筆者は、2016年4月から経済産業研究所(RIETI)(2018年4月からは日本生産性本部JPC)において、「IoT, AIによる中堅・中小企業の競争力強化に関する研究会」を主催してきた。
研究会では、これまでモデル企業9社に参加頂き、研究会がモデル企業に対して、アドバイス・コンサルテイングを行う代わりに、「試行錯誤のノウハウ」を公開していただくことを条件に研究会に参加していただいた。公開するのは、モデル企業による検討のスタートから途中経過の試行錯誤から最後までの企業ノウハウである。それらは、通常「企業ノウハウ」として企業内に留まっているものである。日本国内の中堅・中小企業の競争力強化を図る公益目的の研究会である。
本研究会で採用した手法は、MBAプログラムで用いられている「ケーススタデイの積み上げ方式」である。企業経営を成功させる定石はない。MBAで学ぶのは、多くの成功事例のケーススタデイである。同様に、中小企業へのIoT、AI導入で成功する定石はない。そのため、成功事例のケーススタデイを学ぶしかない。だが日本では、中小企業のIoT、AI導入の成功事例はほとんどなく、しかも、もしあったとしても企業秘密として公開されない。日本に現存しないのであれば、自分で作っていくしかないと考えた。
今回公開する企業ノウハウは、2016年度のモデル企業である「日東電機製作所」の事例の第二弾である。
青木孝浩社長へのインタビュー
会社の紹介
日東電機製作所は、設立が1951年の3月で、今、69期目を迎えております。従業員は152名で、全て新卒で正社員雇用というのが特徴です。精度や品質の高い作りこみに最も気を付けており、また専門知識が必要なことから社員教育を大切にしています。
製造業としては、スタッフの構成率として、設計部門が約半分です。製造業の中では非常に設計が占める割合が多いのが特徴になっております。これは、当社がつくる配電盤という製品がほぼ全てオーダーメードですから、その都度設計をしながら製品づくりをしているため、非常に設計比率が高いのが特徴です。
また、間接部門4%で、非常に少ないのが特徴です。総務、経理、調達が含まれますが、自動化することで間接費を抑えているのが特徴です。
