筆者は、2016年4月から経済産業研究所(RIETI)(2018年4月からは日本生産性本部JPC)において、「IoT、AIによる中堅・中小企業の競争力強化に関する研究会」を主催してきた。
研究会では、これまでモデル企業9社に参加頂き、研究会がモデル企業に対して、アドバイス・コンサルテイングを行う代わりに、「試行錯誤のノウハウ」を公開していただくことを条件に研究会に参加していただいた。公開するのは、モデル企業による検討のスタートから途中経過の試行錯誤から最後までの企業ノウハウである。それらは、通常「企業ノウハウ」として企業内に留まっているものである。日本国内の中堅・中小企業の競争力強化を図る公益目的の研究会である。
本研究会で採用した手法は、MBAプログラムで用いられている「ケーススタデイの積み上げ方式」である。企業経営を成功させる定石はない。MBAで学ぶのは、多くの成功事例のケーススタデイである。同様に、中小企業へのIoT、AI導入で成功する定石はない。そのため、成功事例のケーススタデイを学ぶしかない。だが日本では、中小企業のIoT、AI導入の成功事例はほとんどなく、しかも、もしあったとしても企業秘密として公開されない。日本に現存しないのであれば、自分で作っていくしかないと考えた。
今回公開する企業ノウハウは、2016年度のモデル企業である「日東電機」の事例である。
Ⅰ. 会社概要
1 会社の概要
日東電機製作所(以下、日東電機)は電力会社向け制御機器の設計から製造まで提供する電力の安定供給を支える電力制御機器の総合メーカーである。群馬県太田市に本社を置き、関連2社と日東電機グループを形成している。
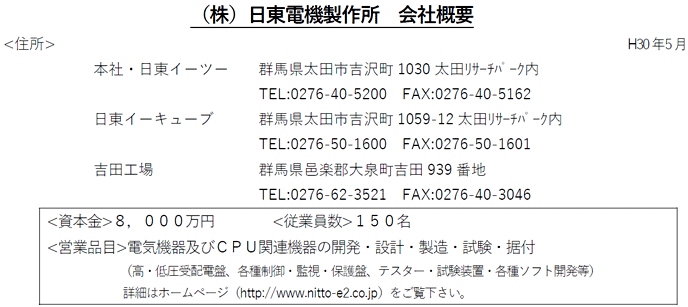
同社は、1951年に市販通信機器部品を製造する有限会社として設立された。その後、1956年に磁器増幅器・変圧器の受注生産を、また現在主力製品となる配電盤の製造は1967年に開始した。(株)東芝や東京電力(株)など大手企業との取引を行い、「価値ある製品を作り出すシステム・アーキテクチャー」を経営方針に、日本の電力産業を下支えしている。
他社よりも早い時期から 製造工程に図面レス配線方式を導入、設計を機械化するため、エンジニアリングワークステションを活用するなど自社へ最新の技術を取り入れてきた。特に2000年代に入ると、CADシステムの本格的な活用を開始した。3次元CADデータを利用することで、板金穴あけ加工及び板金曲げ加工自動化が既に稼働する段階に至っている。
