筆者は、2016年4月から経済産業研究所RIETI(2018年4月からは日本生産性本部JPC)において、「IoT、AIによる中堅・中小企業の競争力強化研究会」を主催してきた。
研究会では、これまでモデル企業9社に参加頂き、研究会がモデル企業に対して、アドバイス・コンサルティングを行う代わりに、「試行錯誤のノウハウ」を公開していただくことを条件に研究会に参加していただいた。公開するのは、モデル企業による検討のスタートから途中経過の試行錯誤から最後までの企業ノウハウである。それらは、通常「企業ノウハウ」として企業内にとどまっているものである。日本国内の中堅・中小企業の競争力強化を図る公益目的の研究会である。
本研究会で採用した手法は、MBAプログラムで用いられている「ケーススタディの積み上げ方式」である。企業経営を成功させる定石はない。MBAで学ぶのは、多くの成功事例のケーススタディである。同様に、中小企業へのIoT、AI導入で成功する定石はない。そのため、成功事例のケーススタディを学ぶしかない。だが日本では、中小企業のIoT、AI導入の成功事例はほとんどなく、しかも、もしあったとしても企業秘密として公開されない。日本に現存しないのであれば、自分で作っていくしかないと考えた。
今回公開する企業ノウハウは、2018年度のモデル企業である「野中工業所」の事例である。
Ⅰ.会社概要
野中工業所
http://www.nonaka-kg.co.jp/publics/index/
野中工業所は、自動車部品・産業用機械部品を中心とした切削、研削加工に特化した会社である。同社は半世紀蓄積した切削ノウハウを軸に、30年程前から自動化にも積極的に取り組んでいる。これまでに「高硬度材旋削の高能率(ハードターニング加工)」の考案により文部科学大臣に表彰されたこともある。この技術は熱処理品(硬度HRC65程度)を研磨ではなく、切削加工により仕上げることにある。この技術により研磨レスを実現できるという。
1. 事業所 概要
- 会社名
- 株式会社野中工業所
- 所在地
- 〒327-0003 栃木県佐野市大橋町3221-3
- 代表者
- 代表取締役 野中 修
- 設立年月日
- 昭和44年(1969年) 5月
- 資本金
- 2,400万円
- 従業員数
- 36名(社員33名、派遣他1名)
- 事業内容
- 旋削加工、MC加工
- 事業分野
- 輸送用機械器具製造 日本標準産業分類 31
自動車部品、産業機械部品 - 工場規模
- 本社:敷地3,978㎡ 建物2,748㎡
2. 沿革
- 昭和34年4月
- 埼玉県加須市にて創業(小型モータ組立)
- 昭和41年4月
- 自動車部品加工を始める
- 昭和44年5月
- 資本金1,600万円㈱野中工業所を設立
- 昭和62年1月
- 現在地に移転
- 平成元年8月
- 資本金2,400万円に増資
- 平成6年12月
- 第2工場増設(主:アルミ製品加工工場)
- 平成18年3月
- ISO9001:2000認証取得
- 平成19年10月
- 第3工場増設(主:研削加工工場)
- 平成24年6月
- 栃木県フロンティア企業 「ハードターニング」認証取得
- 平成26年4月
- 第4工場増設(主:産業用機械部品の加工工場)
- 平成26年6月
- 栃木県フロンティア企業(高硬度品切削/MC加工)認証取得
- 平成29年5月
- 栃木県フロンティア企業(切削/研削複合加工)認証取得
- 平成29年11月
- 統合ISO(9001&14001:2015)認証
- 平成30年5月
- 経済産業省中小企業IoT研究会参画
- 平成31年5月
- 設立50周年
3. 事業 ポリシー
