筆者は、2016年4月から経済産業研究所RIETI(2018年4月からは日本生産性本部JPC)において、「IoT、AIによる中堅・中小企業の競争力強化に関する研究会」を主催してきた。
研究会では、これまでモデル企業9社に参加いただき、研究会がモデル企業に対して、アドバイス・コンサルティングを行う代わりに、「試行錯誤のノウハウ」を公開していただくことを条件に研究会に参加していただいた。公開するのは、モデル企業による検討のスタートから途中経過の試行錯誤から最後までの企業ノウハウである。それらは、通常「企業ノウハウ」として企業内にとどまっているものである。日本国内の中堅・中小企業の競争力強化を図る公益目的の研究会である。
本研究会で採用した手法は、MBAプログラムで用いられている「ケーススタディの積み上げ方式」である。企業経営を成功させる定石はない。MBAで学ぶのは、多くの成功事例のケーススタディである。同様に、中小企業へのIoT、AI導入で成功する定石はない。そのため、成功事例のケーススタディを学ぶしかない。だが日本では、中小企業のIoT、AI導入の成功事例はほとんどなく、しかも、もしあったとしても企業秘密として公開されない。日本に現存しないのであれば、自分で作っていくしかないと考えた。
今回公開する企業ノウハウは、2016年度のモデル企業である「ダイイチ・ファブ・テック」の事例である。
Ⅰ.会社概要
1. 会社概要
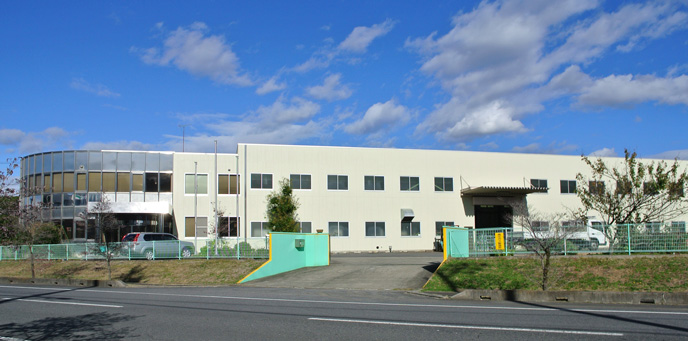
- 所在地
- 茨城県水戸市谷津町1-72 水戸西流通センター内
常磐高速 水戸インターから5分 - 設立
- 創業 1965年1月5日
法人化 1970年6月26日 - 資本金
- 1,000万円
- 従業員
- 25名
- 取引先
- 株式会社日立ビルシステム
フォルム株式会社
水戸暖冷工業株式会社 - 扱品目
- 昇降機部品、トラックフレーム部品、空調機部品
- 経営面
- ①着実な経営と進取の精神
- 生産面
- ①変種変量生産に柔軟に対応 ②短納期注文に対応
- 技術面
- ①最新鋭デジタル板金加工機による高精度・高速加工
ドイツ・トルンプ社製8kWディスクレーザ、YAGレーザ複合機、ベンダー(4080mm)
三菱電機製3次元レーザによる板金6軸加工
②CNC機はすべてCAD/CAM装備
③薄板(0.1t)から中板(19t)までの幅広い板金・製缶加工
④ステンレス、銅、純アルミ、真鍮の板金・製缶加工
⑤その他広範な機械加工に精通 - 品質面
- ①ISO9001:2015 認証(2000年)
- 環境面
- ①KES・環境マネジメントシステム・スタンダード認証(2004年)
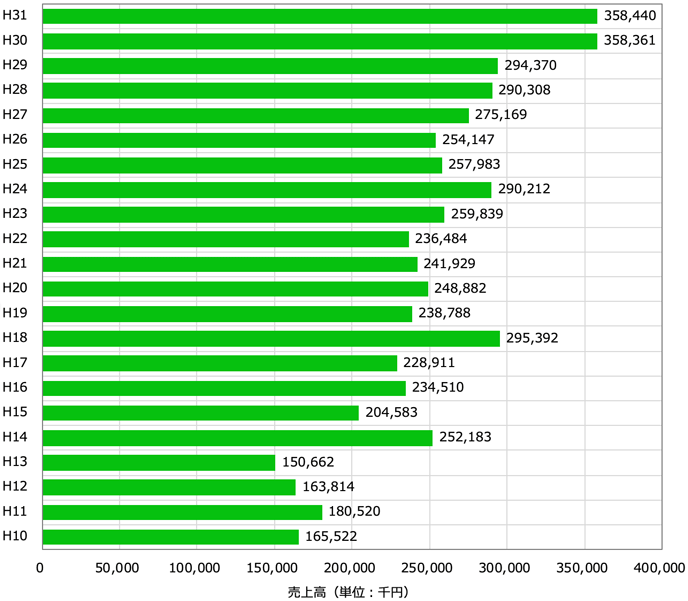
ダイイチ・ファブ・テックは、CO2 3次元レーザやYAG複合機など最新の加工技術を使った精密板金・製缶加工、プレス加工、プレス用仮型製作といった金属加工を行う部品製造メーカーである。ダイイチ・ファブ・テックは、国や地方公共団体からの公的支援で、汎用ロボットや3次元測定機を導入するなど、事業を強化している。同社がIoTを用いて目標としたのが、設備稼働率が大きく変動することで受注量が制約を受けるため、それを平準化することであった。同社の特徴として経営面では、借入れは公的資金を用いることで着実な経営を継続している点が挙げられる。今回のIoTに関する投資計画を実施する際も、国が提供する公的補助金を積極的に利用することで、堅実な経営と技術革新を並行して行っている。生産面では、顧客のニーズに応じるため、部品1個から数百個単位でも受注を行っており、また無駄な材料コストをカットし、時間短縮を可能とする製品見積もりを提供することで、製品付加価値の向上に日々邁進している。売上高推移(図2)を見れば、平成14年以降、売上を伸長させており、3億円台に到達しつつある。大量生産から小ロット生産まで、変種変量生産・短納期注文の要望に幅広く答えることが、他社にない独自の強みである。技術面では、CO2 3次元レーザ・YAGレーザ複合機など最新鋭のデジタル板金加工機を使用することで、各種材料を問わず、広範な機械加工を行っている。品質面でも、ISO9001を2000年に取得し、また3次元測定機を完備することで良質な製品の提供を実現している。
ダイイチ・ファブ・テックは近年、特に加工技術の3D化に注力してきた。それは従来の製造体制にいくつか課題があったためである。従来、金属加工は三角法図面を基に、板取をして作業していた。これは作業者の熟練に大きく依存するし、多くの時間を要していた。そこで2013年以降、経営革新計画の中で、導入したのがCADシステムの3D化である。多関節ロボットによる部品輸送、多軸制御の工作機械及び3D加工機(3次元レーザなど)の使用により、金属加工方法の3D化を実現した。これにより生産ラインでは、製品のコンパクト化・省スペース化・軽量化・複合化・省エネ化が進み、生産性が向上した。
生産管理システムについては、株式会社テクノアが開発したTECHS-BKを導入している。このソフトが優れている点は、紙媒体やExcel等で管理していた情報を電子化し検索可能となる点と、バーコードでの実績収集により工程の見える化が可能になる点である。システム導入後は、顧客からの問い合わせに、現場に行くことなく回答できるようになり、必要な図面をすばやく検索することが可能となった。
このようにダイイチ・ファブ・テックは、製造工程や生産管理システムの拡張を続けてきた。高精度・高速度加工を可能とする、最新鋭のデジタル加工機を利用し、併せて情報化による生産管理システムおよびISO9001に基づくPDCAサイクルを運用することで、顧客からのさまざまな単価・品質・納期の要望に日々応えるよう努めている。
2. 研究会に参加した動機
2.1 IoTへの期待
このように、生産システムを絶えず拡張しているダイイチ・ファブ・テックではあるが、ここ最近、改善すべき課題が見えてきた。それは工場内部の各工程を、完全に把握できていないという問題である。生産ラインに最新の技術を導入してはいるものの、各工程の作業は現場の生産管理責任者に負うところが大きい。複雑な仕事内容であっても、良い意味で、熟練を持った彼らが現場で対処できてしまう。そのため、製造ラインの情報を管理部門で収集・分析できていない。このように、工場の「見える化」が徹底できていないので、改善すべき非効率な工程を明確に把握できなかった。そこで利用可能な新たな技術を探し求めていたのである。
