筆者は、2016年4月から経済産業研究所(RIETI)(2018年4月からは日本生産性本部JPC)において、「IoT、AIによる中堅・中小企業の競争力強化研究会」を主催してきた。
研究会では、これまでモデル企業9社に参加頂き、研究会がモデル企業に対して、アドバイス・コンサルテイングを行う代わりに、「試行錯誤のノウハウ」を公開することを条件に研究会に参加していただいた。公開するのは、モデル企業による検討のスタートから途中経過の試行錯誤から最後までの企業ノウハウである。それらは、通常「企業ノウハウ」として企業内に留まっているものである。日本国内の中堅・中小企業の競争力強化を図る公益目的の研究会である。
本研究会で採用した手法は、MBAプログラムで用いられている「ケーススタデイの積み上げ方式」である。企業経営を成功させる定石はない。MBAで学ぶのは、多くの成功事例のケーススタデイである。同様に、中小企業へのIoT、AI導入で成功する定石はない。そのため、成功事例のケーススタデイを学ぶしかない。だが日本では、中小企業のIoT、AI導入の成功事例はほとんどなく、しかも、もしあったとしても企業秘密として公開されない。日本に現存しないのであれば、自分で作っていくしかないと考えた。
今回公開する企業ノウハウは、2016年度のモデル企業である「正田製作所」の事例である。
Ⅰ. 会社概要
正田製作所はステアリング部品やT/M部品・シートベルト部品といった自動車部品を扱う製造メーカーである。主力製品であるステアリングコラム部品の生産実績は月産100万本に上る。群馬県桐生市に本社工場を、太田市に尾島工場を置いている。海外拠点としては、中国四川省成都市に成都正田車用部品有限公司をもち、グローバルに部品供給を行っている。
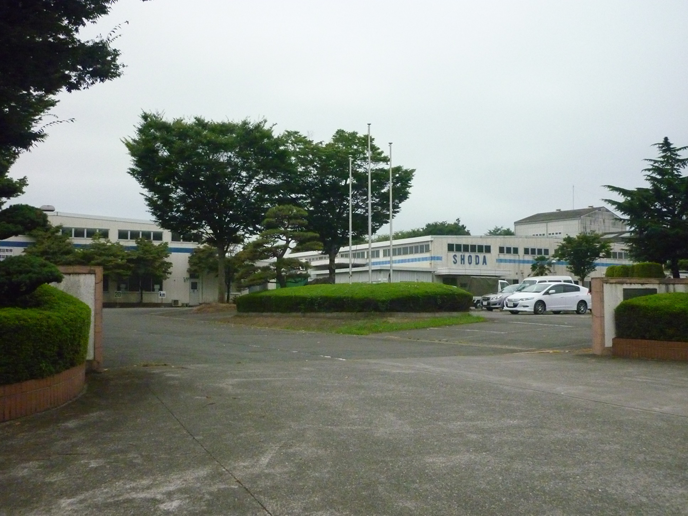
同社は、1952年に創立以降、古河機械金属・SUBARU・日本精工など多くの企業から受注を受け、部品供給を行っている。当初は削岩機部品やスクーター部品などの受注を受けていたが、徐々に自動車関連部品の供給が中心となっていった。それ以降、同社では、生産方式や開発・特許の面でのレベルアップを目指し、技術面・開発面に力を注いできた。特に自社の設備についてみれば、設備自前比率は65%、購入比率は35%と積極的な自前技術への取組みを行っている。こうした技術は同社の「物づくり」を支える原動力となっている。例えば、1982年に有名なTPS(Toyota Production system)を、他社に先駆けて製造ラインに導入した。2002年には、そのTPSを参考に、自社向けに考案した「SPS」(Shoda Production system)という、新たな生産方式を整備した。