当社は電力会社などに納める電気をコントロールする配電盤を製作しています。取引先としては、電力会社、鉄道会社、重電メーカー、公共関係の国・市などです。
拠点は、群馬県に3カ所で、特に太田市と大泉町に集約されております。本社には総務や調達等の本社機能と技術者約70名が在社しており、工場は2カ所、イーキューブ工場、吉田工場で生産しています。
製造プロセスについて、完全受注生産、フルオーダーメードです。全てにおいて設計がかかわります。設計は、構造設計と電気回路設計と大きく2つに分かれます。構造設計は3D-CADを使ってモデリングを行い、板金CADデータは弊社板金工場に送られ穴あけや曲げ加工の機械に送られます。板金加工後は塗装とメッキが施され、組立工場に納入されます。
製造工場ではフレームの組み立て、ブレーカーやランプなどを組みつけ、配線を行います。配線は機種によりますが、多いものですと2,000本を超えるような非常に多い配線を施すものもあります。そのような場合、配線作業だけで製造工程の約7割を占めることもあります。
最終的には試験で製品仕様どおりにでき上がっているか、お客さんの要求するものができ上がっているかというのを最後にチェックして出荷をします。
特徴としては、設計から製造、試験まで、据えつけまで、全て当社社内で一貫生産を行っているところです。オーダーメードでつくるので、一個一個手間をかけながら、時間をかけながらつくらなければいけないところもありますので、上流工程である設計のデータを、下流工程の現場でいかにうまく使えるかというのが、全体を通したコストやリードタイムの削減のポイントです。設計は製品情報を一番持っている部署になります。その設計からいかに下流工程で使える情報にしていくかというのが我々の取り組みの一つになっております。
IoTの活動事例紹介2つ
(1)NT-MOLと呼ぶ総合生産システム
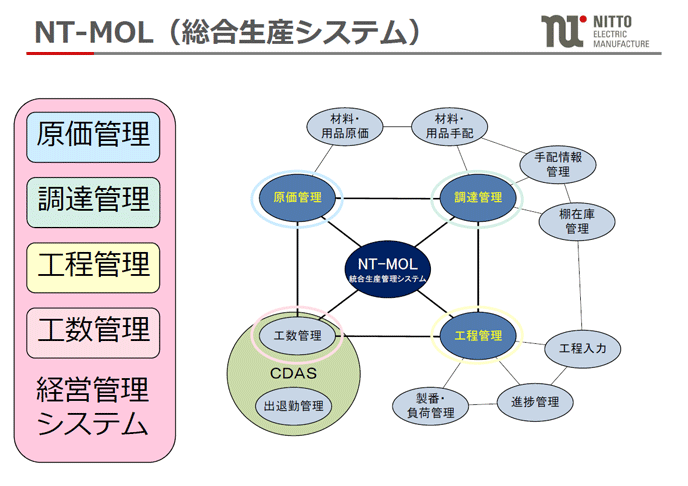
これは、2000年代初頭ぐらいから実際に使っております。今も使っております。リニューアルして、現在のNT-MOLにしたのが2000年です。