それというのも、昨今の製造業を取り巻く技術革新の変化には目を見張るものがあるからだ。「わが社は大手企業の要請に適宜応じていくためにも、そうした最新の技術を取り入れていく必要がある。今回IoT導入に強く魅力を感じ、導入を決意したのも、新技術を他社に先駆けて導入し、わが社の生産性改善に活用できる」と思ったからだという。
そこでまず、「IoTについて知ろう」というところからスタートした。そもそもIoTという言葉は、ここ最近よく耳にすることが多くなり、またセミナーなども徐々に行われているようだが、同社にとって、どのように活用すべきか実態が曖昧であった。
例えば自動運転技術の急速な発展により、自動車の無人運転が今後数年以内に実現すると言われている。そうした「自動化」が普及した社会が実現すれば、現在のような部品加工メーカーも大きな変化を迫られることは明らかであろう。そうした今後予測される技術革新に対して、中小企業はどう対処したらよいのか。どうしたら生き残れるのだろうか。強い危機感があった。「もっと具体的な内容を知る必要がある。」茨城県で岩本が実施したIoT講演会で話を聞いて、その思いはますます大きくなっていった。こうしてダイイチ・ファブ・テックは、IoT研究会に参加し、実際に自社へのIoTの導入を模索するに至ったのである。
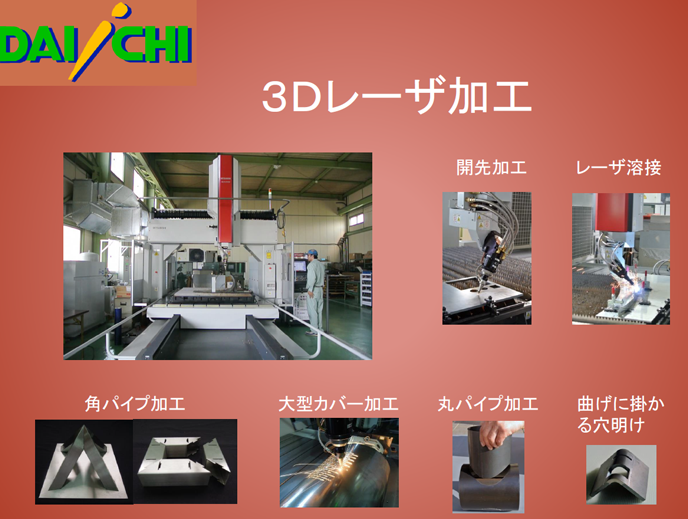
2.2 抱えていた課題
実際の生産現場に関心を持つ方々ならば、まず「IoTとは何ぞや」といった疑問や興味関心から、また少しでも「IoTについて知りたい」という思いから、アプローチを始めたのではないだろうか。もしくはIoTに関する書籍を読んだり、セミナーに参加している方々も多いのではないだろうか。研究会参加の打診を頂いた時点では、同社もまったく同じ状況であった。「IoTとは何か」「その活用法を知りたい」そうした知識欲に駆られてのスタートであった。しかしながら、IoTについて知れば知るほど、ますます現場に即した知識や、より具体的な経験談を得たいと考えるようになった。単に自主的な勉強に止まるのではなく、実際にIoTを導入している大企業と意見を交換し、アドバイスを受けることで、そのケース・スタディを自社に生かしたい。IoTに関する情報(書籍やセミナーなど)が研究会発足当時はほとんどなかったこともあり、同会へ参加したいという思いは、ますます強くなっていったのである。
研究会を通じて、ダイイチ・ファブ・テックがIoTに期待した具体的な効果は、生産管理責任者の仕事を自動化することで、工場の「見える化」を推進することであった。製造ラインで実際に動く機械や製品を、情報で管理することで、生産過程で発生する問題・急な受注なども含め、効率的な製品供給を行いたいと考えている。また上述したTECHS-BKに関しても、十分に活用できていないのが実態である。確かに作業指示書をバーコードで読み取り、進捗管理等を行ってはいるが、実績時間と標準時間のズレの原因を追求する、実績時間からくり返し品の標準時間を確定する等の使い方ができているとは言い切れない。
「モノ」と「ヒト」とをIoTを介して管理し、加工状況に応じて生産できるように、生産ラインを自動化することで、効率的な生産管理システムを運営していきたい。より具体的に、ダイイチ・ファブ・テックのIoT導入への課題を示そう。各種機械の稼働状況や進捗具合に関するデータをリアルタイムで管理できていないため、「モノ」がどこにあるのか、「ヒト」が何をしているのかなど製造部門全体の情報を一元的に管理できていなかったのである。会社全体でこうした課題に対処したいと考えていたのである。
データを把握できていない以上、現場責任者以外に誰も製造ラインの実態を把握できていないことになる。同時に、ダイイチ・ファブ・テックでは部品単位で受注生産を行っており、また特殊製品の注文にも応じている以上、特定の製品が急遽発注を受ければ、工場の生産ラインが停滞してしまうということも多々ある。こうした設備の稼働状況がアンバランスとなってしまうのは避けられない。結果として、各製造ラインで特定の作業機械に作業が集中してしまい、作業量はバランスが悪くなってしまうのである。生産ラインを見ると、一方の設備ではフル稼働状態で、また一方では遊休状態や受注超過といった光景が頻繁に見られる。製造ラインの流れが非効率的となってしまうのである。注文を受けた際や、即座に納入を求められる際、製造ラインでは特定の作業機械に大きな負荷がかかる。作業量の均等バランスが崩れるため、製造ラインが停滞してしまうのである。加工機械の負荷バランスを平準化できないことで、製品ごとに、見積もり時間と実際の作業時間との間に、ズレが生じてしまう。納期が遅れてしまうため、生産性悪化に直結する問題である。
例えば、レーザにある一定量の負荷がかかった場合、他のレーザに自動で仕事を振り分けることで作業を分散できるようなシステムがあれば導入したい。それによって作業効率の向上を図りたいと考えている。
1日の作業量を「見える化」し、工程ラインの能力を超過した場合には、自動的に作業の前倒しや、他の機械への割り振りができるような生産管理システムが望まれる。
以上を勘案すれば、同社はまず、①センサー付加工機でデータを収集・分析し、②生産管理を徹底し効率的な生産ラインを構築することで、③計画通りに生産から納期までを完遂していくことが可能となる。そして④最終的にはロボットを導入し、付加価値を高めることが同社の目標である。
3. IoT研究会参加後の事業計画
3.1 研究会でのアドバイスと軌道修正
こうして「知りたい」という動機から研究会に参加したわけだが、参加後はより実践的な意見を同社は受けた。実際の導入過程は後ほど説明するが、例えば非接触の電流計で稼働機械に関するデータを収集するなど、具体的な活動にも結びついている。IoTによる生産管理自動化実現に向けた生産体制改善のための環境が整いつつある。
すでに述べた通り、自動車の自動運転技術なども考慮すれば、数年後、部品加工メーカーの業界では大きく様相が変わることは想像に難くない。もちろん、全てが急に自動化され、人間の手がまったく入らなくなるということはないだろう。しかし、多くの加工機械メーカーは、いずれも自社加工機の性能を争っている段階にとどまっている。IoTを導入して製造工程を自動化するなどの段階にまでは到達していない。メンテナンスや本社工場と分工場との情報一元化など特定の工程や限定的な部署間でのIoT化に限定されている。
よって、まずダイイチ・ファブ・テックのような「ものづくり」を行うメーカーに求められているのは、なによりも「実際に行動する」ことであった。加工機からデータを収集し、それを生産効率化のためにいかに活用していくかが課題なのである。