独自の思想など組込んだこの生産方式では極めて廉価な投資額で生産を可能にし、その中には4億円から1.3億円へと3分の1程度の規模で実現する事例もあったという。またシートベルト部品の特許出願(1982年)やISO9001(1998年)・ISO14001(2004年)の認証取得などにも取り組んできた。この他にも、アルミニウムの鋳造・機械加工・小組機を連結させることで「1個流し化」を成功させ、『群馬技術大賞』を受賞している。
このように同社では、「狭い分野でも世界一をめざす誇り高き技術屋集団」をコンセプトに、日本の「物づくり」産業の核となるよう、自社の発展に日々努めている。
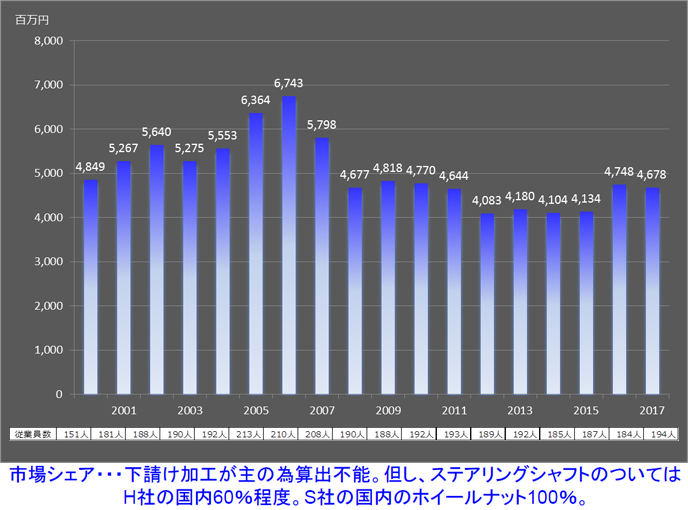
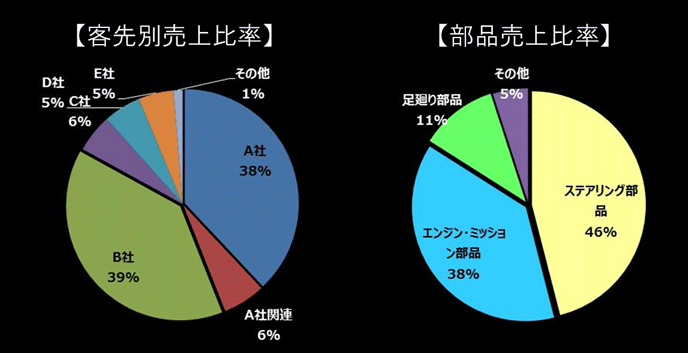
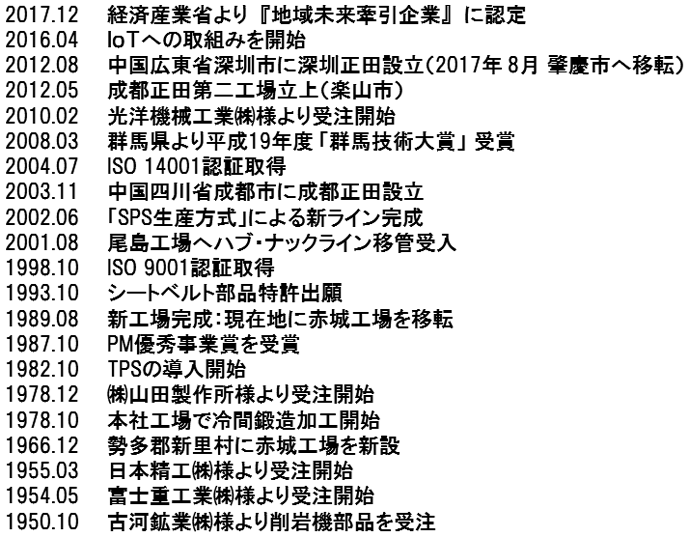
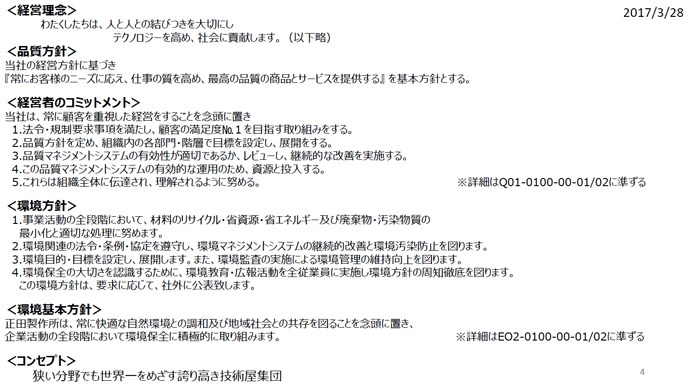
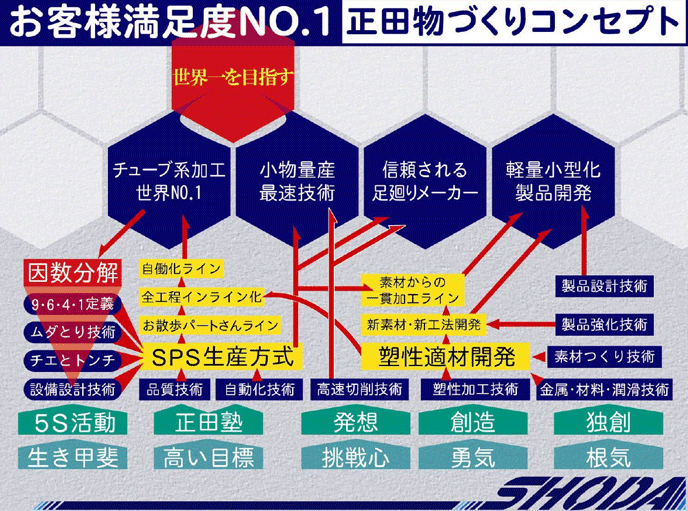
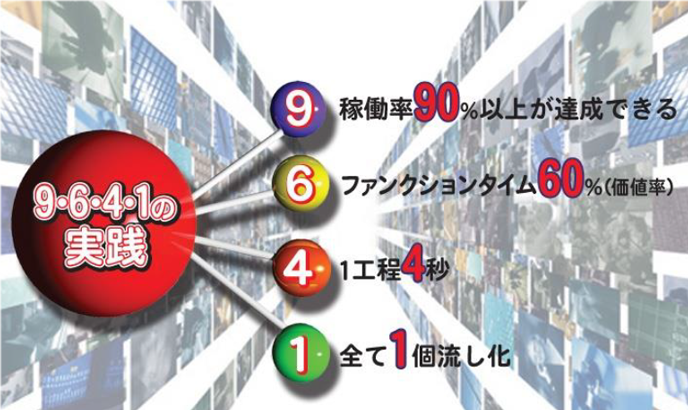
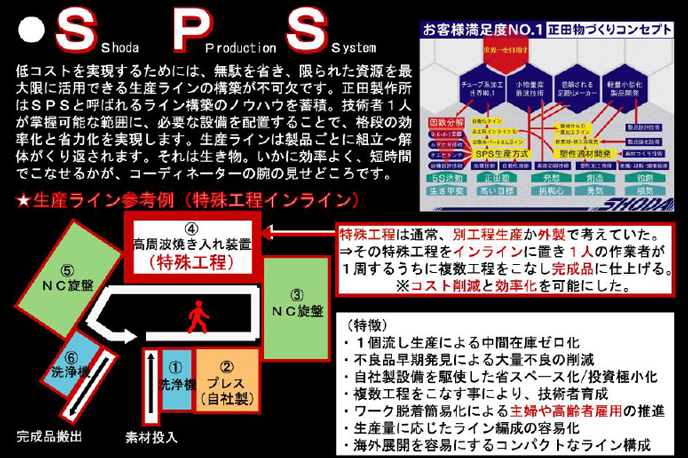
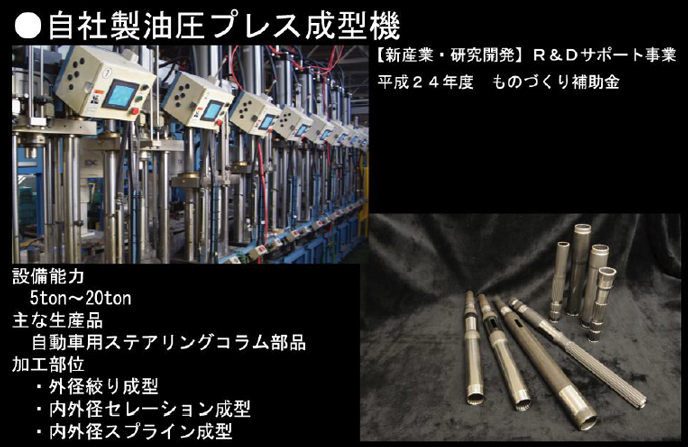
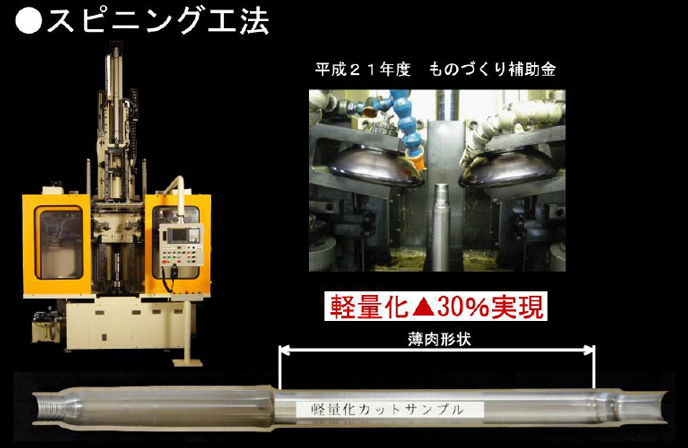
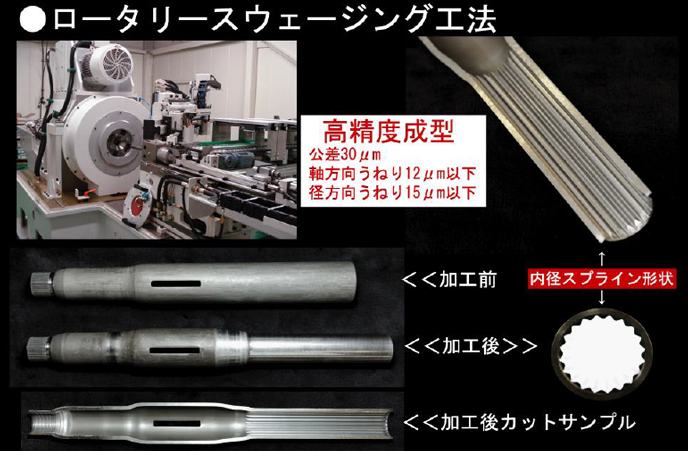
Ⅱ. 正田会長へのインタビュー
研究会に参加した動機と同社が抱える課題
正田製作所が抱えていた課題は、IT・ICTの導入に出遅れてしまっていたことだ。IoTは新聞でときどき見る程度でしかなかった。不況の折、大手親会社からの受注も減っていたこともあり、納入先の新規開拓のためにも、なにか策を練る必要があった。IoT研究会に参加したのは、“IoT”というツールを「モノづくり」と結びづけることで、付加価値を高めるためである。ようやく2016年3月からIoTの選任を当てることができたため参加を決めた。
同社は、自動車メーカーの下請けの加工業でありいわゆる大量生産の会社である。トヨタ生産方式を参考にSPSという生産方式を作り出したが、それはアナログ的なものであった。
SPSは人の手作業の限界を見極めて、1サイクル何秒で作れるかと、より安価な設備でラインを作るもの。17~18年前から、パートが散歩しながら仕事ができるようなラインを構想していた。人間が1つの工程に携わる時間を4秒、それを8工程32秒でぐるっと回る。ワークの入れ替え2.5秒、歩行で1.5秒、合計4秒である。実際69歳の人が、若い人と同じ1サイクル22~23秒で回っていたラインもある。