原価管理、調達管理、工程管理、工数管理の4つの管理を経営管理システムと呼んでいます。経営に必要な情報がお客さんによってはばらばらになっていて、工程も分かれていたり、原価で異なるデータベースがあったり、当社はこれを全てシームレスでつなげ、しかも誰でもどこでも情報がとれるようなデータベースをつくったわけです。
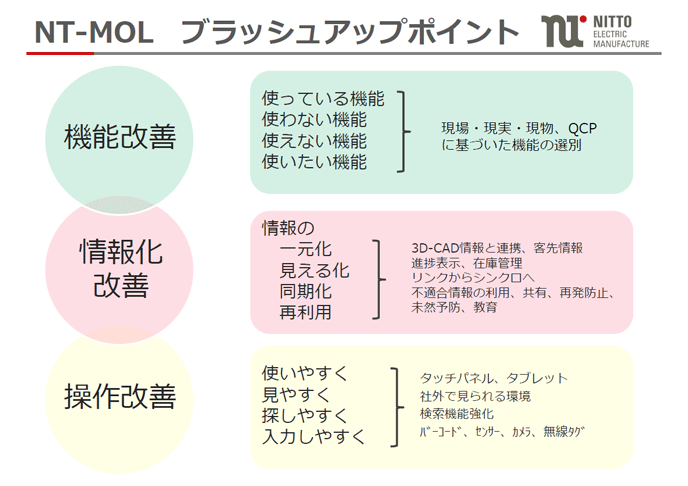
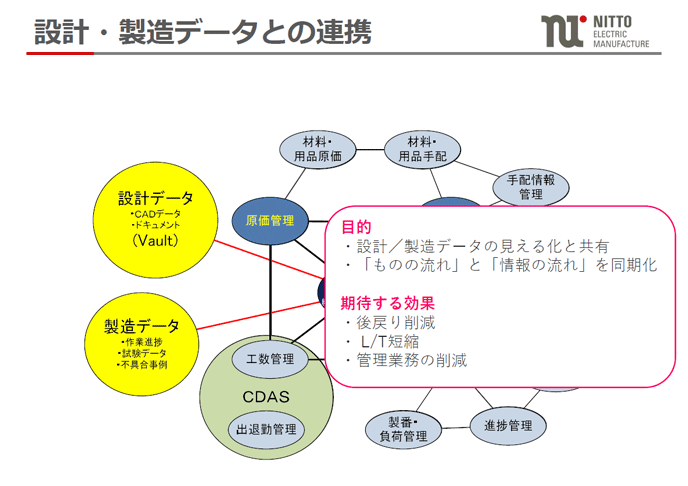
生産管理と聞くと、工程管理やバースケジュール・タイムスケジュールのような機能を思い浮かべがちですが、工程だけでなく、原価や工数とかも全て集約した形で情報が見えるようになっています。
受注情報システムと呼んでいるシステムを説明します。物件を受注後、受注情報台帳に製品番号情報、すなわちジョブに対してオーダー番号を発行するわけですが、その一つ一つに、どういうお客さんで、どういう製品でというのを製番情報として登録をします。そして見積もりから材料費、外注費、購入費を入力します。例えば材料費ですと、鉄板はどれぐらい使うのか、用品購入はどれぐらいあるのか、全て冊子、年度、実績という形で、調達管理ができる「見える化」の形になっています。いただいた金額から材料と外注費を引くと、加工費が出るわけですがそれを付加価値と呼んでおります。付加価値は時間に換算され各部署への指定時間として割り振られる仕組みとなっています。最後に、工程管理として、いつまでに図面を出して、いつまでに組み立てて、いつ出荷、というのが分かるようになっております。
ポイントは、実績です。買った実績、かけた時間の実績、全てリアルタイムで積み増されていきます。実際、このシステムを通して用品購入、外注に発注するのですから、発注した情報がここに集まっていって、今いくら使っていて、今後いくらまでまだ使えるのか、というのがリアルタイムで分かるようになっています。
社員一人一人が一日どんな仕事に時間を費やしたかは、このように分かるようになっています。直課管理システムと呼んでおります。例えば、A君が7時50分に出社をして、タイムカードを切って、仕事を始めます。仕事を始めたとき、ジョブナンバーをINPUTする。どの仕事で、どこの部署で、どんな内容の仕事を何時間やったか、つまり日報を帰社時にオンラインで登録をして帰ります。帰るときはタイムカードをもう一回切って帰るわけです。