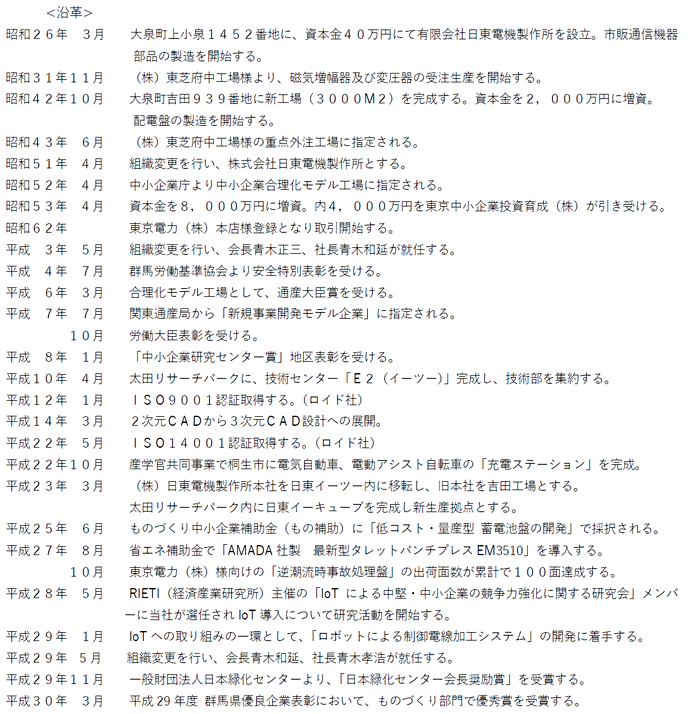
日東電機の強みは一貫生産体制にある。全ての製品に対し、立案設計から生産設計、板金、製造、試験まで一貫生産しているので、コスト競争や短納期対応では他社にない優位性をもっている。こうした一貫した生産管理システムを、われわれは「NT-MOLシステム」と呼んでいる。NT-MOLシステムは1980年代から使用しており、経営・設計・現場の3つを結ぶデータプロファイリングとして日東電機の発展を支えてきたのである。
以上のような特徴をもつ日東電機は、企業の収益性および安全性など経営成績が総合的に良好である開発型企業と判定され、群馬県中小企業モデル工場に認定されている。配電盤で使用される機器は用途によって多種多様であり、その分、部品も多岐にわたるから、受注生産に対して効率的な供給ができるよう、自社の生産ラインを上手く管理することで、業績拡大に結びつけていきたいという。
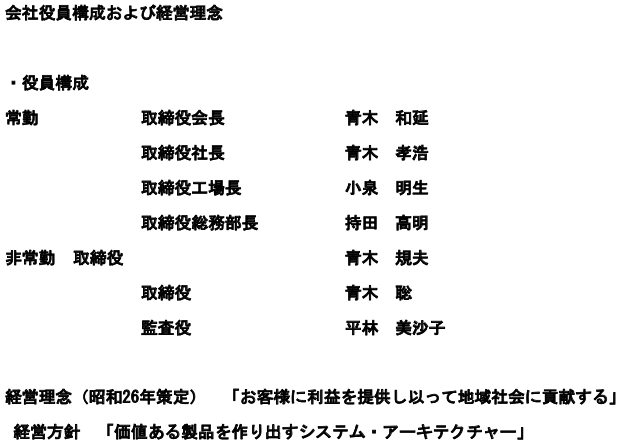
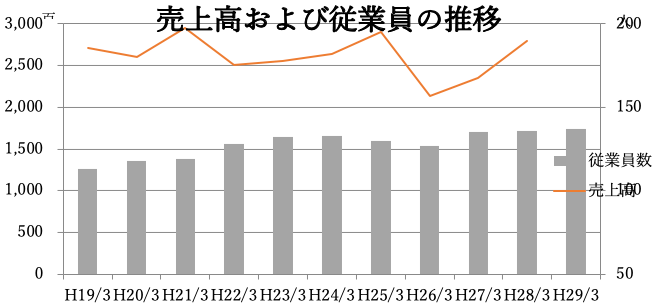
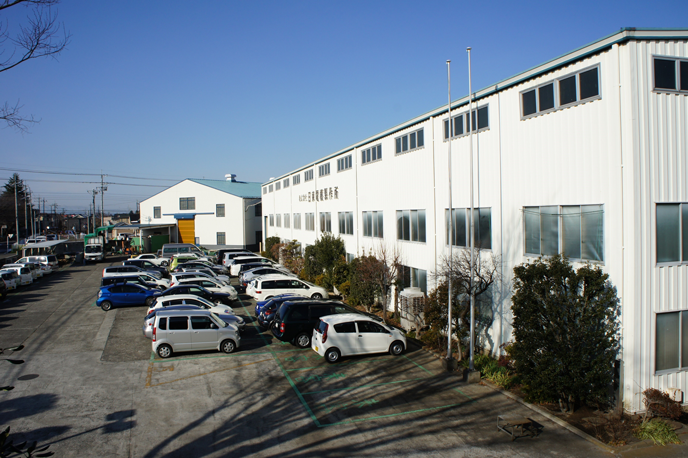
2 解決すべき課題:「カイゼン」による生産性アップ
日東電機がIoT研究会に参加したのは、最新技術であるIoTを自社に導入することで、(1) 製造工程の手作業体制、(2) やや古くなった「NT-MOLシステム」を「カイゼン」するためであった。制御盤製造工程のうち、ワイヤー加工作業は手作業であり、しかも製造時間の6割以上を占めるため、ロボットによる自動化で、作業効率の向上を図りたいと考えた。一方、「NT-MOLシステム」については、導入したのが1980年代であり、年々システムを修正・拡張してきたが、IoT技術を付加することでさらにブラッシュアップしようと考えた。
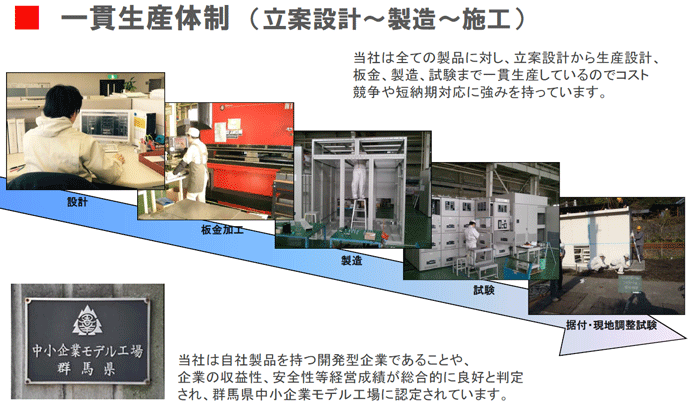
3 IoTを用いた解決方法:「ワイヤー・センターのロボット化とシステムのIoT化」
そこで同社が実施したのが、ワイヤー・センターのロボット化と業務改善診断であった。当初は製造工程全体にIoTを導入しようと考えていたが、大手企業でも一部手作業で取り組んでいるという、IoT研究会の指摘もあり、部分ごと自動化を優先することに決定した。