このラインの構想と実績をもとに「女性・高齢者に優しい生産ライン」を目指したいと考えたが、そこには様々な課題がある。
当初は、いつ・誰でも・不良無く生産できるために、工程ごとにモニターで作業指示をしたり、設備点検データをセンシングして通信で飛ばしたりなどのラインの改造を考えたが、試算でも3,000万円であり、採算がとれない。また、高齢者の8時間稼働は難しいので、2~3時間単位で空いた時間に予約出勤できるような仕組みとそれに対応できる優しいラインが必要になってくる。
IoTを用いた課題解決:「製造ラインにおける検査の自動化による円滑な労働環境の創出」
正田製作所が試みようとしている新たな構想とは、女性や高齢者でも短時間で気兼ねなく働けるような生産ラインを構築するというものである。これまでは、一見して若手従業員と同じ作業スピードを維持するため、早く出社して準備を始めるなど高齢従業員には隠れた負担がある状況であった。そこで、「製造作業者に負担の少ない職場の構築」をするため、製品の品質チェックを、最終的に検査機で自動管理化し、異常発生時には通知が送信されるようにしたらどうかと考えている。検査工程にIoTの技術を導入することで、労働者の負担を軽減しながら製品の品質確保を図ろうと考えたのである。
IoT導入にあたり、技術部門の人材を展示会やモデル工場見学への派遣を通じて育成を行った。自社内でのIoT導入を行うため、推進担当が設置されたのである。また、具体的に当社がこれまでに導入したIT投資の内容としては次の通りだ。まず、通信インフラとして現在までに、社内LANと一部の端末にはWi-Fiを整備し、工場間の連携を図るためVPNを導入した。加工現場には、自動計測・自動寸法補正機能を取付けたラインもある。円滑な情報共有を目指すため、PHS・タブレットを一部の社員に支給した。また、検討中の最終検査機は、200〜300万円ほどで実現したいと考えている。そして、得られるリターンの試算は次の様に考えている。検査工程を自動管理化することと、作業工程に特別なスキルが不要となれば、これまで正社員を配置していた製造ラインをパート的労働者に代替可能となる。ラインによっても異なるが例えば正社員20人の年間労働賃金を、半分以下に圧縮できるとした場合、その削減効果はなんと4,000~5,000万円ほどになるとのことだ。現在のところ、こうしたリターンを見込んでいることから、IoT・自動化推進担当者の増員を予定している。専門スキルをもった人材を育成していくことで、今後の収益増に期待しているのである。
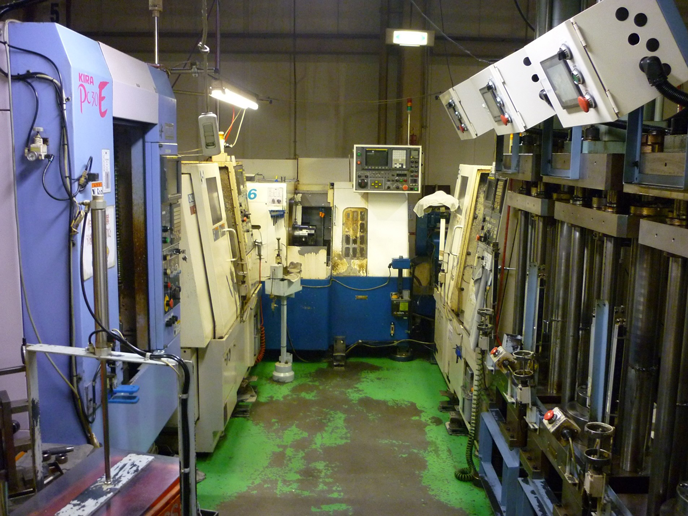
