筆者は、2016年4月から経済産業研究所RIETI(2018年4月からは日本生産性本部JPC)において、「IoT, AIによる中堅・中小企業の競争力強化に関する研究会」を主催してきた。
研究会では、これまでモデル企業9社に参加頂き、研究会がモデル企業に対して、アドバイス・コンサルテイングを行う代わりに、「試行錯誤のノウハウ」を公開して頂くことを条件に研究会に参加していただいた。公開するのは、モデル企業による検討のスタートから途中経過の試行錯誤から最後までの企業ノウハウである。それらは、通常「企業ノウハウ」として企業内に留まっているものである。日本国内の中堅・中小企業の競争力強化を図る公益目的の研究会である。
本研究会で採用した手法は、MBAプログラムで用いられている「ケーススタデイの積み上げ方式」である。企業経営を成功させる定石はない。MBAで学ぶのは、多くの成功事例のケーススタデイである。同様に、中小企業へのIoT、AI導入で成功する定石はない。そのため、成功事例のケーススタデイを学ぶしかない。だが日本では、中小企業のIoT、AI導入の成功事例はほとんどなく、しかも、もしあったとしても企業秘密として公開されない。日本に現存しないのであれば、自分で作っていくしかないと考えた。
今回公開する企業ノウハウは、2017年度のモデル企業である「金属技研」の事例である。
Ⅰ. 会社概要
1. 企業情報
1.1 会社概要
(1)社名
金属技研株式会社
(2)設立
1960年(昭和35年)2月10日
(3)資本金
288,000,000円
(4)代表者
代表取締役社長 長谷川 数彦
(5)主な事業
①金属熱処理
②金属およびセラミックスの接合
③HIP処理
④金属・セラミックスの焼結
⑤電子ビーム溶接
⑥超塑性成形
⑦積層造形
⑧表面処理
⑨精密加工
⑩分析・解析・設計
⑪エンジニアリング
⑫航空機部品リペア
(6)事業所
国内:本社、8工場
海外:中国・蘇州工場(現地法人)、上海連絡事務所
