力の使用状況について、きめ細かく「見える化」して食堂に大きな画面で表示し、従業員全員に周知徹底している。また、停止している生産ラインの設備は、待機電源まで落とすこともやろうと思えば可能。更に、建築物ではいまや常識になっている人感センサーを工場内に設置し、作業員がいる時間と場所だけ、必要な照明と空調を提供することも容易である。
これまで日々「カイゼン」努力を行い、省エネに取り組んできた大企業である三菱電機「サーボモータ工場」でさえ、電力消費量が約25%落ちたという現実がある。そのため「ほとんど省エネ努力をしてこなかった中堅・中小企業では、電力量は簡単に、数割は落ちるだろう」との指摘が「IoTによる中堅・中小企業の競争力強化に関する研究会」であった。
⑤ つながる町工場プロジェクト 3社の機能が水平統合
今野製作所、西川精機製作所、エー・アイ・エスの3社が参加し、16年4月から「つながる町工場プロジェクト」が行われている。同プロジェクトは、インダストリアル・バリューチェーン・イニシアチブ(IVI)の「つながるものづくりアワード2016」の大賞も受賞した。
独Industrie4.0 における企業間の「水平統合」に相当する取り組み。EDIなどの疎結合とは異なり、複数企業においてビジネスプロセスやビジネスルール、ITシステムを密結合し、3社があたかも1つの企業のようにマーケティング、販売、提案・見積、設計・試作、製造、品質管理、出荷・回収を行う。
各社のモノづくりの強みをITで連携強化し、短納期・低コスト・高付加価値に取り組んだ水平分業の事例である。
IVIの堀水修理事(日立製作所IoT推進本部)は、工場間連携について、「頻繁化する生産調整やドイツが提唱するマスカスタマイゼーションに対応するべく、一貫生産ラインよりも小回りの利く水平分業の流れが強まるだろう」と評している。
⑥ 富士通 ボトルネックを即時発見
富士通では、製造工程の稼働状況を可視化するIoTソリューション「FUJITSU Manufacturing Industry Solution VisuaLine」(ビジュアライン)を、16年12月に発売した。ビジュアラインは、生産工程に関わる製造設備からのログデータを収集し、1製品ごとの稼働状況をグラフなどの様々な表現形式にて可視化するシステムだ。
日々のグラフとの比較から、通常よりも時間がかかっていることなどを一目で読み取ることができ、設備からのアラームや稼働停止が発生しなければ気づくことができなかった異常箇所の早期発見が可能になる。
これにより、ログデータから設備の不調や老朽化などを読み取ることができ、製造現場における新たな改善ポイントの発見や施策立案に活用することが可能である。
14年にスタートしたオムロン草津工場のプリント基板の表面実装ラインでの共同実証では、6カ月で30%の生産性向上という効果を確認した。
同工場では、ビジュアラインなどにより生産状況のバイタルともいえる「生産ラインの波形」で表現し、熟練の経験・技を必要とする生産ラインの把握が、誰でも簡単にできるようになったという。
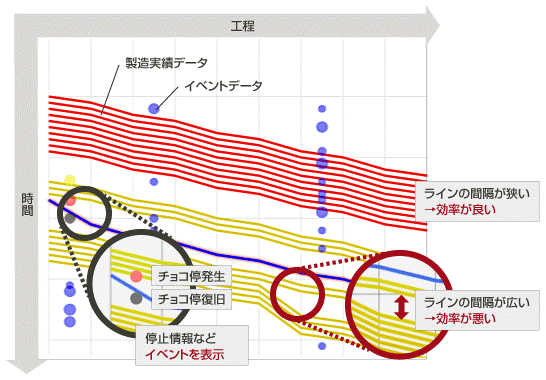
2017年8月10日 日本物流新聞「Start Up 中小製造業のIoT」に掲載