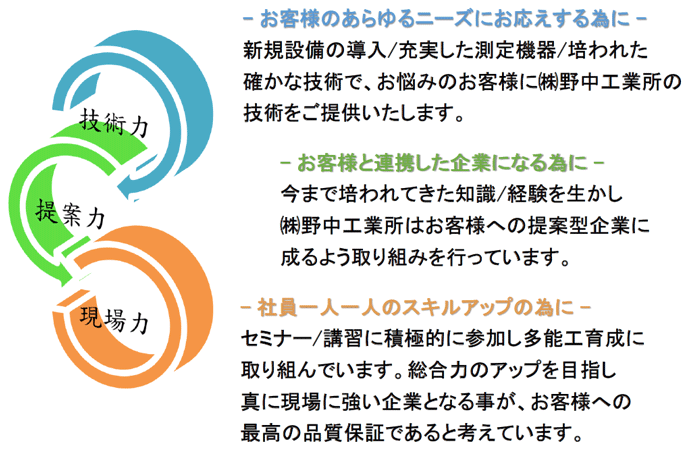
4. 売上高 人員
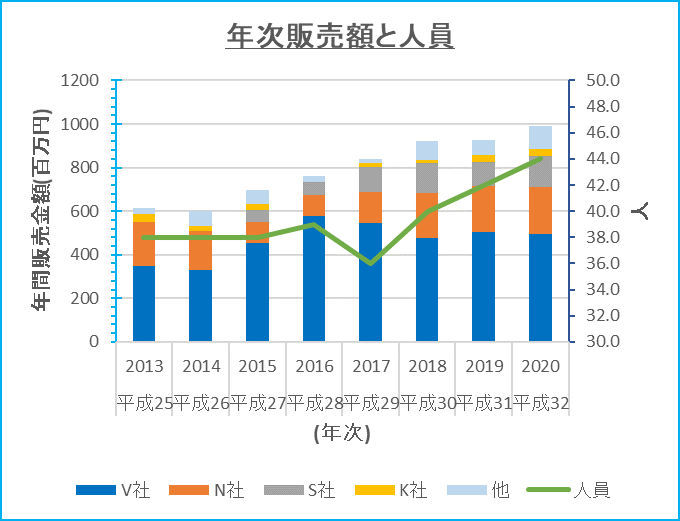
2008年のリーマンショックおよび以降の円高不況により厳しい時代を乗り越えた。現在の野中工業所は販売先比率・業界比率を再考し営業活動を継続している。また、IoT・ICT導入による生産性向上をはじめ差別化を加速するにあたり、採用も積極的に行っている。
5. 製造部門 概要
製造部は4つの工場から成り立っている。各工場の特式が下記の通りである。
Ⅱ.専務取締役 野中管理部長へのインタビュー
1. 研究会に参加した動機
きっかけは日刊工業新聞社伊藤様のご紹介でした。当時の当社は2016年4月より生産性向上を目的にIoT・ICTに取り組み始めていたものの、専門家の不足をはじめとする通信環境(職場環境:ミスト)の問題、お客様との交渉、社内標準の曖昧さ等々があり、壁にぶつかっているところでした。藁にもすがる思いで専門家にアドバイスをいただきたいと思い、参加を決意しました。
1.1 研究会へ参加以前の取り組み
IoT・ICTをツールとしてうまく活用し、ペーパーレス化、重複間接業務の削減による生産性向上を足掛かりに経営管理システム(主に原価管理、品質管理、労務管理、財務管理、工程管理等)の構築を構想していました。まずは、各システムにおける調査を行うため、市販のパッケージソフトや実際に導入されている企業様を拝見させていただいたりと検討を重ねました。しかし、確かにデータが見えるようになるものの、主目的である「生産性向上」につながるという実感が得られませんでした。そこで、自社オリジナルのソフト開発を決意し、地元ソフトウェア開発業者に協力を仰ぎ、自分たちの構想するシステムを導入することとなりました。
当初は数回の打ち合わせにより全体像、方向性を確認し「生産管理システム」、「設備信号システム」、「経営管理システム」より着手することとしました。システム開発をする中で、すぐに間接業務を削減できた事例もありますが、主システムの1つとして考えていた「機械信号でのデータ収集」で通信環境の不安定さや電気系統をいじることはリスクが大きいと判断し別案で進むこととなりました。このような方向転換は一例であり、他にも他システムで同様の問題が発生し、前提条件の見直しを含めた方向転換をせざるを得なくなってしまいました。そのタイミングでIoT研究会の存在を知り、専門家のコンサルティングを受けさせていただくことにしました。
1.2 ITベンダーを選んだポイント
「当社のやりたいことができること」を前提としました。その中で「地元中小企業がIoT・ICTを活用してさらなる可能性を模索していけるようお手伝いを」という理念を持たれ起業された方と出会いお願いすることとなりました。
もちろん、その方は前職大手製造業でシステム開発をされており、製造業の基本的考え方をご理解なされていたことも大きかったと思います。現在も積極的に議論に参加していただいています。
2. 研究会参加後の、IoT導入の検討過程
2018年10月の研究会では実際に当社までお越しいただき現場を拝見いただきました。当社の状況・環境に合った的確なアドバイスをいただきました。技術面でも対応策や処置方法等を多くご提案いただきましたが、特に、そのシステムが「何のために・誰が・どの程度の頻度・精度」で必要なのかというシンプルな問いが、当社がIoT・ICTで何をしたいのかを再考する機会を与えていただきました。
2.1 自社課題の再検討:間接業務最小化と「生産性向上」に資する「見える化」