(7)従業員数
総計 538名、正社員 426名(2018/5/31現在)
(8)会社の歴史
- 1960年
- 金属技研株式会社創立(東京都板橋区)、熱処理事業を開始
- 1962年
- 群馬工場操業開始(群馬県佐波郡玉村町)
- 1970年
- 群馬工場:真空炉を導入し本格的に防衛(航空)分野の事業開始
- 1972年
- 滋賀工場操業開始(滋賀県草津市)
- 1974年
- 滋賀工場移転(滋賀県愛知郡愛荘町)
- 1977年
- 滋賀工場:ボーイング社品質規格(BAC)の認定取得
- 1982年
- 神奈川工場操業開始(神奈川県海老名市)
- 1984年
- 滋賀工場:HIP装置1号機を導入、HIP事業を開始
- 1987年
- 茨城工場操業開始(茨城県水戸市)
- 1989年
- 姫路工場操業開始(兵庫県姫路市)
- 1991年
- 姫路工場:マシニングセンタを導入、本格的に加工事業を開始
- 1993年
- 群馬工場:国内最大のHIP装置「Mega-HIP」を導入
姫路工場:ホットプレス装置を導入、焼結分野に参入 - 1999年
- 滋賀工場:超塑性成形(SPF)装置を導入、成形分野に参入
- 2001年
- 茨城工場:積層造形成形装置を導入、造形分野に参入
- 2003年
- 有限会社三泉精密から営業譲渡を受け統合
- 2005年
- 長谷川 数彦、代表取締役社長に就任
- 2006年
- テクニカルセンターを設置
滋賀工場:熱処理工程Nadcap認証を取得 - 2010年
- 姫路工場:世界最大HIP装置「Giga-HIP」を導入
エンジニアリング事業本部を創設
中国現地法人・坂上金属技研(蘇州)有限公司を設立 - 2011年
- 千葉工場操業開始(千葉県山武郡横芝光町)
- 2012年
- 成田工場(FAA Repair Station)設立、 Pratt & Whitney社の指定サービスプロバイダー(DSP)として契約を締結
- 2013年