3.2 研究会参加後の新たな発見
2016年における同社の経営革新計画は「IoTを活用した3Dデータ機器による非量産精密製缶の供給体制の確立」であった。これは、自動運転技術などAI、IoT技術が発展していることから、「変革の波」が近づいているという危機感と、さらなる発展を目指してこうした技術を活用しようという意欲があったためである。自社の課題追求に加えて、研究会で「IoT実践者」の生の声を聞くことで、新たな課題も発見された。ダイイチ・ファブ・テックの視察や研究会で指摘された課題は何かというと、生産ラインで発生している問題の原因が、「モノ」に起因しているのか、「ヒト」に起因しているのかを追求し、区別していく、という点である。そのためには、システムの効率的な運用と費用対効果に応じた投資計画の実施という判断基準に注意を払う必要がある。
発生している問題の原因が「モノ」であれば、前者の生産ライン・生産管理システムを改善する必要がある。まずは同社ではそれまでに導入していた生産管理システムを完璧には使いこなせていなかった。いまだに全部の機能を使いこなすまでには至っていない。日立製作所の技術者から、生産管理システムについて指摘を受けた。「現状の『モノ』と『ヒト』の動きが把握しきれていない原因も、このシステムを理解することで少しでも解消できるのではないか」とのアドバイスを受けた。営業戦略についても、三菱電機の方から同様の助言を受けている。営業戦略に利用した情報を収集・蓄積していくことを薦められた。「機械設備での活用は進みつつあるが、多方面でもうまくアピールしていくべきだ」との指摘も受けた。設備の潜在的な生産能力をしっかりと引き出した上で、稼働設備から抽出したデータの分析を行い、生産の流れを一層改善していく方法を模索していくことが求められるのである。
生産ラインで発生している問題の原因が「ヒト」であれば、どうすればよいのか。こちらが後者の費用対効果に関する視点を意識する必要がある。既存の生産システムを効率的に運用していくことと併行して、その限界を把握して、「ヒト」の管理を徹底することで対策を峻別することもまた重要なのである。
例えば、IoTを使って工場ラインの進捗などを管理しようというようなことは、実は人間が行った方が効率的で、費用を安く済ませる場合もある。実のところ同社も、IoTが単にセンサー付加工機によるデータ収集に止まっていてはおかしい。収集したデータを何とか活用したいという思いから、作業量の自動振り分けについては、「AIもどきの自動システムがあればいいな」と考えたこともあった。IoTデータを利用しつつ、プログラムされたAIを活用し生産工程の割り振りを効率的かつ迅速に行うようなソフトである。同じ工程をいろいろな機械で加工できるようになったが、工程の混みぐあい、効率性を勘案し、生産計画を立てるのは小規模工場に集まるヒトの能力を超えている。本格的なAIではなく、あらかじめプログラムされたAIを活用し生産工程の割り振りを効率的かつ迅速に行うような生産管理ソフトである。
こうしたAIは、大企業のIoT導入事例を見れば、複雑かつ判断が必要な作業工程の自動化に最適であるようだ。確かに高度なプログラミングのスキルや人工知能などの活用が昨今増加している。しかし、そうした技術には多額の費用がかかり、またその技能を導入するには高度なスキルが必要である。あくまでも「大企業向け」である。対して小規模企業では、中長期的な投資計画は資金が限られているため容易ではない。無理にそうした技術を導入しなくても、人的管理をまず徹底して行い、ヒューマンエラーを減らしていく方が割安に済ませることができる。依然として人間が行ったほうが、コストを割安に抑えることが可能なものもあるので、判断を要する作業などは「ヒト」に任せるべきだと再認識した。投資をしてどのくらい回収できるかを考えれば、大企業であれば人も資金も豊富であるかもしれないが、小規模企業にとっては資金面で限界がある。「どこまで資金を投じ、どこまで実行したらいいのか」と考えた場合、なかなか大企業のような導入事例を即採用することはできない。研究会での指摘を受けて、同社は実現可能な範囲で、稼働データの収集とIoT技術の修得を行い、工場の「見える化」を実現していくこととした。そのため、IoTのスキルを学ばせるため、社員への人材教育を行った。その上で学んだ技術をもとに稼働率データ収集を開始し、活用に向けてさまざまな取り組みを実施したのである。
4. IoTの活用による課題解決へのアプローチ−初年度の取り組み−
以上を踏まえて、闇雲に投資対効果の分からない高価な技術を導入するのではなく、ハイエンドな技術は次の課題に回し、まずは身近な技術の利用を進めることに決定した。それにはIoTによる作業工程の自動化とマンパワーの管理による工程の改善とをすみ分けることが重要な対処法である。企業のIoT化には、データを収集、分析することで十二分に吟味し、生産プロセスの問題点を特定する必要がある。しかし、「どのようなツールを使い、どのようなデータを取得すればいいのか」という点に苦戦していた。具体的には、ミーティングでその日の作業計画や配送予定を確認し、顧客からの催促や、急ぎの作業などの情報を徹底して共有することで人的なミスを解消していきたいと考えている。ダイイチ・ファブ・テックでは1つの機械に1人の作業者がついている。作業者は合計20人である。一人ひとりの作業者は作業指示書通りに、マネージャーの指示に従いながら割り当てられた業務を進めていく。20人が独自に判断して作業を行う場合、不意の変化には、なかなかうまく対応できず生産性が低下してしまう。そのため、この20人を管理するマネージャーが生産工程の進捗において重要なファクターとなる。このマネージャーは各作業の知識を豊富に持っており、状況に応じて判断を行っている。AIなど導入しなくても、このマネージャーが見て即座に正確な判断ができるように、データ管理を活用していきたい。リアルタイム生産ライン調整は、「ヒト」の面からも考えていきたい。
実際に行った投資内容をご説明しよう。具体的にダイイチ・ファブ・テックの生産設備IoT化には、何よりも稼働データを収集することが必要であった。そこで初年度に優先して行った取り組みは、IoT化を実施するための知見を学び、実際に取り込むことであった。新しい技術を学ぶため、茨城県工業技術センター(現在は、茨城県産業技術イノベーションセンター)にお手伝い願った。同センターでは、「企業等IoT自動化技術導入促進事業(茨城県委託)」の一環として、IoTの知識や経験のあるプログラマーやデータサイエンティストなどの専門家を派遣し、またIT化・IoT化に関するセミナーを行っている。これまでもこうしたセミナーに参加していたこともあり、生産管理システムの共同研究が決定したのである。