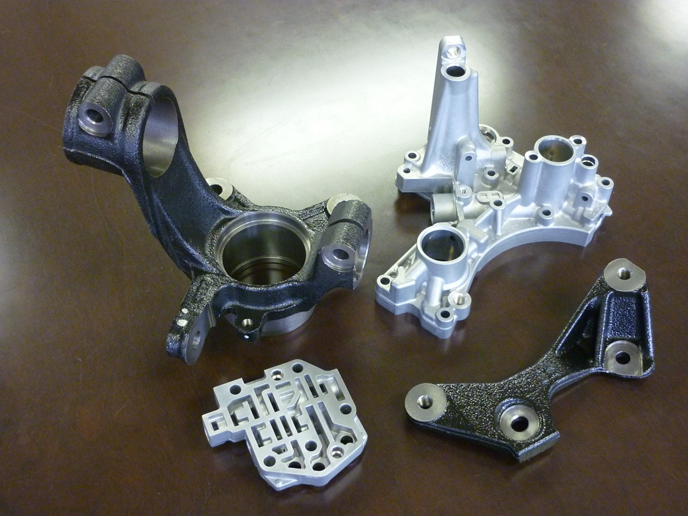
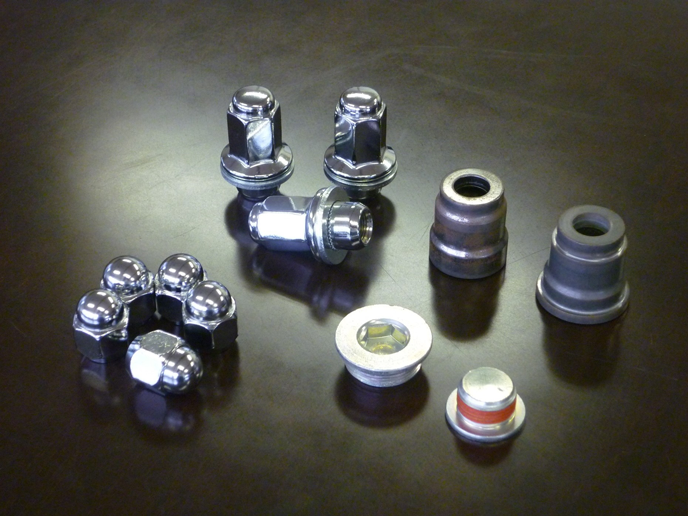
IoTといえども所詮はツールの一つ
正田製作所はこうして生産ラインのIoT化に大きく舵を切った。特に重要であったのは、「少しずつできるところから切り崩して、挑戦すること」である。前述したいつ・誰でも・不良無く生産できるラインにするために、当初3,000万円ほどの投資費用が算定されたが、検査工程の自動化は安く自社開発することで対応していく。なんでも大手企業と同じ設備を導入する必要はない、IoTへの過信・依存は本末転倒でしかない、肝要なのは“IoTはツールに過ぎない”と理解し、自社に合ったものだけ取り入れる姿勢である、というのが同社の考え方である。
進捗状況と次の目標
正田製作所が最近導入を開始したのは、データを収集するためのシステムと現場のネットワークの構築である。現時点では、データの収集方法を確立し、どのデータを採取することが重要なのかを検討している段階だが、少しずつシステム開発に取り組んでいる。実際、i Smart Technologies株式会社が提供する「製造ライン遠隔モニタリングサービス」を社内設備にとりつけて、製造ラインのモニタリングを試験的に開始した。「いつ、どの設備がどれだけ生産したか」といった情報が「見える化」したのであった。このデータを次期に導入する現場専用のサーバと無線でネットワーク連携することで、現場のデータを有効活用していくことが狙いである。
正田製作所は、こうした取り組みのほかに、3DデータとCAMシステムの接続、加工工程の自動化を行い、納期を大幅に圧縮する「超短納期」を実現していきたいという構想も練っている。このように付加価値を高めることで、遠隔の企業にも販路を拡大し、ゆくゆくは米国などの大手自動車会社などからの受注に対応するのが同社の夢である。
IoT導入による実施内容
実際のIoTの現場での進捗状況についていえば、まず大きく変わったところは組織です。担当部署が研究開発部門として独立しました。部長が兼務、1人研究員を追加して2人半です。去年は1人でしたので、新しい方向に向けて手を打つ部署を強化しました。
IoTの進捗状況としてモニタリングシステムのお話をします。弊社が導入したモニタリングシステムは旭鉄工株式会社(i Smart Technologies社)が昭和の機械でもIoTができるという売り込みで出しているものをテスト的に導入しました。昨年はとにかくやってみようと始め、どのようなデータが出て、そのデータはどのように使えるのか、を試しました。今年は、実際のラインに入れて、実際のラインの改善に使ってみるという方向で動いています。