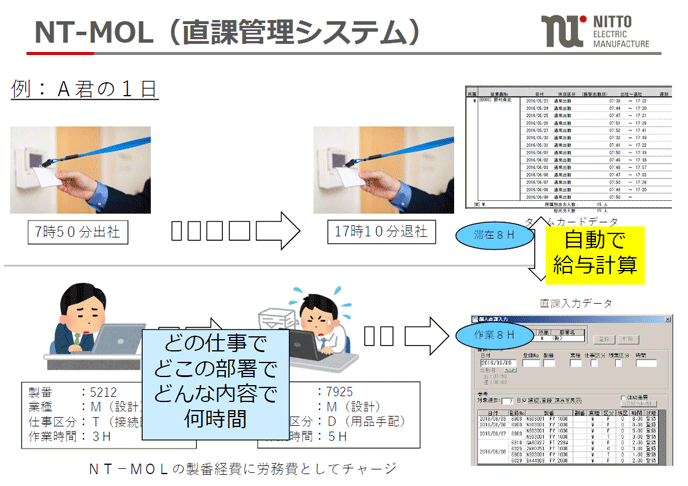
例えば1日の作業が8時間だった場合、帰るときにもタイムカードを切りますので、8時間が合っているかどうか、全て自動で計算をしています。タイムカードのデータと直課入力のデータを毎日毎日自動的に突き合わせ、エラーがあったら、エラーとして上がってくるようになっています。毎日毎日自動的に給与計算をしているような感覚です。総務が3人いますが、うち2人で給与計算をやっています。グループ会社を合わせ300人ぐらいの給与計算をこなしています。
ただ、2000年代からずっと使っているものですから、ここに来て、ちょっとまずいなという点がいろいろ出てきたわけです。例えば、操作性があります。ユーザーインターフェースが非常に古くなっています。あるいはウェブ上で決裁したいという要望が出てきました。機能を拡張したいとか、もう少し「見える化」する場所は結構ある。そうした課題が浮き彫りになってきました。
そういったものをまとめると、大きく分けて3つになります。簡単に言うと、改善点が大きく分けて3つほどありました。
1つ目が機能改善です。使っている機能、使えない機能、使いたい機能をもう少し絞り込んでいこう。2つ目が情報化改善です。一元化されていないとか、見える化されていないとか、もう少し情報をうまく集められないかなど。3つめに、操作性改善です。もう少し見やすくしよう、探しやすく、入力しやすくしよう。例えば、タブレットで使えるようにしたり、営業が社外で工程が見られるようにしよう、など改善点がいくつか出てきました。
この段階で、経済産業研究所のIoT研究会に参加しました。IoT研究会参加後、いろいろ当社は取り組みました。すぐ取り組んだのが、情報の見える化と一元化です。
既存の日東MOLに対して、設計データ、製造データをつなげてしまおうということです。当社はフルオーダーメードでつくっていますので、いかに設計の情報、上流のデータをうまく活用するかによって、コストパフォーマンスが変わってきます。