- テクニカルセンター:電子ビーム積層造形装置「Arcam A2X」を導入
レーザビーム積層造形装置「EOSINT M280」を導入 - 2015年
- テクニカルセンター:電子ビーム大型積層造形装置「Arcam Q20」を導入
姫路工場:熱処理工程Nadcap認証を取得 - 2016年
- 神奈川工場: 『JIS Q 9100』に金属積層造形を追加認証
茨城工場:HIP 18号機導入 - 2017年
- 土岐工場 設立
(9)役員構成
代表取締役社長 長谷川 数彦
常務取締役 土屋 将夫
取締役 上田 実
取締役 平山 鉄人
取締役 畑中 秀夫
社訓
「和を貴び、和を守る」
経営方針
・地域・社会と融和をはかり、信頼される会社であり続けます
・つねに変化を先取りし、多くのソリューションを提供します
・たゆまず技術革新に挑戦し、さらにポテンシャルを高めていきます
・人を育成し、活用し、活発な会社風土を築いていきます
・法を守り、公正かつ透明な経営をおこないます
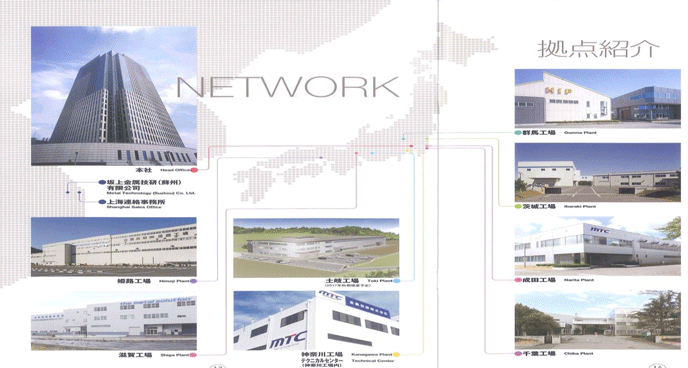
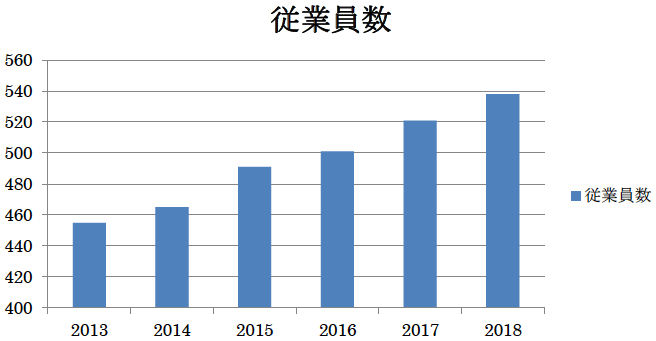
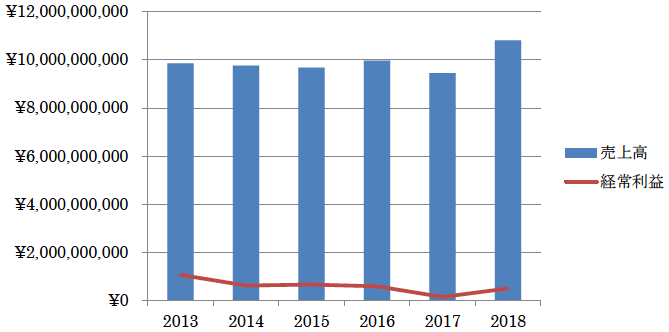
2. 企業の事業内容
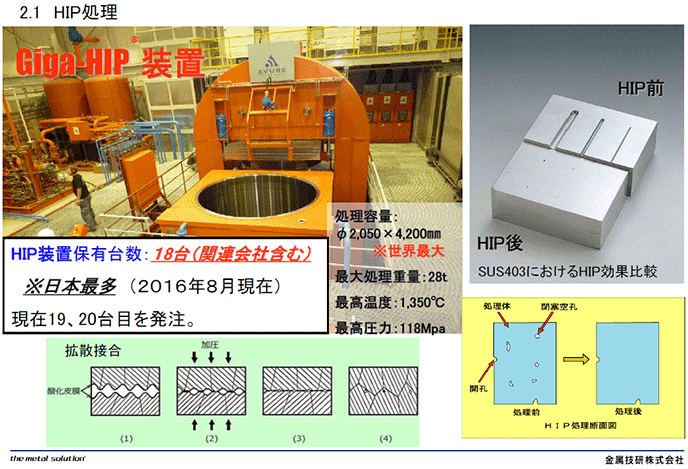
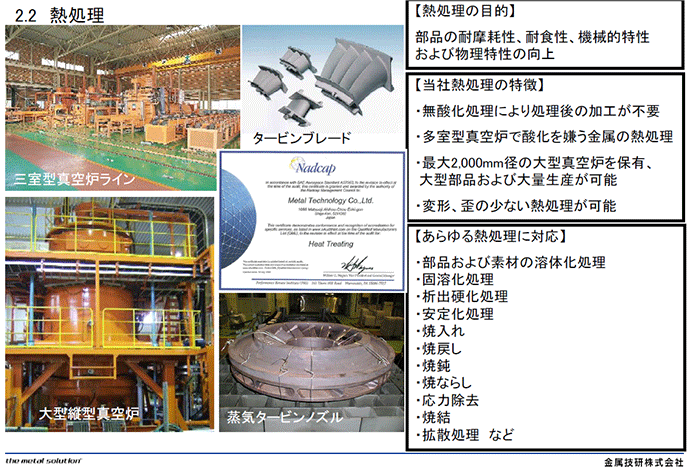
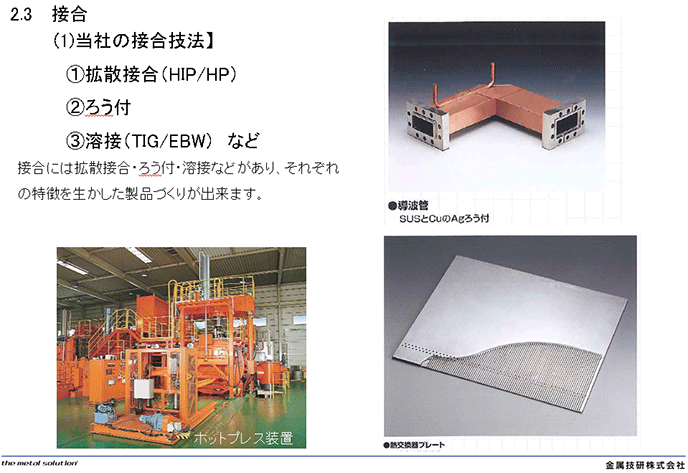
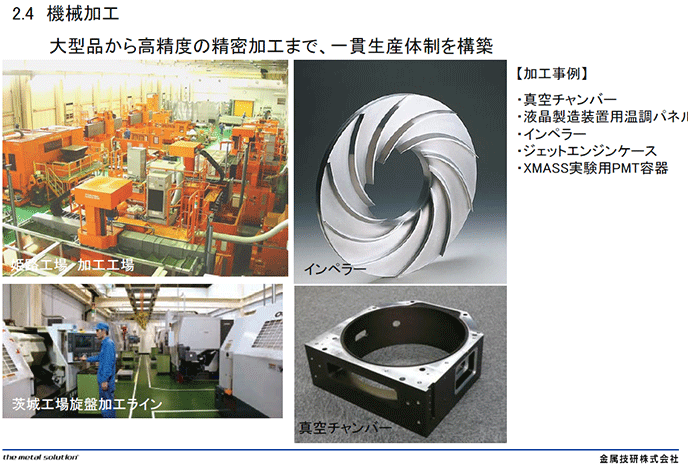
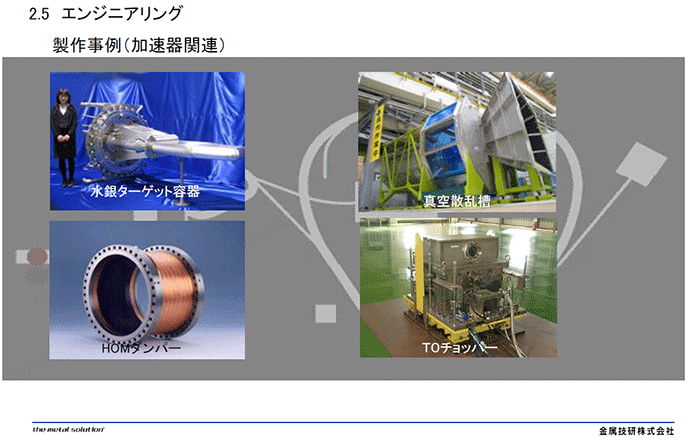
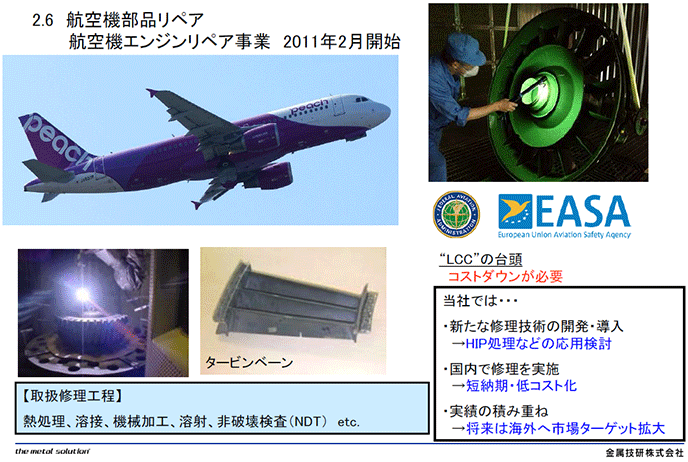
3. 研究会参加の動機
3.1 動機
IoT導入を進めていきたいが、「何を」、「どこから」始めていけばよいのか?