工業技術センターが提供しているのは、次世代技術活用人材育成事業の応用過程研修「工場設備の見える化を睨んだIoT化技術の習得コース」である。研修は講義・実習・データ収集に分けて修得する形式である。このコースに参加することで、IoT技術に関する人材育成を行い、習得した技術でダイイチ・ファブ・テックの課題を解決することが目的である。IoT化に必要な技術・計測手法を実際に学び、課題を解決できるよう、データ管理システムを構築可能な人材の育成を目指した。また得られたデータを定量的に分析することでIoT化の有用性・導入効果を明確にすることを目標としたのである。研修では、「どの加工機のデータを、どうやって収集していくのか」を決定するため、データ収集項目の整理・収集に必要なセンサーの選定・計測ユニットの開発および計測手法の検討を行った。
同社はCNC加工機(数値制御工作機)を主体としつつも、可能であれば手動で動く機械についても取り上げたいと考えていた。そのため、データを取得する加工機はレーザ、プレス、ベンダー、溶接ロボット、ボール盤などとした。レーザ、プレス、ベンダー、溶接ロボットは、工業技術センターがすでに開発しており、ダイイチ・ファブ・テック自身でも3カ月ほどで電力使用量を測定するために「無線LANを利用した非接触の電流計」を活用し、稼働率の測定に成功した。ボール盤はリミットスイッチを使用した打点数測定装置を製作することを予定していた。また集めたデータを解析するソフトをExcel VBAで作成することで、生産ラインの問題を改善していきたいが、「無線LANを利用した非接触の電流計」では稼働状況は把握できるものの、具体的にどの製品を加工しているかはつかめないので、別途バーコード等での製品名の読み込みは必要となる。システム・センサーについては、比較的設置が容易な、電流値測定モジュールを選択した。これは以前、電力使用量を測定した際に利用したシステムをそのまま応用することができたためである。非接触の電流計を加工機の配電ケーブルに接続し、無線LANでパソコンにデータを送信することによって、稼働時間データを自動で収集することが可能となったのである。このように工業技術センターの協力で工作機械6台はすでにセンサーの取り付けが完了し、研究会に参加したことでデータでの管理が実現したのであった。
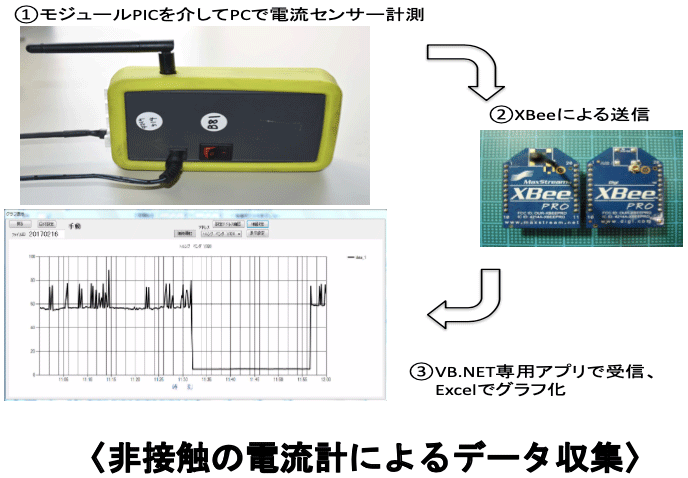
導入したIoT技術の具体例を1つご紹介しよう。図4は、ベンダー作業での電流測定プロセスを示している。まずベンダー作業で発生した電流を測定する。この計測によって把握できるのは、「どの工程が、いつ、どれだけの電流を必要としたか」というデータである。計測後は、モジュールPICに組み、無線通信規格のXBeeでデータをパソコンに送信する。続いて送られたデータをVB.NET専用アプリで受信し、Excelでグラフ化するのである。
稼働データの抽出ができたことで、TECHS-BKとの連動が次年度以降の課題となった。バーコード作業実績と電流測定値から生産ラインの動きがデータで把握できれば目標に近づく。現状、すべてのデータをリアルタイムで管理する段階までにはまだ到達していないが、各設備の情報を少しずつ収集できている。電力測定が可能になったので、稼働状況が把握できるようになった。研究会参加初年度は、可能ならば順次データ取得方法を拡大していくという段階であった。その甲斐もあって、工場各部の流れが徐々にデータとして「見え」始めてきたのである。
5. IoTの活用による課題解決へのアプローチ−次年度以降の取り組み−
次年度以降の計画では、はじめ初年度での「工場の見える化」に向けたデータの収集を徹底しつつ、分析・活用段階への移行を目指した。レーザ・プレス・ベンダー・溶接ロボットなど各種加工機に、前述した無線LANによる非接触の電流計を取り付け、合計7台の設備がどれほど電気を使用しているのか=どれほど稼働しているのか把握できるようになったのである。要・不要な設備がどれか選別するのがなかなかに困難だったが、データを収集することに成功したダイイチ・ファブ・テックは次の段階に移った。同社の次の取り組みとは、収集したデータをどのように活用するのかについてであった。測定した各稼働データは、オンラインでパソコンに送付し、早速分析を行った。そこで利用したのはテクノア社が提供する生産管理ソフトであった。プールしたデータをもとにこうしたソフトを組み合わせることで、「工場の見える化」を目指したのである。具体的には、データをグラフ化することで、その問題点を特定し、現場の作業員との情報共有を通じて、仕掛品の滞留を改善したのである。1つの稼働設備に仕掛品が滞留することがないように、データを確認しながら分散・分配していくことが可能となったのである。つまり、受注案件に対する各設備の作業負担率を明瞭に把握可能となった。こうして「工場の見える化」で把握された分析結果を基に、同社では、社員と作業状況およびそれに応じた作業方法を朝礼で打ち合わせるようになった。事後的にデータを確認するのではなく、分析結果を基にリアルタイムで設備の負担率を効率的に調整できるようになったのである。情報を共有することが同社の課題解決および生産性向上に至ったといえる。
IoTを過度に意識せずに、ヒトとモノの流れを適切に管理するツールとしてとらえることで、工程内納期の遅れを改善することにつながったのである。初年度で苦戦しつつもデータを取得・分析してみて初めて、“ただデータをとるだけでは生産性に直結しない”ということをダイイチ・ファブ・テックが実感した瞬間であった。こうして同社は、データの一元管理が可能となったことで、生産過程における設備稼働情報を把握できたのである。