生産管理システムに関しては、古い非効率箇所を特定するため、業務改善診断を行い、新たに「設計データ」「製造データ」のシステムを追加することで、データファイリングを徹底し、情報検索の簡易化を目指した。
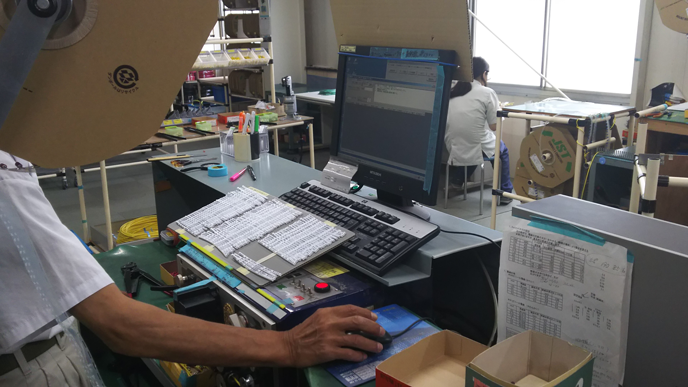
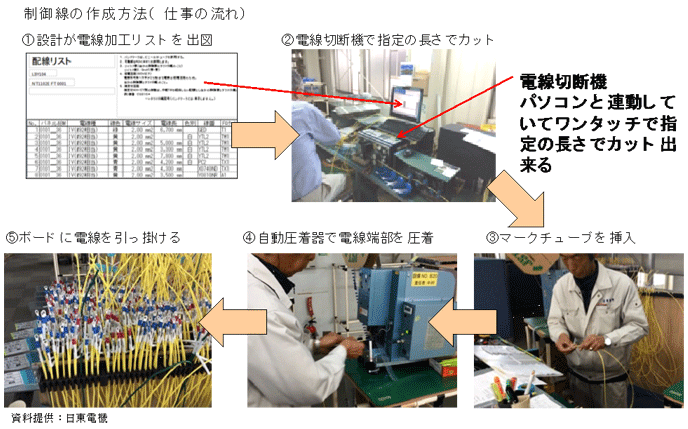
ワイヤー・センターについては、ロボットが得意な作業はロボットに任せ、人間に任せるべき作業は依然として人間が担うことで、ロボット作業が、手作業業務と並行することで、実用化に近づいている。現在は人員の増減までには至っていないが、自動化が定着していく過程で検討していきたい。投資費用は1,700万円ほどだが、リードタイムの短縮・作業能率の向上・生産量拡大による「カイゼン」効果は、500万円/年ほどを見込んでいる。「NT-MOLシステム」については、情報の共有化が進むことで、「重複業務」「後戻り」などがなくなり、生産性向上に大きく貢献してくれると予想している。診断結果から、付帯作業の2割を改善できるとの試算であったので、システムのIoT化が完成すれば、1,800万円ほどのリターンにつながるとのことである。
今回の製造工程自動化では、社外のベンダー企業等と提携することなく、社内の設計・開発部門(2名)で実現することができた。IoTという新たな技術を、既存のスキルと上手く接合していくことが効率的な経営に結びついたといえる。
4 「試行錯誤こそが“ノウハウ”」
日東電機は、「一体何をどうすればIoT化といえるのだろうか」と常に悩み、「研究会でひとつひとつの課題を検討し、その成果を報告する過程で、成功と失敗を繰り返した」という。しかし、重要なのは単なる成功ではなく、その“過程”にあった。ちまたで提供されるIoT化の事例は成功事例でしかない。技術者としては、その過程で得られる経験やノウハウこそが貴重な財産なのである。「導入までの試行錯誤こそがノウハウだ」という同社社長の言葉には、技術者として今回のIoT導入によって得られた成果が十分に大きかったことをうかがわせている。
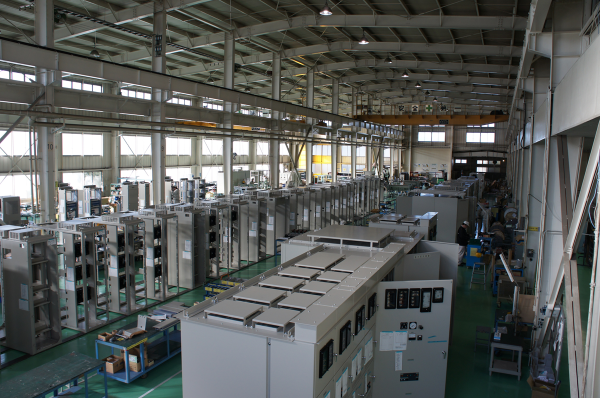
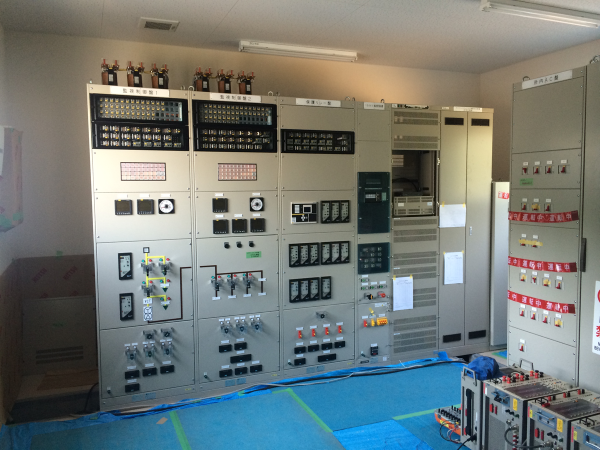
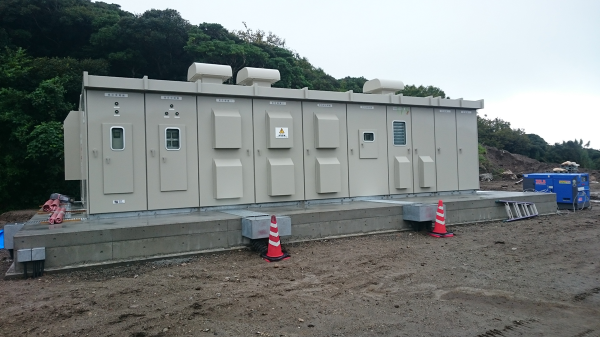
5 進捗状況と次の目標