またメリット(費用対効果)があるのか? などの問題があり、進められていない。この研究会をきっかけにして導入を進めていきたい。
3.2 IoT導入に期待するもの
①社内の「見える化」:PDCAによる現場力向上
②ロボット等の導入による省人化・省力化
③設備予兆管理
④生産管理システムなどの導入
上記のものを取り入れて、工場の生産性を向上させる。
3.3 これまでのIT導入の取り組み実績
①各種情報システム(文書管理、工程管理など)を導入し、コンピュータによる一元管理
②新設工場の省人化・省力化・自動化の取り組み(現在、進行中)
a)熱処理製品のAGVによる自動搬送・自動熱処理の実現
b)熱間成形品の入れ替え省人化の実現
Ⅱ. 平山 修一(金属技研情報企画室次長)氏へのインタビュー
研究会に参加した動機
IoTという言葉は知っており、必要性は感じていたのですが、当社は全く導入していませんでした。研究会に参加することはIoTを導入するよいきっかけであり、積極的に取り入れ、生産性の向上が実現できると考えたことが動機です。
IoT導入の検討過程について。研究会に参加する前に、自社としてやろうと考えていたものと、研究会に参加することによって、最終的に導入が決まったものは、同じものか、違うものか
それはほぼ同じです。最初のきっかけとしては、土岐工場という新しく設立した工場があるのですが、そこは土地柄、人口の減少の影響もあり人材募集しても応募がなかなか集まらない。しかも高齢化社会にも直面してきますので、まずは、省人化・自動化、IoTを取り上げようということからスタートしました。
人による効率がよくないから、そこを自動化して、IoTを導入しようというよりは、むしろ、人が集まらないからこそ、そこを機械化して、IoTを導入という考え方がありました。
そこで土岐工場ではAGVによる製品の搬送及びそれを制御するAGV搬送管理システム、熱間成型の金型脱着ロボットを導入しました。 研究会に参加し、いろいろ話を聞いていくうちに当初考えていたIoTよりも、より多様なことが実現できるという認識が持て、幅が広がりました。
具体的には、例えば設備の予兆管理や基幹システムなどがあります。多くのアドバイスをいただいて、気が付いた点が幾つかありました。
それらあらためて気づかされた点が、研究会に参加したことによって付け加わった部分です。それらに対する会社の対応は、前向きで導入したいという話になっています。まだ実現は出来ていませんが予兆管理は特にそうです。弊社は設備産業であり、設備を止めることなく順調に稼動させることが重要で,設備が故障してしまうと仕事が出来ません。その意味で、予兆管理など設備に対する管理をもっとしっかりやっていこうということで、IoT導入を考えています。
ITベンダーの選定
今、土岐工場にはAGVを制御するAGV搬送管理システムを入れていますが、そのITベンダーは、A社にお願いしています。A社は、これまで取引がない企業です。
もともと当社は、パソコンなどITシステム関係のベンダーとのお付き合いはありますが、そのベンダーに今回のIoTの話をしたときに紹介頂いた企業がA社でした。
調べてみたところ、生産管理も含めて、工場のシステムも手がけておられたので当社が検討していることを実現できますか? と確認したところ、できますという回答でしたのでAGV搬送管理システムの開発ベンダーの候補3社の1社にしました。最終的には見積もり仕様書の提案内容及び見積額を比較して当社の要求を一番満たしていたA社を採用しました。選んだ結果は、納期・品質共に満足のいくものでした。
投資対リターン
(平山)もう一つの省人化のためにロボットを導入しました。熱間成形の設備に対して、上の金型をロボットで脱着する作業です。500~600度の状態で加熱炉から出てくる製品・金型を従来は従業員が防火服を着て3人がかりで入れ替え作業していたのですが、ロボットを一部導入することにより、従業員を3人から1人に減らすことを実現しました。このロボットとプログラムや制御も含めて一式で、8,700万円でした。
熱処理製品のAGVによる自動搬送・自動熱処理の費用を含めると1億円を超える金額になります。
(岩本)研究会には地方自治体の方も来られていましたが、一番驚いていたのは投資額です。それぞれの県の地元でも、IoTに数千万投資するというだけでも、皆さんすごく驚いていて、IoTにこんなに投資するような企業は、自分たちの地元にはないとおっしゃっていました。
ところが2017年度のモデル企業は、3社とも何千万とか、1億円なので、県の方々ものすごく驚いていました。何がこんなに違うのでしょうか。IoTへの数百万の投資と数千万の投資、1億円の投資は、何が違うのでしょうか。