実は、このモニタリングシステムを現場に入れる前に、7年ぶりに軽自動車の富士1,000キロレースでIoTを実感することができました。社員で10人ぐらいのチームつくって出たかったのですが人が集まらない。若者が車に興味がなくなっているのです。実際レースで一番大変なのは、ストップウォッチでラップタイムを測り、記録することと、ドライバーにサインを連絡することでした。人が集まらない中でも新しく入ってきた人のなかに、ITに詳しい人がいて、スマホのGPSを使ったデータロガーの情報を得て試してみました。スマホのアプリです。すると、チームの車が、今、第1コーナーに入るところだとか、時速90キロで走っている、などが全部わかります。ラップタイム計測もしなくていい。GPSがあるので、位置情報でゴールラインを決めると、そこを通過したときにタイムを計測するのです。ドライバーにメッセージも送れるので2人分ぐらいの省人化ができました。
これ、すごいことだよなと感動しました。それで、そのシステムをそのまま現場に入れようと考えました。原理は同じなんですよ、全く。レースの発想で、これと同じものを工場につくればいいじゃないかと。
もともと旭鉄工のシステムは、知っていました。でも、レース中に、スマホに全部表示し、指示も全部スマホを使っていると、製造現場で情報収集と指示を出すことも、同じようにできるのではないかと気づきました。それを発想の原点にしました。
今、実行しているのは、生産ラインのタイムスタンプという、1個のモノができるのに何秒要したかを計測するものです。たとえば生産工程の最後に製品を取り出す扉が開いた時間と回数を計測する仕組みです。何かトラブルがあり、次の製品が出てくるまでに時間を要すると、そのタイムスタンプの間隔が伸び、停止時間がわかります。
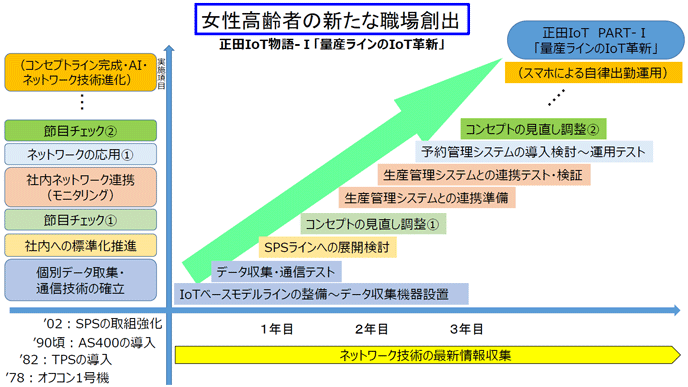
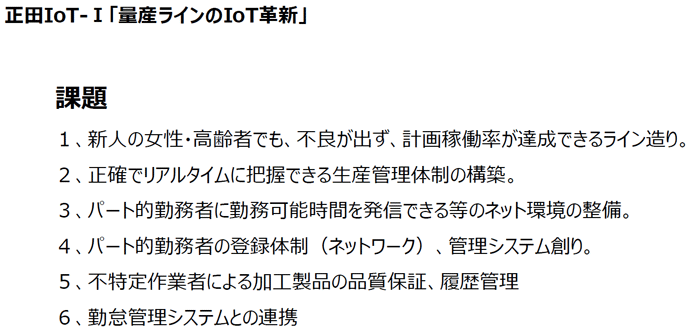
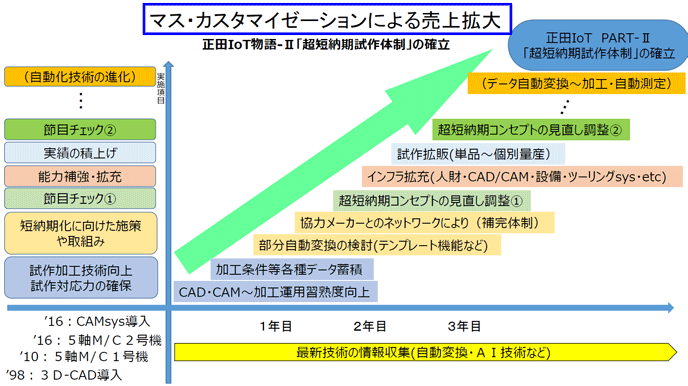
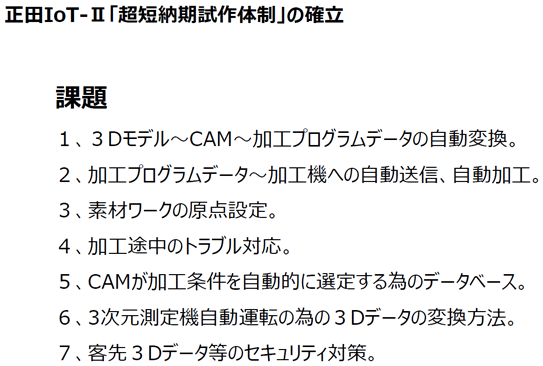
投資対リターン
投資としては、旭鉄工のモニタリングシステムで10万円弱から始められました。機器構成は受信機と送信機があり送信機は台数分費用が掛かりますが、かなり安く設定されています。受信機1台につき、最大30台ぐらいまでの接続実績があるそうです。それ以外に、月額料金が必要です。送信機のデータを受信機がクラウドに上げるという仕組みで、そのデータを編集した専用のサイトを見るイメージです。
実際にそのデータが見られるのは、インターネットがつながる環境ですのでIDとパスワードを入力できれば、どこでも、誰でも、今でも、スマホでも見られます。それは見える化、すなわち、ビジュアライゼーションです。