2019年度に同社が取り組んだのは、データを取得する設備の選定を通じた設備稼働率の活用である。設備の選定を実際に行ってみると、稼働率を収集していた設備7台のうち、初工程のみの把握で十分であることが判明した。データの分析をするにあたり、結局、初工程におけるレーザ2台(トルンプ製・三菱製)と複合機1台の稼働率だけ把握し、調整すれば、溶接・ベンダーといった残りの工程は、一気通貫で作業が可能であるためである。つまり、作業全体をみるとレーザによる切断といった初工程では、長い作業時間を要するので設備の稼働状況が大きくアンバランスになるから、この工程の状況を把握・調整すれば、作業全体の管理につながると判明したのである。こうして当初は稼働している設備のうち7台のデータを採取していたものの、仕掛品が多かった初期工程に限定することで稼働率の調整を行うように作業体制を整えたのである。またTECHS-BKおよびサーバーをバージョンアップすることで稼働状況の把握が一層容易になると、負担率の高い設備が稼働する作業工程に対して、的確に人員を充当できるようになったのである。これは工程内納期の遵守を徹底することに大きく貢献した。これまでの受注時に事務員が計算した生産計画の作業指示書では、リアルタイムで作業状況を把握できていなかったが、グラフによるヴィジュアル化で、生産管理の精度が大幅に向上したのである。従来、作業遅れの原因を即座に特定できていなかったが、工場内の見える化が推し進められたことで、朝礼を通じて情報を共有し、作業人員の振り分けが精緻に実施できるようになった。事実、2018年度は作業量が増えたにもかかわらず、従業員の人数は増やさないまま納入することができた。これは生産性が向上した所以であるといえよう。
この他にも受注案件の効率的な管理を実現するため、バーコードの導入を図った。バーコードを読み込むことで、例えば現在すでに検査工程まで終わっているのか、もしくは納期がどれくらいになりそうなのかといったリアルタイムでの作業状態がすぐに確認できるようになったのである。顧客からの問い合わせに対するレスポンスの質が高まったのである。

こうした見える化したデータを具体的に活用していくために、現在3つの取り組みを行っている最中である。1つ目は非効率性を縮減するため5S計画を実施している。チーム化を進め、範囲・ローテーションを設定することを通じて周知徹底を行っている。また2つ目は2017年度補正ものづくり補助金を利用した、非量産向けマシニングセンター用ロボットシステムの開発である。人材難により工場内作業効率を改善するため、現在手作業で行っているタップ・ザクリ・リーマ加工作業を、マシニングセンターを利用した多品種少量生産向けロボットシステムを開発し、全面的に機械化を目指している。3つ目は、2018年度省エネ補助金の利用である。レーザ加工機・照明・変圧器更新による省エネルギー事業を本社工場で推進していくため、高効率の変圧器へと設備を更新し、電気量の大幅な削減を図るという。
6. 導入の成果・結果
積極的な投資はもちろん実施したいが、技術導入というものはすぐに効果が出るわけではない。そのため短期的なリターンは考えておらず、長期的な視野で経営方針を決定したいと同社は考えている。研究会参加初年度は、市況からみて投資はできそうなので、積極的にタブレット等の導入などを実施した。現段階では、センサーをつけ、電気使用量を把握しているだけなので、目に見える効果は出てはいない。そこで仮に、データから作業工程を改善することで、稼働率が上がった場合に得られる効果について試算を行ってみた。IoT導入を計画した当初の試算では、稼働率の上昇によって生じる利益は次の通りである。これまで生産現場では、正社員14人、パート6人が作業している。労働時間をそれぞれ8時間、6時間とした上で、稼働率を5%改善したとすると、1日当たり7.4時間の削減が可能となるわけだ。実際のところ、データの共有および作業工程の最適化を通じ、納期の管理・調整が可能となったことで、受注量のキャパシティを拡大することができた。この結果、景気拡大による受注量増大という波を受けて、売り上げが3割上昇し、9,000万円の増益となったのである。投資に要した費用は、取り付けたセンサーおよび付属機器だが、これは公設試験研究機関の器具を利用していたため、無償であった。収集したデータの活用で大幅な増益を実現した事例といえよう。
データを測定し、蓄積したのはよいのだが、どのように利用していくのかという課題は、依然として残ったままである。目的のないデータ収集はまったくの無駄であるので、まずは収集したデータを加工し、潜在的な製造ラインの問題を把握していきたい。
次の課題としては、以下の3点を計画中である。1つ目は、加工機から収集した稼働率データと作業指示書とを連動することである。今後は各工程における稼働データの収集を行っていきたいという。VB.NET専用アプリで、作業指示書は生産管理ソフトTECHS-BKでパソコンへと取り込みが終了している。両者を照合することで、作業工程の「見える化」はもっと徹底的に実現するであろう。データベースと各生産管理システムが連動するよう、システムの再設計にも挑戦したいという。最終的にはデータによる部分最適で満足するのではなく、各工程の最適化を図りつつ、全工程一気通貫の全体最適化を模索していきたいという。そこでは、例えば非量産向けマシニングセンター用ロボットシステムといったロボットの導入を検討している。このシステムが開発できれば、現在手作業で行っているタップ・ザクリ・リーマ加工作業をマシニングセンターを利用して非量産の多品種生産が可能となる。投資額は1千万円ほどを見込んでいるが、2017年度補正ものづくり補助金を充当する計画で目下進行中である。他にも2018年度省エネ補助金でディスクレーザ加工機・高効率LED照明・高効率変圧器へ設備更新するなど機械化・ロボット化を通じた全体最適を目指すという。
2つ目は、データの利用方法である。「データ収集」と「データによる見える化」との間にはギャップがある。データをいかに活用するのかは難しい。優先的な活用計画は、やはり作業量の負荷バランスを分散するシステムの開発である。現在、CAD・CAMを製作販売しているITベンダーと、リアルタイムで生産を最適化するソフトウェアの開発を相談中である。このソフトの開発が進めば、例えば、特急品を受注した場合、受注処理が終わるや否や、特急品の納期に間に合うようにリアルタイムで作業指示が自動で変更される。同じ工程加工のできる加工機が複数ある場合、仕事がはかどっている機械にリアルタイムで優先的に仕事を割り振ることが可能である。その際、データの閲覧やカメラによる視覚情報の利用が容易にできるよう、タブレットを試験的に3台導入した。現在はまだ使い始めたばかりであるが、パソコンでなくても作業状態に関するデータを直接TECHS-BKで閲覧できるようになった。製造ラインの不具合や停止の原因など、一律かつ視覚的に情報共有できれば、適切な処理ができるだろう。QRコードの読み取りなどにも活用していきたいという。また、発注親会社や分工場との間にも稼働データを活用したいと検討している。向こう1週間程度の各機械稼働データから勘案し、「いかに親会社の納期を遵守していくのか」「分工場との作業分担は現在可能なのか」といった対応も可能となる。発注会社・分工場との関係も改善できるよう、生産管理ソフトの連携を高めていきたい。他方、データの一元化が進んだことで、複合的な利用も可能となっている。見積もり時のデータと実績のデータのずれで把握される標準時間を把握可能となったので、実際にある作業工程でどれほどの収益性があるかなどが計測できるようになった。これは顧客との交渉時に活用する余地が多分にあると考えられる。