製造データは、例えば作業の進捗に応じて不適合が出てきます。恥ずかしい話、実際につくっていると、いろいろな問題が出ます。それに対し、どうやって、以後防ぐか、とか、弱みを強みに変えるか、そうしたところを強くしようということで、設計と製造データの見える化、一元化に取り組みました。目的としては、見える化を共有化することによって、リードタイムを短縮したり、あるいは後戻りを削減したり、もっと言うと、管理者の業務を削減してあげるところを目指しました。
具体的に、設計データから説明をさせていただくと、3次元CAD、2D-CADを多用しています。以前は、設計データは部門ごとにサーバーを持ち、技術部ごとのサーバーを立てていました。しかし問題点として、技術部間でデータの相互利用が低い点や、承認行為が人間系でしたので同じ場所に置いてある古いファイルを出図してしまい、間違ったものができたなんていう問題がありました。
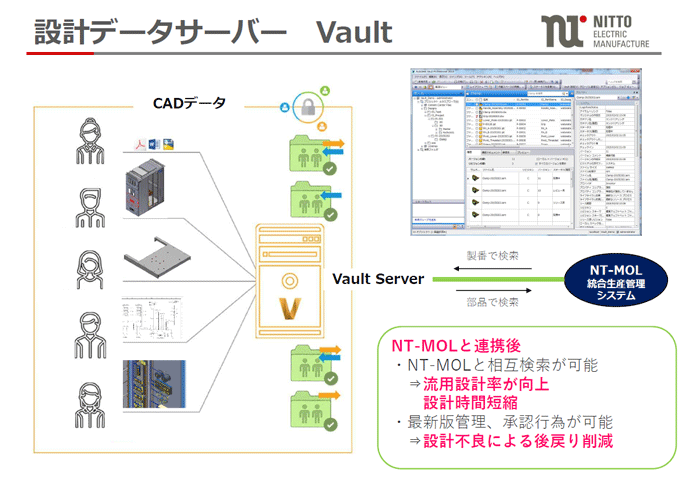
そこで、CADのデータを統合的にCADデータ専用のサーバーで管理するようにシステムを構築しました。例えば検索、最新版の管理などが1カ所で行えるシステムを構築しました。これによって、ローカルで置いていたものを、どの部門でも同じデータを使え、見ることができるようにデータベースをつくり直しました。さらに総合生産管理システム、日東MOLにデータをつなげることによって、双方向で検索ができるようになりました。
それによって流用設計率が向上し、探す時間が短くなりました。結果、最新版の管理をきちんとし、承認行為をできるようフラグを立てさせたので、設計不良による後戻りも減りました。
一方、製造データの管理における課題では、不適合、不具合の再発があります。不良、対策、水平展開、再発防止とPDCAを回すわけですが、非常に時間がかかり、今、誰が動いていて、どういう処置をして、再発防止はどうやって動いているのかというのが見えない。 不具合連絡票があるのですが、紙でしたので終わるとバインダーに綴じられます。見えるようになっていない。そこで不具合管理帳を電子化しました。