日東電機が現在取り組んでいるのは、作業工程で得られる情報を電子化し、再利用する「見える化」とワイヤー・センターの実用化である。特にワイヤー・センターは、開発・実用の段階から運用・改善の段階に移行している。具体的には、開発時よりもロボットの動きを単純化し、またカメラ・センサーを取付け、作業効率を大幅に改善した。試作時には安全面・効率面にあった問題点を克服できたことで、作業の自動化実現に大きく近づいたのである。同社の次の目標は、制御盤製造の完全な自動化と生産管理システムの段階的な拡張である。人とモノとをつなぐIoTを、自身のノウハウと体験を基に活用する日東電機の今後の発展は、追随する企業の有意義なモデル・ケースとなることだろう。
Ⅱ. 青木会長へのインタビュー
1 これまでの進捗状況
スケジュール的には2018年1月から運用に入っていなければならないのですが、まだ留まっている状況です。
配電盤工場の2階でワイヤー・センターの手作業を行っていましたが、ロボットの横で手作業とロボット作業の両方やらせるという状況になっています。困っていることは、1つは、一連の作業で測長をし、電線のストリップをし、ロボットがつかんで、両端の圧着をして、最後に離すまでの時間が、30~40秒近くかかっています。これだと人間のほうが早い、というので、それを30秒以内に短縮するという作業をやっていました。実現できたのは25秒です。
もう1つは、品質の成功率を上げなければいけないので、目標としては99.5%を掲げてきました。2スケアはそこに入ったのですが、1.25というミミズのような、さわると曲がってしまう径が細い電線が曲がってしまいます。
そこを改善するために時間を要しました。
今、品質の成功率を上げる上で問題なのは、電線の皮むきをしたとき、表面や断面が荒れている部分が、測長ミスを発生させることです。
測長ミスというのは、カメラで状態のチェックを全部加え、その誤差をロボットに指示し、端子の真ん中に通すとときに、削り取ってしまいます。断面が荒れていることが問題だということが分かりました。
これまで、人間がその荒れているものを通すとき、すばらしいことに人間は、触覚で全然苦にしないで、すとーんと通します。端子の内径と電線の外径がコンマ1しかクリアランスがないですが、そこをシュッと入れられるのです。
ロボットだと、補正をしているのですが、コンマ1ミリを補正しきらないと、圧着不良に認定されてしまいます。不良率が10%もあれば仕事になりません。
人間は100%でしたが、一応、ロボットで99.5%ぐらいまでいきました。2スケアと1.25の電線がクリアできました。