再考の結果、間接業務の重複およびペーパーレス化を最優先項目と設定しました。すでに業務が標準化されているものほどIoT・ICT化しやすいと考えたからです。システム開発の優先順位としては「勤怠管理システム」と「製造成績入力画面」から着手しました。
勤怠管理システムはこれまで紙のタイムカードで出退勤を管理しており、タイムカードの準備、勤務時間の手集計、再チェック等を行っておりました。これを削減し間接業務の削減が達成されました。
また、製造成績入力画面を用意したことで、これまで出来高表(どの製品をどの時間で何個加工し、良品と不適合と不良品が何個あったかを示す表)を全て人が紙に書いて、その後エクセルに入力し、集計結果が合っているかどうかを確認していました。これを紙の出力・配布、記入、回収、保管を削減し間接業務の削減およびペーパーレス化を達成しました。
2.2 今後の進め方と目指すゴール
現在は間接業務最小化のために、受注管理システム、入出庫管理システム、在庫管理システムの導入です。在庫管理システムは、最終検証を5月で終わらせ、本格稼働させようとしています。
次の段階では、これまで導入したシステムを連携し、人が行うべき仕事は全てシステム化することです。「ヒトはヒトにしかできない仕事(知的労働)」をするべきであり、それこそが生き残る会社の必須条件だと考えております。また、目指すゴールはこういった技術は日進月歩です。当社としてもあくなき追及をし続けることだと思います。
2.3 投資対リターン
当初の予想では2,000万円の予算で、開発期間が2.5年で、回収期間は3年という形で最初はスタートしました。間接業務の削減、重複業務削減およびペーパーレス化によるコスト削減および生産性向上により、2,000万円は3年間程度で回収できる試算をしています。
例えば、業務削減によるコスト削減です。例えば、紙を出力する時間、回収する時間、代理入力をする時間など紙で管理していたもの、印刷、回収、保管まで含めた業務全体を換算し年間で削減される費用は最初の構想段階で計算しました。その紙のコストや短縮された時間を金額に換算すると3年で回収できると考えます。
また、ペーパーレス化により生産性の向上も見込めます。例えば、17時までの業務であれば、紙ベースの入力の作業時間を考慮して5分前に全員作業を終えないとならない。その5分間を生産の時間に充てられると稼働率の上昇が見込めます。また、集計されたデータから、各担当者の業務効率や品質状況が把握可能となります。現時点では、この結果(データ)をどう生かすかは人にしかできない領域であるため、別の仕掛けを実践中です。
3. 周囲の変化
大きな変化としては講演の依頼をいただくことが増えたことです。これまでに4回ほど、IoTの取り組みの事例として講演させていただきました。また、各公演後には懇親会もあり、若い経営者の方や先生方とも人脈ができ、お金で測れない価値があるのではないかと思います。
4. 研究会に参加しての感想
研究会に参加していなければ、これまでの課題を短時間で整理したり、優先順位を明確化したりできていなかったと考えています。特に、現時点での当社にはIoT・ICTを追求した結果、IoT・ICT以外の当社課題が明確化されてきたことが最大価値だと感じています。
5. 他社へのアドバイス
①とにかくやってみる②経営トップもしくはトップに近い人が行うこと③(システム導入の)目的を明確にすることだと考えています。
自分から情報を取りにいかない限り、自社に生きるシステムは存在しないということ。システムはあくまでもツールですが、会社の仕組みの一部となるため、経営指標に直結します。経営トップの理解なくして成功はないと感じています。