まだ2ラインにのみ導入したところなのですが、これから、何ラインも広げていこうと思います。これで製造課長の仕事が変わってきます。基準となるサイクルタイムを決めるのも、今まではラインサイドでストップウォッチを持ち、何周か回ってもらい、その時間を割って、大体決めるような状況でした。また、以前は時間毎に出来高管表を書いていたのですが、今は直の終わりだけのラインがほとんどです。製造の管理者は、1日終わって、記録を見て、それをパソコンの管理表に打ち込み、その結果で生産の調整をしていました。
しかし、このシステムを使えば、全部のラインがその瞬間、瞬間、どう動いているか、出来高とラインの状況を瞬時に見ることができます。例えば当社のものづくりのモノサシで9641定義というのがあり、稼働率は90%という、なかなかレベルの高い目安がありますが、それに対して話し合いをしながら、その月の稼働率を決め、その稼働率のとおりできてなかったら、すぐ現場へ行く、というようなシステムにしようと思っていました。後追いでなく、瞬間的にリアルタイムに手を打てるということです。稼働率が、ぐっと下がっているとか、品質の問題が起きて停止している瞬間に管理職が動いてくれているとか。それが現場のオペレーターにとっては大事なことです。まさにリアルタイムに、何か起きたら、人間がそこに駆けつけるという。
決して新しい手法に取り組むわけではないのです。1日の出来高管理表で、本当は製造課長が1時間おきに現場を回りながら、チェックしていくのが大事なのですが、それがなかなかできない。ところが事務所にいてもパソコンで見られるようになりました。将来的には、掲示板にモニターを掛けて見るという様にしたいと思います。
現場の電子化、標準書類の電子化を進めるに当たって、出来高管理なども現場で入力ができたり、記録が見られることができなかったりとスピードアップにつながらない。作業の勘、コツ、ポイントなどを電子化し、動画で見る。言葉が通じにくい外国人でも動作で見せるために、社内のなかに、現場が自由に使えるネットワークを組んでいかないといけない。そのため現場の無線ネットワークというインフラ整備をしたいと思っています。
それは、研究会で東京電機の実施内容を聞いて、その発想が出てきました。東京電機と同じように、工場の中にLANを組み、全社員にタブレットを渡せるように。
昨日、ある会社の話を聞いたのですが、お客さんが発注するときに、工場を見に来るのですが、工場を見たときに、その工場がどれだけ新しい手法でつくっているか、それで相手の信頼性が全然違うという話でした。だからそれはいいことだと思います。売上増に結びつくようなことだと思います。