3つ目は、製造部門以外へのデータ利用である。上記の通り、同社でのIoT技術は現状では、製造部門への利用が主である。そこで、収集したデータをより活用するために、営業や社内教育の場に導入することを検討している。営業面については、VPN(Virtual Private Network)を利用して社内LANを活用したいという。例えば、営業の際に製品加工の様子をビデオで見せるだけでなく、その時点における実際の生産ラインの情景をオンライン映像で提供することができる。「どのような加工をしているか」をダイレクトに見せることで、製品の視覚情報を顧客に伝えることが可能となる。あるいは社内の生産管理ソフトにアクセスし、各工程の混雑状況を見て納期回答を行う等、即座に顧客が求める情報を提供可能となる。検討段階であるが、ダイイチ・ファブ・テックは非量産型の生産体制であるので、「1ロット何百個」という注文を受けることもある。こうした受注には、社員が帰った後に自動で加工機をリモートで操作したり、ネットを介して状況を見たりなど、多用な活用方法を実践してみたいという。しかも社内の加工データはすべて3DCADで製作し、また溶接のロボット、搬送用ロボットを含めすべてのCNC加工機にCAMを完備しているので、IoTの活用も容易と考えられる。
これら一つ一つはすでに実証段階にある。このようにIoT技術を社内に導入する過程で、いろいろな課題に挑戦していきたいという。念願であった、作業量の平準化を含めた社内生産システムの情報化・IoT化は、あと一歩のところにまで到達していると考えられる。
同社の最終的な目標である設備稼働率の平準化につなげるため、さらなる情報化への投資を実現することである。生産管理ソフトを今期バージョンアップしたことを踏まえ、タブレット3台を導入した。これにより、パソコンでわざわざ入力管理をする必要はなく、より効率的なデータの活用が可能であると思われる。また最近、経済産業省が推進しているQRコードを利用することも今後の課題と考えている。
さらに中長期的な計画として、今回社内に取り入れた工場内のシステム環境を参考に、ソリューションとして提供していく、システム・インテグレーションに参与していきたいという。このための準備として、特に製造業のIoT化に特化しているドイツの生産管理システムについて研究すること、カメラの導入による画像認識機能を稼働設備に取り付けることを計画している。
また今後は集めたデータを「どのように利用していくのか」という点に加えて、各工程の部分最適ではなく、全体の最適化を目指していこうと同社は考えている。これを実現するにはロボットの導入を行い、生産工程を一気通貫にスムーズに実現していくという。「工場の見える化」を実現することで、ダイイチ・ファブ・テックの他社に負けない高付加価値の製品供給に期待したいという。
具体的な施策として、ロボット化と高速ディスクレーザの導入、評価式教育訓練の再開、新卒者教育を通じて不良削減を目指していくという。
ダイイチ・ファブ・テックが上記のデータ収集・加工と並行して取り組んだのは、既存の3D機器を中心に生産体制に、IoTによる自動化を組み入れることであった。IoTは単に導入すればよいわけではなく、手段として効率的に活用できるよう、自社の課題と向き合うことが必要である。人材育成・データ収集と段階的に生産現場改革を行う同社の成長は、IoT導入プロセスの1つの指標となるだろう。
【ダイイチ・ファブ・テック談】
IoT研究会を通じて、大手ベンダーの大変素晴らしい技術を拝見した。しかし実際、われわれ小規模企業の立場で意見を言わせていただけるのであれば、もう少し安価に導入できる技術を探し出していくことが重要であると思われる。自分たちと同じ企業規模の企業が採用しているIoTについての成功事例があれば、より一層参考になるのではないかと思う。現在のIoT化の流れの1つの特徴は、センサー類を含め安価に構築できる可能性があることだと思う。やはりデータを収集して、活用して経営を効率化しようという路線で、企業がIoT化を行うには、ビッグデータの収集方法でも、そのために要する資金でも限界がある。センサーをつけるなど、IoTを導入するのは誰でも発想自体は容易にはできる。ただし、それだけでIoTを導入したことになるのかといえば、データを活用できていない以上使いこなしているとはいえないだろう。いまだにわが社も使いこなしているという実感はない。センサーを導入し、データを収集して初めて、それをどうしたらよいのかというところにたどり着く。そしてそこからも活用するまでには時間が必要となる。データを収集したことで少しは漸進したと安心してしまってはだめである。そのセンサーを使って「仕事をどうやって効率的にこなすことができるのか」などを念頭に置く必要がある。IoTを導入しようと考える企業の方々は、まず本当に今ある生産管理システムを100%活用することに注力してほしい。ある程度の課題は、それだけでかなり解決できると思われる。わが社でも同様である。考えれば考えるほどに、「多品種少量受注生産工場向けのIoTとは具体的にどのような設備・技能で行うのが効率的なのだろうか」「本当にIoTを活用して、投資リターンを得るにはどうしたら効率的なのであろうか」という疑問が頭をよぎった。いまだ正確に理解できているのかと疑問も残る。こうした問題点や疑問は今後も考えていきたい課題である。IoT技術は最近ますます周知度が高まったように思う。農業分野でもIoT化が進んで生産が効率化していると耳にしたことがある。売上に直結するような産業もあるようだ。対して小規模部品加工メーカーでは、IT化すらも進んでいないのが現状である。ここをどのようにIoTで効率化していくのか、課題を模索していきたい。どこに課題があるのかを見つけないことには解決策は見えてこない。課題を絞って、データから解決策を模索していきたい。