コンマ5という、その下にもっと細い電線があって、これは始末に負えないからやめようとなりました。1.25までやると大体7割から8割はロボットでできます。
コンマ5はそんなにはありません。8割方が1.25スケアと2スケアの2種類の太さの電線です。イメージ的に言うと、1つの配電盤の中に500本ぐらい入っているとすると、そのうちの8割の400本ぐらいはロボットでできます。残り100本ぐらいは多芯ケーブルであったり、圧着端子でなくコネクタピンだったり、それらは手動でやらざるを得ないのです。
当社は忙しかったです。ここに携わっている社員、仕事が分かっているエース級の人間がそこに携わっているのですが、忙しくなると、オンジョブで引っ張り出され、戻ってこない。ある物件が終わるまでは離れられない。そうすると、1カ月、2カ月平気で止まってしまいます。中小企業は、どこもその問題を抱えながら進めていかなければならない気がします。
実際にロボットを使い始めると、全ての作業の大体8割ぐらいがロボットでできるようになります。ただ、1台では足らないので、もう1ライン作らないといけません。ロボットのラインを。今、手作業のラインが2つあります。
2 投資対リターン
これまで人間がやっていたうちの一部をロボットにやらせるようになると、変わってくることは次の2つです。
1つは、生産を拡大させるという意味で、人間ですと1日の処理量が400本ですが、ロボットを入れることによって、800本に上げられます。1ラインで、人間がやっていたうちの8割をロボットが肩がわりするだけではなく、プラスアルファで8割分をロボットが別に作るわけです。生産量が増えると同時にリードタイムが短縮します。全体のリードタイムがここの部分で、全体の製造現場の3割ぐらいとっているのが減ってきます。
けれどリードタイムよりはむしろ生産量が増えるほうが効果は大きいです。物づくりの中の30%がワイヤー・センターの仕事で、それが1.5倍になるので、3割分が1.5倍になるから4.5になります。実態的には4.0です。そうすると全体は、100が110になる。だから、売り上げは少なくとも10%は増えるわけです。会社の売り上げは30億弱、それの10%増、3億売り上げが増えるのです。
ロボットを導入したことによって、配電盤の製造能力は10%増えるわけです。フルに受注すれば、売り上げも10%増えます。
投資は、ロボットが800万ぐらい。周辺機器も含めて 全体で1,600万ぐらいの投資。それにもう少し付け加えて2,000万ぐらいです。単純に考えると、2,000万投資して3億の売り上げ増です。3年間で大体取り返せるという試算です。