当社のラインも、稼働率だけでなく、不良の状況、どういう手を打つか、などにきちんと対応していることを、お客さんが来たときに見てもらいたいと思います。
IoT導入による顕著な成果、例えば全体の稼働率向上など
今はまだ顕著な結果は出ていない。使い始めて半年ですが、いまの稼働率と、使う前の稼働率を比較できていないのです。実はまだモニターしているだけの状態です。データをどう使って、どう分析していくか、モデルケースをつくって分析しています。それを現場でどう使っていけるのか、ほかにどういうデータが必要なのか、なども詰めないといけません。
モニタリングシステムを導入して、監視するというだけでは労働強化になるかもしれない。そうではなくて、なぜ、どのような原因で止ったか、という分析ができないと、本当の改善にはならない、などと私が言うものだから、なかなか進まなくなっています。
出来高だけでも、課長がすぐに見られるシステムにすればいいのですが、まだそこまで設置できていません。機器をつけて試行錯誤している段階です。その状態で、すでに半年経ってしまいました。
なぜラインが止ったのか、その要因は何十項目あるのですが、それを入れるためには、まだシステムを変えていかなければならなりません。それを今試行錯誤しています。
ホンダのF-1でその様な事をしていたのを思い出しました。栃木の研究所で、レース中のF-1マシンの状況が全部わかるように、マシンにさまざまなセンサーがついていて、レース中のコンディションがどういう状況になっているのか把握できる。だから最初に情報をつかむのは栃木の研究所。そして栃木の研究所が、レース中のF-1のピットに指令を送るという。それと同じことなのです。
当社の今の仕事の90%ぐらいは賃加工下請です。
今、当社はこれまで約40年かけて培った加工ノウハウをまとめたSPSという生産システムによって、極めて廉価の投資で最大効率を上げるラインをつくってきました。
今度はIoTの技術を入れて、女性や高齢者が入ってきても、不良も出ず、効率も落ちないラインをつくって、働き方改革ではありませんが、例えば70過ぎの高齢者に3時間ぐらいでもいいから出てきて仕事してもらえるような環境をつくりたい。
そういうことをして賃加工下請けでも絶対に世界一と言えるラインをつくろうという目標を掲げています。そのためにはIoTが相当活躍してくれるのではないかと思っています。
今、ラインをIoT化して、不良も出ない、効率も落ちないようなラインを目指しています。それをそのまま当社が設備の設置まで請け負う、いわゆるシステムインテグレータというのでしょうか、そういうようなことまで、IoTを入れ込んだら売り物になるのではないか、とも考えています。そうすればこういうことまでできますよ。など、そのようなことも、お客さんに仕掛けていければと。