IoTを導入するためだからこそ、むしろ人的管理を行うことが重要であることが改めて分かったという。現場労働者が自身でも「考える」ということが重要なのである。手段であるIoT化を活用していけるように、その「考える」力を強化していきたいという。5S(整理・整頓・清掃・清潔・躾)などのスローガンを徹底し、職場環境をも含めた生産ライン改善を今後の目標として目指していくという。
特に小規模製造業は真剣に取り組まなければならない。3次元プリンターの誕生などを見るに、旧来の部品加工メーカーなどは不要になるという時代が到来しつつある。現在はまだ人の手などがどうしても必要であるが、早晩、そうした技術的な問題も改善され、全て自動化されかねないと思われる。ダイイチ・ファブ・テックのような加工業者は、5年後、10年後にどれほど生き残ることができるのだろうか。岐路に立たされているということを自覚して動向を注視する必要がある。最新のIoT技術に乗り遅れることなく、自社に合った形で昇華し、生産現場に活用していきたい。
Ⅱ.株式会社ダイイチ・ファブ・テック 代表取締役 金森良充氏および同社事務グループリーダー 照沼友珠氏 へのインタビュー
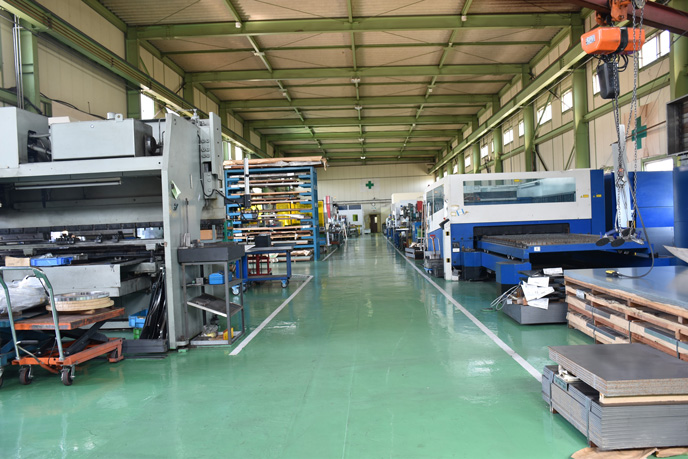
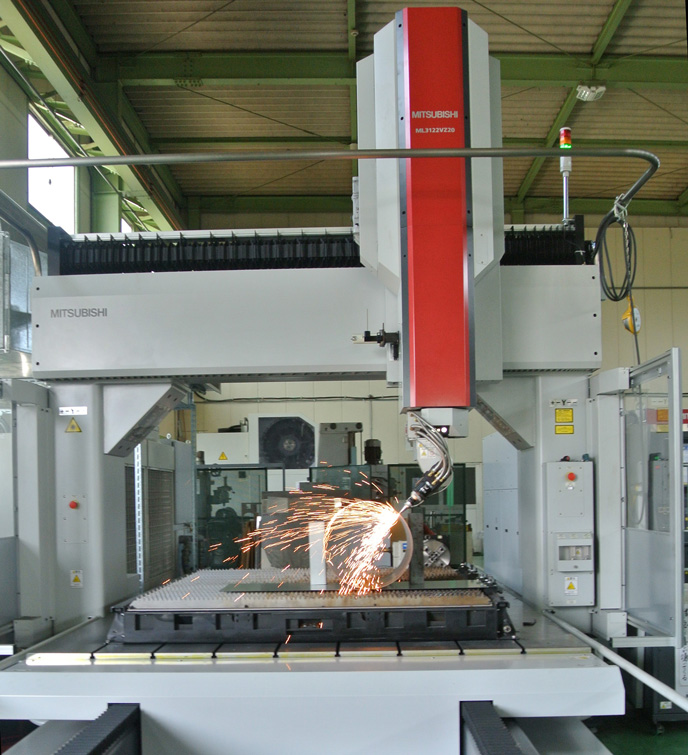
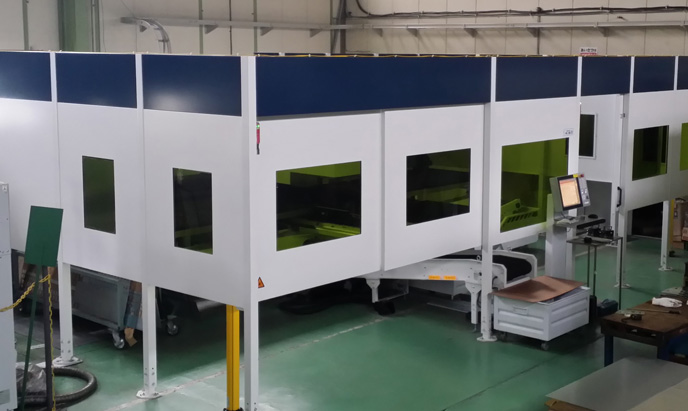
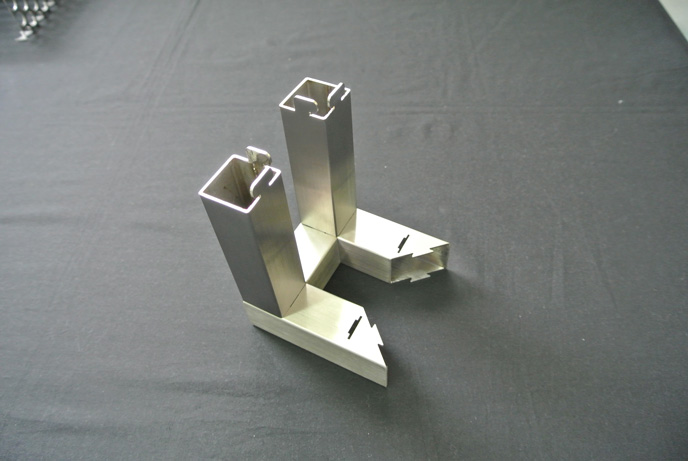
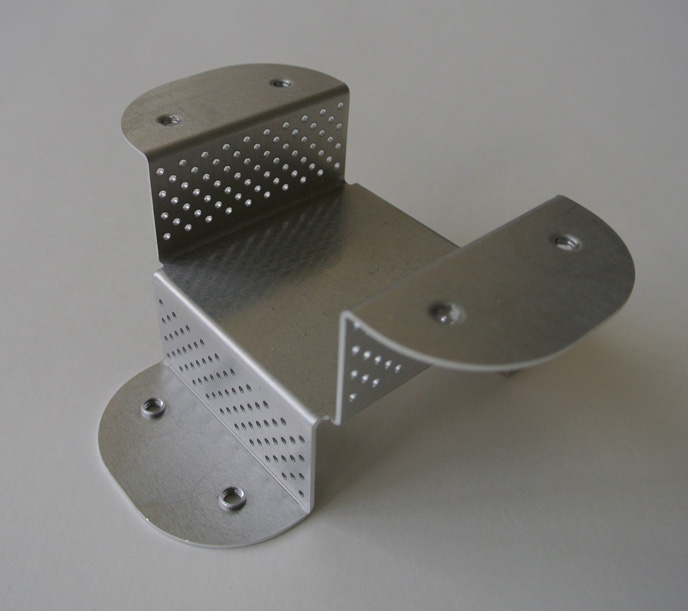
IoT導入の進捗状況
非接触型の電流計で設備稼働率の計測を始めました。当初は、7台でやっていましたが、初工程の稼働率だけ取れば構わないので、今はトルンプのレーザと複合機と三菱の3次元レーザの計3台を計測し、その数値を朝礼で報告しています。
非接触の電流計で稼働率を計測すると、問題が別なところで発生しました。初工程に関しては稼働率を上げたほうがいいのですが、残りの設備は稼働率を上げるよりは一気通貫でいかに速く納品まで流していくかが重要であることが分かってきました。
今は3台のレーザのなかでも、トルンプが混んでいます。トルンプの場合はパレットチェンジャーがあるので、ほとんど止まらないで、8時間ぐらい稼働します。
工場の中にある設備は全部で30台ぐらい。その中で計測しているのは3台で、その3台は初工程です。最初の工程の稼働率を上げたほうがいいと思います。これから30台計測しようという考えはありません。最初の稼働率を上げれば、後半はそのまま流れます。
社内LANを引き直したので、工程内納期の遅延がとれるようになり、どこが混んでいるかがグラフでわかるようになりました。1日ごとに、その日はどこが混んでいるか。要するに混んでいる工程があったら、混んでいる工程に人を充てるか、製品を分割して作るか、です。
工程内納期は、その工程を何日までにやるということで納期をつけています。今までの納期遅れというのは、最終的なお客さんに対する納期遅れです。その前に工程内の納期を決めていて、そのとおりに終わっていれば、本当はお客さんに迷惑をかけないことになります。
基本的には1日1工程というふうに決めていまして、検査日で一応バッファーとして3日とっています。最後はお客さんの希望納期で、検査で3日とっていて、製品によって、レーザ、ベンダーとか、溶接とか、いろいろな工程がありますが、それぞれ1日1工程としています。そうすると、逆算して、例えばレーザが初工程だったら、その日にちまでに完成してくださいという情報が作業指示書に表示されます。
また、今まで初工程でトルンプのレーザからやっていたものを、他のレーザでできるものはそちらに回したりするようになりました。
これまではそういうことができなかったのです。どこか混んでいて、そこがネック工程だったら、そこに仕掛品がたまっていることが、目で見てわかるのですが、それがグラフでちゃんと分かるようになったということです。
外部から仕事を受注したときに、まず事務グループが作業指示書を作ります。今まではそれは紙で出ますが、グラフでは見ていなかったので、現場の作業者もおそらく自分でどのぐらい遅れているのか、把握が難しかったと思います。
作業指示書を作る際も、本来ここから回すところを別なところから回すとか、そういうふうなことを、事務グループはそこまではしません。
工場内に別な生産管理者がいますので、その者が作業指示書を見て、分けるという方法でしたが、グラフ化されることで、遅れが減ってきたとか増えているから回そうとか、毎朝朝礼で生産管理の者が確認します。
作業指示書を振り分けている者が、あるところで混んでいるとか、ひっかかっているとかいう状態を感じつつも判断が難しかったのかもしれません。紙によって振り分けがうまくいかなかった。それをグラフで見える化することによって、その者がうまく判断して振り分けられるようになったし、あと、混んでいる場合はそこに人を充てるなど。
作業者自身も今まで朝礼でグラフを見ることはしていなかったので、作業者自身が自分の工程の遅れがどのぐらいあるとか、あとは、何日か前はこのぐらいあったけれど、昨日はこのぐらいまで減ったとか、作業者自身でも確認できるようになりました。逆に言えば、それは見える化しないと、分かりませんでした。
目の前にいっぱい積み上がっていれば、すごい遅れているなというのが感覚で分かるような。ただ、自分のところは分かっても、もしかしたらほかの工程までは分からなかったかもしれません。今はグラフで確認できます。グラフで見ると、やっぱり手伝い・応援が、わりとスムーズかもしれませんね。
朝礼でグラフを見たら、これだけたまっているんだから手伝わなきゃならないかとか、やりやすくなったみたいです。人の回し方とかも。
投資対リターン
それが景気拡大の波に乗って、結果的に受注増とか売り上げ増につながっているわけです。結局、3月までだと3割ぐらい増えています、前年に比べて。売り上げが3億だから、その3割ということは9,000万増えたわけです、売り上げが。
大手だと臨時工を募集するとか、何かするんでしょうけど、うちの場合、かき集めるといったってかき集められない。同じ人数です。同じ人数で対応して3割増です。同じ人数で3割増になったのは、早く流すようになったから。もちろん、ピーク時には残業、休暇出勤が増えましたが。
納期が遅れていたら工場の中で滞留する時間が長いわけです。納期が守れたらどんどん流れていくわけだから、3割増の受注があったとしても、それは実際にそこで働いている人の労働時間が3割増えたのではない。
ちゃんと順調に流れていったからですよ。だから、3割増えても、個々人の労働時間は3割増えなかったんです。