(平山)AGVなどの自動搬送にしても、導入している企業は、一番安いところでも2,000万円からとおっしゃっていました。搬送系は、重量物を対象にすればそれだけ値段が上がってきますし、仮置きステーションのような附帯設備も構築すると、金額もそれなりにアップしていきます。金額の差はあってもそれに対する費用対効果を期待するのは同じだと考えます。
当社は、今まで設備への投資はかなりしていたのですが、IT分野にはあまり投資はしてこなかったので、これからはこれらの投資が必要になってくると考えています。
正直なところ、他社の投資額を把握していない部分がありますが、AGV搬送管理システムについては3社に対し、要求仕様書を提出し、それに対する見積もり仕様書および見積書を提出していただいたときに、大体の予算感というのが分かりました。前述しましたが、最終的にはA社を採用しました。
(岩本)それだけ投資するということは、回収できると踏んでいるわけですね。投資対リターンのリターンはどうなりますか。
(平山)熱間成型の金型脱着ロボットについては8,700万円の投資といいました。今まで、きつい・汚い・危険な3Kに加えて熱い仕事を3人で行っていましたが、それを1人へと2人分減らすことができます。最少で考えると1人当たりの年間作業コストが600万円、600万×2=1,200万円が1年間で削減できます。それが2人の場合には、2,400万円の削減です。投資は8,700万円ですが、約4年で回収できます。
何よりも今のままでは人が集まらないということもありますので、ロボットなどの省力化は新しい採用の可能性が拡がるというような費用対効果も期待ができます。
さらにAGVによる設備への製品の自動搬送は、まだコストは出してはいないのですが、そちらも人員削減に役立っています。人が設備まで製品などをホイストやフォークで運び載せていたという作業がなくなります。そういう意味では従業員が4人から2人ぐらいには削減できると想定しています。該当製品を設備に搬送したタイミングで処理条件を設備に自動送信する仕組みも取り入れていますので従業員が設備の操作盤まで行き、制御機器に処理条件を入力する必要が無くなると同時に入力ミスもなくなるので、人員削減効果やミス防止という効果が出てきます。
現在の土岐工場での取り組み状況
土岐工場で取り組んでいることは、AGVを使った搬送管理システムを取り入れております。ただ運ぶだけではなくて、真空炉・大気炉など熱処理を利用する設備に物を運ぶのですが、物を運ぶと同時に熱処理の条件も設備に送り、自動的に処理を行っています。
ハードウェアとしては、横型の3室の真空炉、大気炉2台、大気炉用の受け渡しのステーション、AGV、真空炉用の仮置台が3台、大気炉用の仮置台3台。真空炉と大気炉は、それぞれ大きさが違うので、それぞれ3台ずつ用意しています。
工程管理システムは、熱処理条件を管理しております。設備を動かすような状態にして、物と同時に、熱処理の条件を送ってあげるという形になっています。
製品の流れですが、まず人が作業台に、実際に処理する製品を乗せます。乗せた状態になったら、搬送管理システムから物が乗ったという指令を送ります。すると作業台にAGVがとりにいく。大気炉あるいは真空炉が製品を処理中で置けないというときは、仮置台に一時的に退避します。AGVが搬送管理システムから指示をもらったら、また仮置台にある製品をとりにきて、大気炉あるいは真空炉に物を運ぶ。そのとき熱処理のデータや条件を送って処理する。処理が終わったら、AGVに取りに行きなさいという指令を行って、大気炉あるいは真空炉に取りに行って、作業台に何もなければ、そのままストレートに返す。物があるときは仮置台に一時退避して、AGVに指令を出して、作業台に返却する。
もう一つ別の棟の建屋になりますが、土岐工場は1階が2つのエリアに分かれていて、1つは真空炉・熱処理をするエリア、もう一つは、熱間成形という温めた状態で金型で押し込んで成形するという処理があります。
熱間成形のエリアに関しましては、製品の入れ替えロボットを導入しています。熱間成形はとても熱いので、なるべく人を減らそうと、ロボットを導入しました。土岐工場は、入れかえロボットを導入することによって、3人でやっていた作業が1人で賄うことができるようになりました。
1作業は5分ぐらいかかります。実際、人がやったほうが早い。でも、人を減らせるというメリットは当然ございます。遅くなったといっても、金型は冷え過ぎたりしないくらいの時間で行けますので、運用するには、特に支障がないレベルです。飛行機の部品ですと、自動車と違って、秒では動かないのです。せいぜいつくって月100機ぐらいです。飛行機は、1分1秒を争うわけではなくて、正確さを求めます。3人が24時間やると、3人3班で、9人要るところが3人で済むという意味で、メリットあります。