どこで、どういう仕事で、どういう不具合が起きた、が登録されています。具体的に写真もつけています。添付ファイルもつけられます。それに対してどういう再発防止策を打ったかも入れます。これは全ての部署で見られるようになっています。これらもNT-MOLと連携していますので、類似製番で過去に起きたトラブルも事前に把握することができるようになっています。
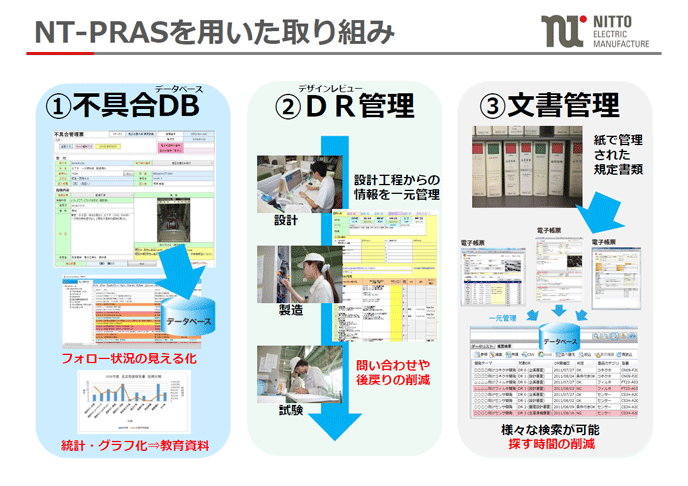
今お客さんに報告中とか、再発防止を検討中だ、というふうに、今どういうステージにいるか、が一元で見えるようになっています。また、決めた日限までにフォローしないと、アラートメールが来ます。
一番よかった点は、自分の部署は、どういう不良が多くて、どういうところが弱いのか、全て情報化され、グラフ化してくれます。これによって、「自分の部署はここにウィークポイントがあったんだ」というのが年間を通してタイムリーに見ることができます。これを教育訓練や教育資料に使っています。
その結果は、一面当たりの構造設計の時間の統計をとると、3年間、2016年から、2017年、 2018年と確実に減ってきました。3年間で21%短縮できました。これは流用率が上がったり、不具合が少なくなった結果、仕事に集中できたり、複合的な要因で時間短縮につながっています。
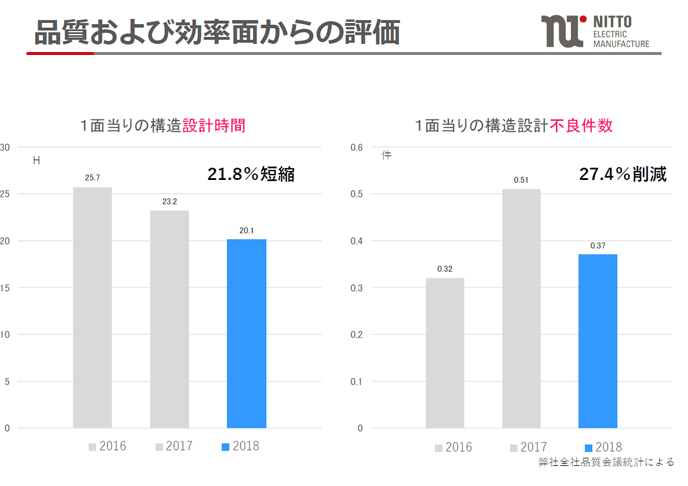
不良件数では、一面当たりの構造設計の不良件数は、2017年から減っていて、対前年比27%削減です。
設計作業の改善でもう1つ、RPAにも取り組んでいます。RPAを用いた設計業務の自動化ということで、どちらかというと定型業務、事務系、総務系の仕事が多いと思います。銀行系や窓口業務など。技術系の仕事には応用が難しいと思われがちですが、当社は直接部門の設計に導入しました。設計は、頭を使うホワイトカラーの仕事と思われがちですが、設計の仕事を分解していくと、頭を使う仕事と手を使う仕事が混在しています。手を使う仕事とは、例えば重複するインプット作業、単に図面を書き写す作業、手を使うだけの仕事も結構あります。直接業務に導入することによって、人間は頭を使う仕事に集中してもらおう、自動的にロボットを使ってできる仕事はRPAにしてもらおう、ということで、労働時間の短縮と本業の質向上を目的としてRPAを導入しました。