生産能力が10%増強は大きいです、2,000万の投資で。やはりここがボトルネックだったのです。社員の皆さんもうれしいです、残業しなくてもいいので。ここが清々と仕事ができるようになりました。そういうのは、金額でなかなか反映できない効果です。喜んでいます、皆さん。ここがぐっと短縮されたのであれば、うれしいです。しかも売り上げは増え、ボーナスが増えたら、みんな喜びます。残業は減るし、ボーナスが増えるとなったら、皆さん全員がハッピーです。
これから先は、生産管理システムは結構進捗が出てきます。
3 研究会に参加した現時点の感想
機械の稼働率を見ようとして、センサーをつけて、機械の稼働状況など情報はどんどん集まります。ですが、集めた情報を確認していかないと何の対策も立たないという問題があります。今機械が止まっているけどどうしているのですか、と追跡して言わない限り、集めたデータが何の役にも立たない。
中小企業は人がいないので、「今、何やっていたの?」「どうして機械が止まっていたの?」「いや、ちょっと材料を入れ替えていました」というやりとりになると、どうにもならない話になってしまいます。
データは、機械が10台あれば、10台につなげたら、機械の稼動状況をデータでとって、それを改善しようとしたときに、そういう手がほんとうに打てるんだろうかという心配があります。
機械が動いてないことを見えるようにするのだけど、なぜ止まっていたのか、そこを改善しなければ、見える化してもしょうがない。 そのときトイレ行っていたのか、材料の供給が止まっていたのか、あるいは作業者が打ち合わせで呼ばれたのか、それを明らかにしないと、手は打てない。
一生懸命、機械のデータとっても、それをどう手をつけたらいいか、考える人がいない、中小企業には。
AIは、教えないとだめでしょう、過去の膨大な事例やこうなったらこうだよっていう状況を教えないといけない。
その過去の事例は、ドキュメントではない。頭の中にあるだけ。頭の中にはドキュメントとしてはあるのだけど、それが形になってあらわれてこないというのが痛いところだと思います。
人間ができる範囲には限度があると思います。どんなに熟練作業員でも人間だから、その日の体調とか気分によっても変わってくるし、100%ではない。だから、最後に判断するのは人間なのですが、それに対して、過去の例から判断すると、これが原因だろうとか、こういう対策を打つのがいいだろうとか、アドバイスをしていくというのが、これからの時代のような気がします。