ロボットは、姿が変わっています。銀色に包まれています。高温なので、ロボットもやけどしてしまうので、やけどしないように、カバーしています。
今、話をしたように、経費削減で大きなメリットが出ています。従来、三人でしていた作業が1人に減ったので、1人当たりの年間作業コストが600万とすると、1,200万の削減が見込まれます。交代勤務を想定した場合、3直ですと、3人×3直=9人でやっているところを6人減らせると、600万×6人=3,600万が削減できます。生産がふえればふえるほど、効果が大きくなります。
今ロボットにやらせようとしている作業は、重いものを持って置くだけでみんな嫌がる3K職種です。みんなやりたがらない、ただでさえ人手不足なのに、人を雇うのだったら、もっと高度な仕事をさせたほうがいろいろな意味でメリットがあります。
ロボットは市販のもので、1,000万ぐらいですが、先に取り付けるハンドが高いです。
大事なのは、先のところをどういうふうにつくり込むか、そこが肝だと思います。それによって大きく変わると思います。まずカメラで、この金型は何か、というのを判断します。製品によって金型が全部違って大きさも違うので、まずカメラで、金型を判断します。置くところも、金型に合わせた動きをするのです。それを判断しています。熱板金が、温まって出てくるので、金型が少しプレスした後、斜めに向いたとなると、その角度を確認し、画素数高目ので、メラメラしてもわかるようになっています。
将来の展望ですが、今後、土岐工場では生産の増加が見込まれています。新しい設備、洗浄装置も入れましたし、真空炉も同じ型を入れることも想定しております。それらを連携させたシステム、また、もう少し搬送する幅も広げていきたいと考えています。
航空機の部品になると、ライセンス、認定が必要になってきますので、その認定を取っているところしか熱処理ができません。今、順番に認定を取っているという強みがあります。
ふえている仕事は飛行機用部品ですし、それ以外、土岐としては医療も増えています。
医療もお客さんの監査を受けて、認定をもらってからでないとできません。発注は、日本の会社からで、実際使われるのは海外です。輸出品です。
飛行機だと、土岐でやっているのは機体でボーイング向けです。実際、製造しているのは日本航空のメーカーです。中部地区は、三菱重工、IHI、日本飛行機です。私どもは直接ボーイングとやりとりできないので、その間に大手が入られて、その下請という形でやっています。ただ、監査はボーイングから直接下請に来ます。
航空機は、一度つくるとそれが10年、20年、30年と、ずっと長いです。将来のことが約束されます。4年間でモデルチェンジないです。ずっと安定して仕事が取れます。将来が見通せるから。航空業界もこれからどんどん伸びていきます。一昔前は大型機だったのが、だんだん中型機に移ってきています。その台数がふえてきています。ただ、小さくなった分、コストが安くなっていくという部分はあります。ふえていても、中型機とかなので、要は車で例えると、ベンツ1台の値段でなく、例えば軽5台のような形になっていくイメージだと思います。
土岐で行っていることは大体以上です。ほかの工場の水平展開の話をさせていただきますと、群馬工場は今、仕事が増えてきてはいるのですが、設備がたくさん置いてあって、これ以上設備を入れられないという状態になっています。遊休している土地に新しく建屋を建てようと進めていて、今年10月ぐらいに建屋が完成して、設備をどんどん入れていくということを今やっている最中です。そこに入れる設備が、土岐工場で使っている真空炉と同じタイプのものを入れます。新工場の投資額は、大体10億ぐらいです。そのぐらい売り上げが伸びているということです。伸びているから、新工場を建てないといけないという。
我々、委託加工業なので、一度手を挙げて受けた仕事は必ずやるという、おりるのは許されないのです。飛行機が飛んでいる期間は保証しろ、という契約なので。設備が老朽化で生産ができませんというようなこと言えません。必ず設備を更新していくということです。
今、基幹システムが全体的に老朽化しているので、全部それを、見直しをしている最中です。基幹システムの中でも今、ここの受注管理システムは8月にリリースします。今、工程管理、進めているところです。工場に引き渡した時点で、その工場の独自のやり方カスタマイズして、統一されたものでなくなってしまった。今回は全社統一したシステム、標準化したシステムをつくろうと考えています。受注管理システムも工程管理システムも全社統一したシステムをつくろうとしております。最終的にはこういう形でやるところが、IoT研究会の目指すところと思います。