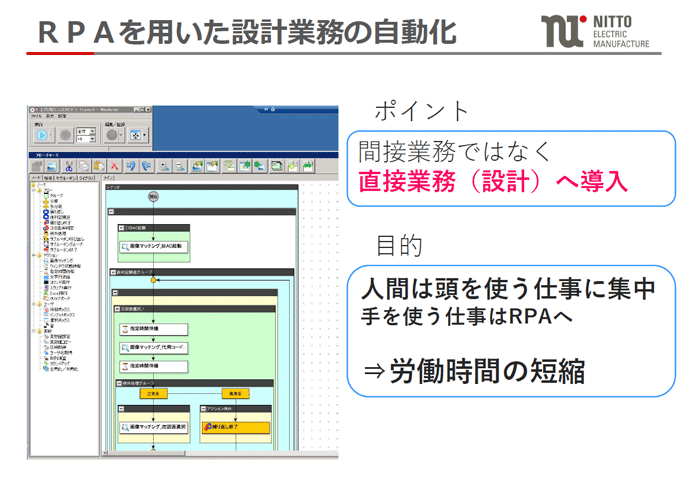
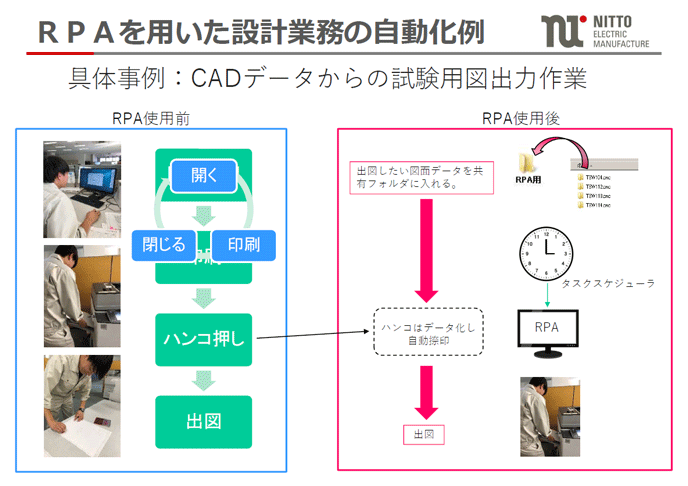
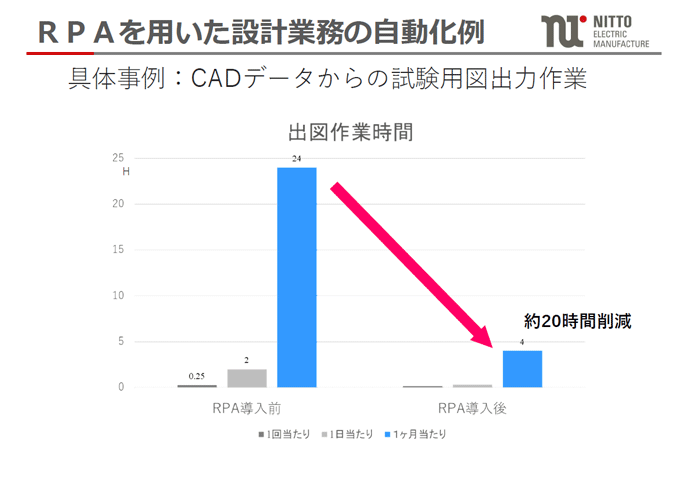
具体事例を説明すると、電気回路CADデータから試験用の図面を出力する作業を自動化しました。RPAを使う前は、「データを開く」→「印刷する」→「ハンコを押す」作業を面数分ずっと繰り返すわけです。20回、30回、同じことを繰り返し、結構な時間がかかっていて、RPAを使うことによって出図したい図面データを、共有フォルダRPA用フォルダの中に保存します。それで終わりです。
タスクスケジューラーで管理されていて15時になると自動的にRPAが起動するシステムになっています。自動的にRPAが動いて、図面を開いて、印刷をします。判子押しも、全て判子もデータ化して、自動的にRPAが決められた場所に押してくれるというシステムも入れました。15時を過ぎるとプリンターのところに出図されているというシナリオになっております。
タスクスケジューラーが肝で、3時までにデータを入れさえすれば、作業をやらなくていいので、3時過ぎたらこれは自分でやらなければならない、ということで時間に追われて動くようになります。1回当たり、20分程度なのですが、1カ月になると結構な時間を出図作業に使っています。それがRPAを入れることによって、約20時間削減ができました。
(2)ワイヤーセンターのロボット化
配電盤の中に大体2,000本ぐらい入っています。配電盤の製造では、3割から7割ぐらいが配線時間です。配線時間がコストに直結します。逆に言うと、配線時間を短くすると利益率がかなり変わってくる。
効率アップするため、当社は2つトライしました。まず、設計データをものづくりに活用するため、3次元CCADを使って電線測長をしています。当社は3次元CADで構造設計し、電気回路も設計しているので、どこからどこに電線をつなぐのかというデータを両方使って、3次元CAD上で電線を測長しました。