これから自動車のEV化が進むのは確実です。ヨーロッパはものすごく進んでいて、中国も進みます。日本は多分、世界の中ではEV化はかなり遅れるのではと心配しています。それでもEV化の流れは世界の流れだから、それに対応していかないと生き残っていけないと感じています。
そこで超短納期の構想です。そういうのがこれから大事になってくると思います。だから、米国から受注して中1日で納められるぐらいの超短納期の技術ができれば、お客さんとの商談でも、中1日でできることが売りになるはずです。そうするといろいろな仕事が来ると思います。その中から将来の方向づけを出していければと思います。だからIoT物語を2本立てでいきます。物語パートⅠは量産の仕事は世界一と言える位のQ.C.Dをつくること。あとは超短納期を物語パートⅡで、いろいろな仕事にチャレンジしていこうという構想をしています。しかし先行きは見えていません。
研究会に参加した今の時点でのご感想。これまでの研究会を振り返った感想。
以上の発想は、研究会に参加しなければ出てこなかったものです。例えばIoT物語は、私が自分で整理した将来的な会社の方向性ですが、研究会に入ってから3カ月ぐらいで出しました。それが出なければ、賃加工下請けで、ずっと、もがいているような状況でした。ですが、賃加工でもこういう手が打てる、新しい方向づけで超短納期の試作体制ができるはずだ、そのようなことが明確化されたのではないかと考えています。
中小企業でIoTを導入してるところはまだまだ少ないが、何とかしなければいけないと考えてる社長は相当多い。そのような社長に対するアドバイス。
日本では圧倒的に10人ぐらいの規模の会社が多い。当社のように200人前後の会社は10%ぐらいだと思いますね。そうすると、われわれが導入したシステムを使ってやろうとしているようなことは、そのようなシステムを入れなくとも、現場をぐるっと回れば、全部分かってしまうでしょう。
繰り返しになってしまいますが、“IoTはツールに過ぎない”のです。なんでもメーカーが言っていることや他社と同じことをする必要はないのです。いつのまにかIoTを導入することが目的になってしまうようなことは本末転倒であると肝に銘じ、自社に合ったものだけ取り入れるので良いと思います。
最後に、これまで振り返って、これだけは言っておきたいという主張などがあれば。
当社の名前の知名度が上がりました。私も講演を頼まれるようになり、IoTの関係で3回ぐらい頼まれました。その講演の中で必ずIoT話をするときに、レースの写真も入れ、参加者の興味を引くようにしています。つまり、いつどこで気づきがあるかわかりません、常に考え気づきを大事にするということなのです。