理化学研究所から、研究グループから独立したのが我々の始まりです。売上高は111億です。工場群としては、土岐、千葉と成田、群馬、茨城、神奈川、滋賀、姫路、これとは別に、中国に有限公司があります。本社が東京にあります。航空事業が土岐、千葉、成田ですが、千葉・成田は、メンテナンス・リペア・オーバーホールをするところです。土岐は心臓と言われる部分を担当しております。
当社は、理研のグループから独立して企業をつくった会社です。当時、金属熱処理というのは当然、大気だったのですけど、それを雰囲気中、もしくは真空中でやるというのは、当時はなかったんです。当時、事業化するというのはあまりなかったようです。還元処理を考えて、メインでそれをやるというのはなかなかなかったようです。大気炉にかわって、真空であったり、特定のガスの雰囲気であったり、そういう炉というのが独自の技術ということ。
今の会社の技術的な優位性は、HIPです。HIP処理を高温高圧でやるというのが当社の主力です。HIP処理した後に熱処理をするという一連の工程を全部自社でやるというのもありますし、その中心となるのはHIP業務です。
航空が14%ぐらい、半導体とエネルギーが30%ずつです。半導体ですと、半導体の基板に表面をコーディングをするスパッタの材料を使うスパッタ装置です。エネルギーは、原子力、火力発電のガスタービン羽根の部分です。
最終的なゴールの姿と今回導入したIoTとの関係
将来のIoTのゴールは、各工場の自動化です。今回導入するIoTは土岐工場で、まず試験的に導入しました。設備のレイアウトも含めてゼロからのスタートでしたので一番導入しやすかったのです。既存工場では設備が稼働しているのでかなり制限がされるため自動化の導入が困難ですが、何もないところからやると、最初から自動化を想定した工場を構築できるので、まずは土岐工場から手掛けることになりました。そこで構築したノウハウをほかの工場に水平展開していくことを考えています。
既存工場の建物や設備が老朽化しており再開発を余儀なくされるところです。再開発に当たっては、スクラップアンドビルドを行い、老朽化した建物を取り壊して新しい建物を建設し、新しい設備を据え付けます。そこに土岐工場と同様にAGVおよびそれを制御するAGV搬送管理システムの導入をしていきます。それによってAGVによる設備への製品の自動搬送と処理条件の自動送信を実現していきます。既存設備を移設する場合はAGV搬送管理システムと通信が可能か確認し、出来ない場合はシーケンサーなどを交換し通信可能にして、AGVによる設備への製品の自動搬送と処理条件の自動送信を実現していきます。
また土岐工場では実現した設備は真空炉や大気炉ですが、他の工場では、HIPなど目的が異なる設備があるので、それらにも同様の事が実現できるように展開していく予定です。
設備投資額は、今の土岐工場で1億円ぐらいの実績からすると、他の工場全体で7~8億円ぐらいかかる大きな投資と考えています。
最終的にはIoTを駆使した全社で統一したシステム構築・FA化を目指したいと考えています。工場によって特色があるので全く同様のシステム・FA化は困難ですが、ある程度の統一化は可能だと考えています。またAIも取り込んでの予兆管理や「見える化」を実現してより効率化を図りたいと考えています。
IoTを導入した効果として金額以外に何かあれば
顧客に対するアピールが出来ると思います。顧客の多くは自動化を実施或いは構築中で当社も期待されています。よって、土岐工場での自動化の取り組みを見学された顧客は非常に興味を持たれ、費用対効果や処理能力などを質問されます。期待されていることを感じます。従来の顧客からはオーダーの増加やアイテムの増加が見込まれます。新規顧客についても同様のアピールをしたいと考えています。
また日刊工業新聞に土岐工場がIoT導入事例として掲載されました。全国版であり、この掲載されたことによる顧客拡大も期待しています。
研究会に参加された感想
(平山)IoTを利用して色々なことを実現したいと考えていました。それを実際にされているモデル企業がいらっしゃいましたので、非常に参考になりました、例えば、東京電機殿がタブレットを導入されていましたが、当社も導入したいことの1つであり、実際現場での運用について拝見できたのでとてもイメージが湧きました。
他のモデル企業で実現されていることを当社に置き換えて、何をどうすれば実現できるかという発想が浮かび、非常によかったと思います。
(岩本)同じことは2016年度のモデル企業の方々もおっしゃっていて、自分の会社が発表するだけじゃなくて、ほかの会社が発表する内容は、普通、会社の中だけで議論するような内容なので、それが研究会で聞けるというのは非常に参考になるとおっしゃっていました。