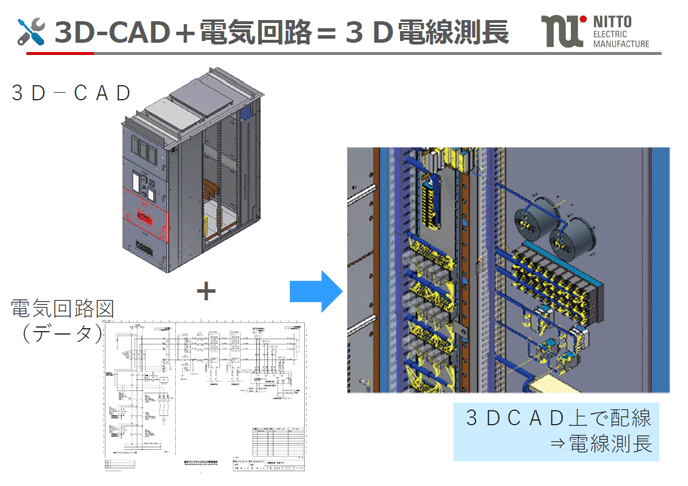
ここからがIoTの活動です。ロボット圧着システムに取り組みました。構想を半年から1年ぐらいかけ、始まったのが2016年の12月からです。全て当社で設計をしました。架台をつくるところから、電装周り、PLCのソフトプログラム、電線をつかむハンドも3Dプリンターで設計しました。IoT研究会に参加されている三菱電機からロボットを購入しました。ビジョンカメラを使って画像を診断させ、電線の先の座標をとって、ロボットで挿入するというものです。
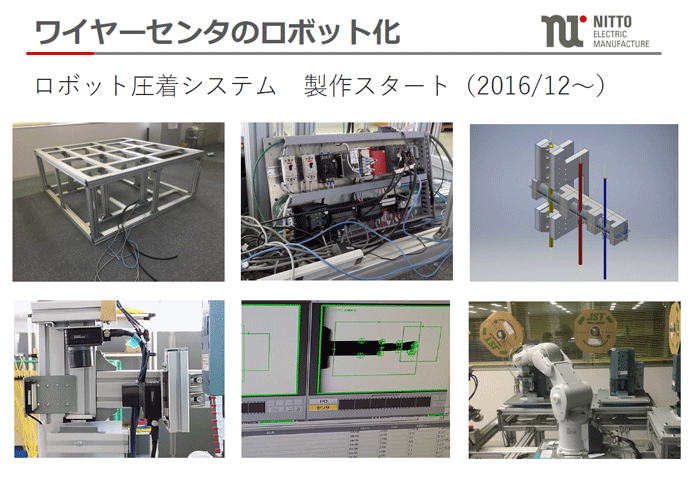
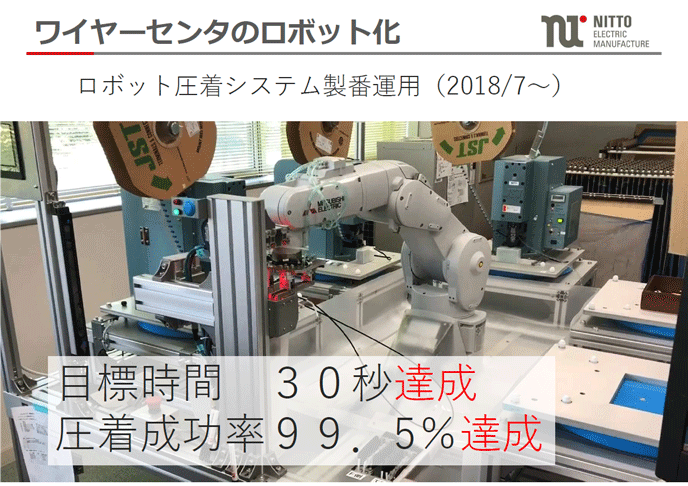
ロボット化による効果として、年間の配電盤の製作年数を2016年、2017年、2018年ととってあります。2018年の初頭からロボットによる自動圧着をトライしました。対前年に対して配電盤の製作年数は13%アップしました。ただし、ワイヤーセンターの人員の数というのは変わっていないので、今の体制のまま13%生産性が上がったと言えると思っています。
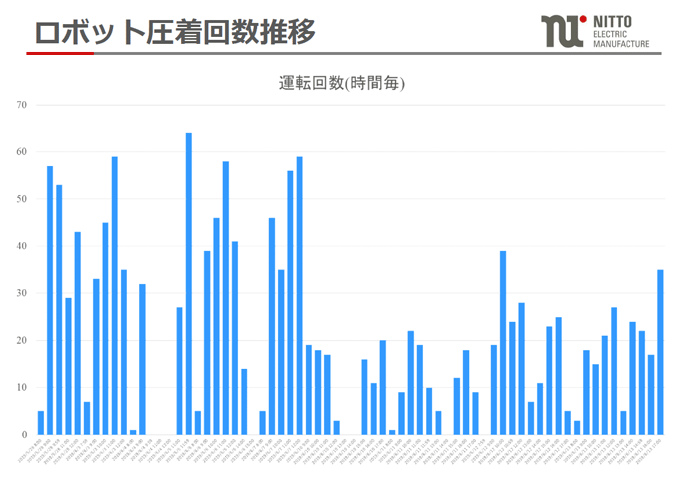
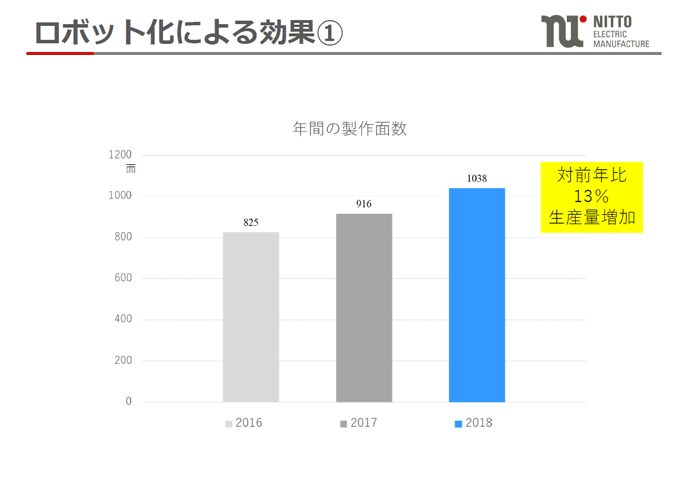
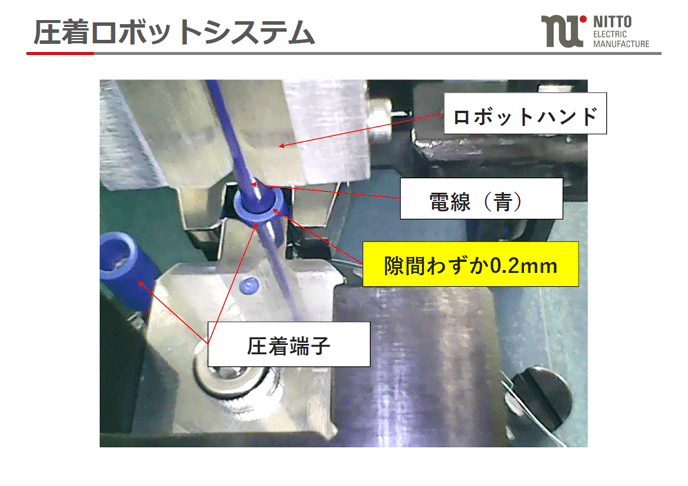
現在は、第2ステージの開発ということでチューブマークの自動挿入が出来るロボットシステムの開発を開始しています。12月の運用開始で開発費は、おおよそ1,000万円の概算です。ロボットを1台から2台追加して3台の共同作業になります。複合作業で実感的には全体の加工時間を半分にしようと計画をしています。
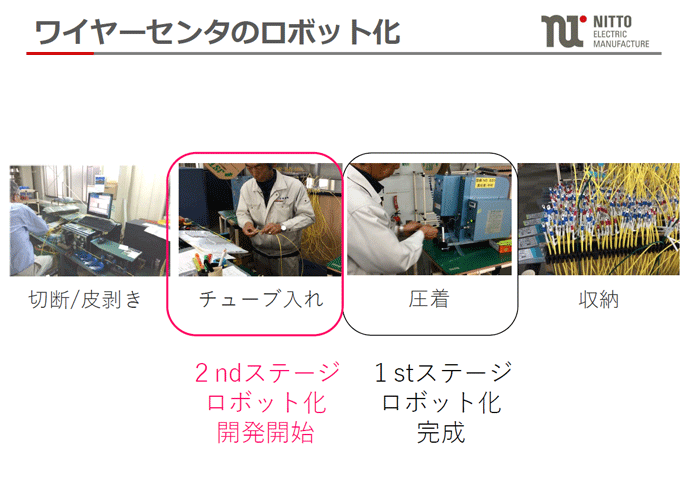
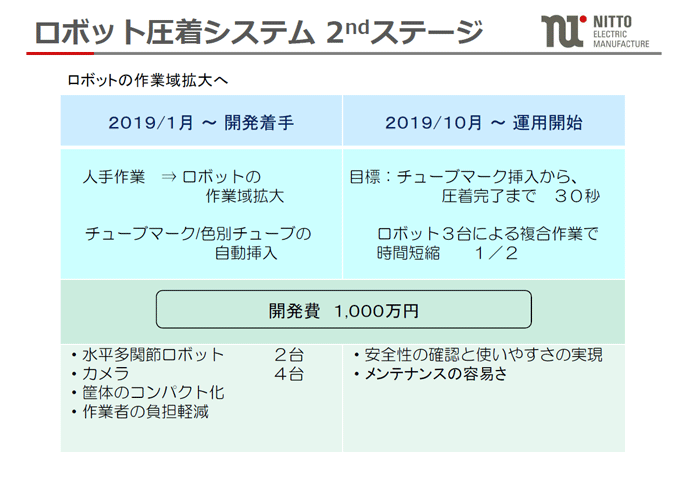
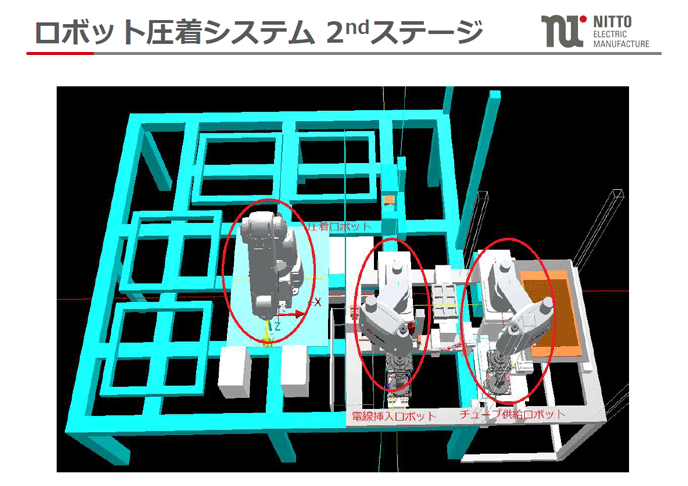