受注が3割増えて、納期が遅れたのが半分あったかもしれない。納期遅れは同じだったかもしれないけれども、受注が増えなければ本来は納期を守れたのが、納期遅れが本来5%ぐらいだったのに、それが受注が3割増えたことによって納期遅れが半分ぐらいでキープできたということです。どんどん流すような体制がとれなければ、納期遅れがもっと増えたかもしれない。
ただ、本当の課題は、今後の課題なんですけど、改善活動によって3割仕事が増えたら、労働者に3割の負担がもろかかるんじゃなくて、治具とか、現場改善を行って、1割、2割でというふうにしたいと。
最初、研究会に来たとき話していたとおり、ちゃんとうまく部品が工場の中に流れると、たくさん仕事が来てもちゃんとこなせます。
当社は、2017年までにいろいろ設備投資しています。その設備投資が生きたという話だと思います。レーザも2017年1台ですし、その使いこなしとか、2018年もちょっとばたばたしながらでも回していましたから。
作業現場は、事務所の隣にあるとはいえ、お客様から例えば電話がかかってきて、この納期いつぐらいになりそうですかというのを確認するのに、バーコードを読んであると、自分の目の前のパソコン上で、今もう検査が終わっているから今日の便で持っていけますとかって言えるんですけれども、今までバーコード入れてくれない人とかがいたりして、そうすると、電話を受けた者が現場まで行って確認したりとかしなくてはいけない手間とかがあって、皆がバーコードを入れてくれることによって、パソコン上で確認できるようになったと思います。
そういう意味では、いろんな活動をしないと、3割増しはお手上げだったかもしれませんね。それでも何とか、苦労はしたけど、やれたという話かもしれません。それで、2017年に比べて3割増し、2017年もそんなに極端に暇というわけでもなかったのですが。
最終的に目指すIoTシステムの姿
情報化投資をして、情報システムを使って、最終的に目指す姿についてです。テクノアをバージョンアップして、いろんなデータ、例えば、工程内納期の遅れのデータとか、見積もりのときのデータと実績のデータのずれも測れるようになりました。
タブレットを3台使うようになったので、管理者が直接テクノアのデータを机に戻ってパソコンで見なくても分かる。また作業者がバーコードで入れるよりタブレットで入れたほうが早い。それがいいのかどうかよく分からないので、3台試しに入れてやってみます。
IoTの課題で将来の話というのは、2018年に勧められたカメラを入れることです。当社の場合、不良がかなり多いんです。不良の原因分析するときに、作業者も自分が不良を出したときの状況を思い出せない。だから、全部カメラで撮る。特に手元を撮ろうと思う。不良を出したときの状況を、簡単に検索できるみたいです。だから、不良を出したときに、この状況で何を考えて作業したのか、不良対策の手段として、使おうかと思っています。
ただ、一番の今の問題は、省人化ということ。ロボットで搬送して、タップとかボール盤の仕事をやるというのが、今の課題です。今ロボットの勉強会を始めたところです。ロボットシステムと、それぞれの機械装置からデータをとってくること、そしてカメラ、この3つで、大体最終的な目標というか、ゴールに近づきます。
ロボットの場合は最終的なゴールは、目標は高いかもしれません。今、自分のところでシステムを作ろうと思っているんです。自分のところのシステムを、タップと他のところも自動でできるものを作ったら、そういうシステムが売れるのかなという気もしています。
うちなんか100個ぐらいのものをロボットでやりたいなと思っているんですけど、そういう相談に乗ってくれるシステムインテグラーっていませんよね。当たり前なんだけど、1日に何百、何千個繰り返しの仕事をやるからロボットでやるんだって、そういう言い方ですよね。私は、いや、ロボットいろんなことができるんだから、多品種少量生産に向いている。
全部でトータルでの投資は、ロボットのシステムは最大で1,000万ぐらいです。タップ立てる機械が950万。カメラは500万ぐらいです。ドイツの産業用ソフトウェアが今のところ800万ぐらい見積もりもらっています。
研究会に参加した感想
研究会に参加されて、現時点、今の時点でのご感想、参加されて2年たちましたけど。皆さん感想は、研究会に参加している方の大手の方とこちらの参加している側も両方のおっしゃっているとおり、参加しなかったらなかなかやらないですよね。それで、これも決断もしないし、忙しいとずるずるという感じが強いですよね。それはある程度、てきぱきと今度のテクノアのバージョンアップですか、社内LANのバージョンアップも何とかできましたし、時々故障して今ちょっと苦労しているんですけど、でも、何とかできそうだし、次のロボットシステムとカメラとドイツの企業の産業用ソフトウェアという話もなかなか進まなかったでしょうね。研究会に参加しなかったら。
-導入に当たっては何か苦しかったこととかございますか。
苦労していることは、IT技術に関して知っている者が限られるので、仕事をしながらその者にどうやって時間を割いてもらうかだと思います。時間を割いてできればいいんだけど、できないことが結構あります。
1人分かっている人を雇えばいいんですけど、なかなか専門家は雇えない。工学部卒の者も初めて雇ったんですけど、その者はロボットのCAMとか、わりとすらすらやっています。先行的に雇用しないと、なかなかそう行かないかもしれませんね、そういう方向に。自分が進みたい方向に行かないかもしれない。
-将来的に会社の目指している方向性。
自分のところでIoTとかロボットのIT技術をものづくりの中に取り入れて、それを逆に今度は、そのシステムを売れるぐらいのところまで行けばいいと考えています。
-これまでを振り返って、言っておきたいこと
今回、研究会に参加して、会社全体で意識が高くなったのは感じていて、おそらく参加していなかったら、生産管理ソフトのテクノアも今のようにデータを吸い上げてグラフ化してみんなで見るというようなことはしていなかったかもしれないですし、そういうふうに見えるようになって、それが、それ自体は仕事を早くするとかではないかもしれないですけど、それが社員に影響を与えて、みんなの意識が高くなって、仕事のやり方とか、そういうものにプラスになっているというのはすごく感じています。
こういうIT関係のことを考えるようになって、例えば、セミナーによく行くようになりました。今までだと忙しいから、ついつい行かなかったけど、行こうかという気には前向きになりました。だからセミナーや展示会などにはちょこちょこ行っています。