そのため自社がモデル企業として終わった後も1年間、オブザーバーとして参加されていました。他社の取り組みは参考になるのですね。
(平山)なります。業種は違ってはいても、IoTでやっていることが非常に参考になりました。研究会で、予兆管理も実現できますと、参加者の方に指摘していただきました。
他社の取り組みが非常に参考になりました。
IoT導入を考えている他社へのアドバイス。日本の中堅・中小企業は、IoTを導入しているところは、まだほとんどないが、やらなければならないと考えている社長は結構多い。そういう方々に対するアドバイス
まずは、何をやりたいか。当社は自動化が出発点だったので、省人化、省力化、自動化といった順序で進めていきました。まずはモデル工場を選んで、小さいエリアで対象となる作業や製品を限定して省人化、省力化、自動化などIoTの導入を手掛けていき、その後、水平展開してエリアが拡充していくのが望ましいと考えています。
IoTによるデータの収集自体は簡単だと思いますが、収集したデータをどのように活用するかが非常に重要で、そのようなことをよく考えて取り組んだ方がよいと思います。
そうでないとただ単にデータ収集しただけで終わってしまいます。そこのところを意識して進めるのがいいのではないかと思いました。
IoTを使って、会社として将来的に何を目指しているのか。IoTを使うことによる将来的な会社の最終的なターゲットや会社の方針。
今当社が直面しているのが、工場の自動化です。
しかし、その前提条件として5Sがあると思います。普段から心がけてはいますが自動化のための5Sを徹底することも開始しました。社内で「工場のFA化と業務改善プロジェクト」を立ち上げ、各工場から自動化や業務改善に興味ある人材と、工場の中でも水平展開できるような役職の人、さらに若い将来を背負うような人材を募集して活動しています。エリアを限定しての5S活動、そのエリアに所属する社員の品質教育、さらには自動化したい作業の提案などを実施していきます。そのような基盤を作り、それと並行して自動化を実現していきます。前述しましたが、最終的にはIoTを駆使した全社で統一したシステム構築・FA化を目指したいと考えています。
導入に当たって苦しかったことがあれば。
(平山) 社長からのトップダウンでしたが周囲の理解を得るのは大変でした。中には批判的な方もいて、自動化に投資するなら生産設備に投資すべきだとの意見もありました。最終的には理解していただきました。
(岩本)社長は、中身はあまりわからないけども、直感的にこれからこういうことをやっていかなければならないと思っていたのですか、それとも技術的な中身までわかった上で、やれ、という感じだったのでしょうか。
(平山)理解しています。以前、姫路工場の工場長を務めていて建物のレイアウト、設備配置、設備の製品を載せる台のレベル統一、シーケンサーに通信機能を搭載するなど当時から自動化を想定した工場設計をしていました。
何か困ったことがありましたか。
AGVについてはAGVメーカー、設備メーカー(2社)、AGV搬送管理システムを構築するメーカーの4社との仕様検討が必要でした。個別での仕様検討・確定から相互間(GVと各設備、GVとAGV搬送管理システム、各設備とGV搬送管理システム)の仕様検討・確定とやるべきことが多くあり、確定した仕様も個別での検証、総合的な検証まで実施したのでそれらに対する取りまとめが結構大変でした。
最後に、全体を通じた感想。
IoT研究会に参加させていただいたことによって、IoTに対する考え方が広がったのはとてもよかったです。多くの助言も頂いたことによって、多くの知見が得られました。第3者の方からの助言なので当社の人間が思いつかないような発想もありました。当社がこれから力を入れて取り組んでいく分野ですが、やるべきことが多くあるので社内で同じ意識を持って進めていきたいと思います。
全体の最終ターゲットからすると、今はまだ初期段階ですが、1つ事例ができると、社内から困っている作業などについて自動化出来ないかと相談されるようになってきました。
良い傾向に向かっていると感じています。
同じ業界で比較したとき、当社のIoTはこれからだと思います。以前、他社のAGVによる自動搬送を見学させていただいたのですが、処理工程の順に設備が設置されており、向きも統一、設備の高さも統一されていました。作業者は入口付近の準備スペースに製品を設置或いは回収スペースにある製品を回収するのみであとはAGVによる搬送と設備の自動運転が実現できていました。とても感銘を受けました。 当社は、そういうよいところを見習い、よりいいものを目指していきたいと考えています。