現在、筆者が主催し、経済産業研究所で行われている「IoTによる中堅・中小企業の競争力強化に関する研究会」では、研究会委員である日立製作所、富士通、三菱電機から、中堅・中小企業向けのさまざまなIoTツールが紹介された。それらの内容は、本稿を読まれている中堅・中小企業の方々にとっても、これからIoT導入を検討する上で、「IoTを導入すればどのようなことができるようになるか」、を考える上で大きく貢献する情報である。
「中堅・中小企業向けIoTツール」を紹介しようとすれば、どうしても各企業の商品を紹介することになるが、本稿の目的は、各社のPRをするのでなく、現在、日本の多くの企業で開発中のIoTツールは、多かれ少なかれ、これから紹介する上記3社のIoTツールと類似性が高い。そのため、いま日本の多くの企業で開発中のIoT ツールの基本形・基本分類であると考えて頂いてもよい。それが、これから3社のIoT ツールを紹介する目的である。
今回は富士通のIoTツールを紹介する。
1 はじめに
富士通では、工場の製造設備から収集される稼働実績のログデータをもとに、製造工程の稼働状況を可視化するIoTソリューション「FUJITSU Manufacturing Industry Solution VisuaLine(ビジュアライン)」(以下、「VisuaLine」)を、2016年12月5日より販売開始した。
本ソリューションは、生産工程に関わる製造設備からのログデータを収集し、1製品ごとの稼働状況をグラフなどのさまざまな表現形式にて可視化。日々のグラフとの比較から通常よりも時間がかかっていることなどを一目で読み取ることができ、設備からのアラームや稼働停止が発生しなければ気づくことができなかった異常箇所の早期発見が可能になる。
これにより、ログデータから設備の不調や老朽化などを読み取ることができ、製造現場における新たな改善ポイントの発見や施策立案に活用することが可能である。
日本の製造現場では、製造ラインの設計や工程の見直しなどを日々図っているが、製造設備の異常などは設備からのアラームや稼働停止を受けて対策を講じるため、リードタイム短縮や効率化において、大きな課題となっている。
富士通では、2014年よりオムロン株式会社(本社:京都府京都市、代表取締役社長CEO:山田義仁、以下 オムロン)草津工場のプリント基板の表面実装ライン(SMT工程)にて、製造設備のログデータを活用した現場革新の共同実証に取り組み、6カ月で30%の生産性向上という効果を確認した。さらに、2015年に行った富士通アイ・ネットワークシステムズ株式会社(本社:山梨県南アルプス市、代表取締役社長:中村裕登、以下FINET)山梨工場のSMT工程における社内実証では、停止時間25%削減を達成した。
今回、富士通は、オムロンとの共同実証をもとに確立した稼働実績を線グラフにて見える化する機能をベースに、FINETでの社内実証で開発した動画連携などの機能を付加した「VisuaLine」を提供し、IoTによる製造現場の改革を支援していく。(図表1)
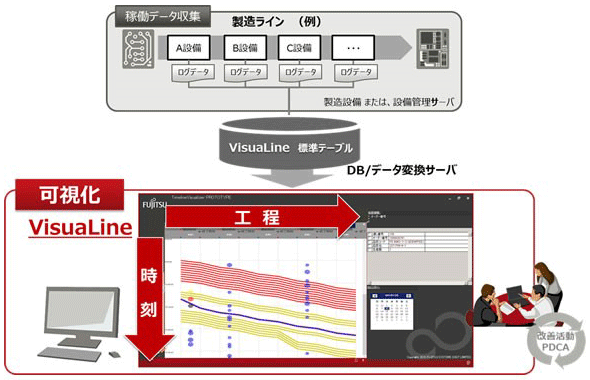
2 製造現場の課題解決に向けて
製造現場では生産効率向上に向けて多くの課題・悩みを抱えている。
例;
・現場の実態が、経営層と現場とで共有できない
・製造現場の実態は、現場に行かないと把握できない
・生産ラインのボトルネックや非効率箇所が特定できない
・数字を羅列した実績表では、製造実績の把握に時間が掛かる
・熟練の技術者でないと、生産全体の無駄が発見できない
・IoTを活用した製造現場の効率化をすすめたいが、どこから手を付けてよいか分からない
課題解決に向けて、製造現場では日々改善活動が行われているが、生産状況の把握に時間がかかる、改善すべきポイントが見当たらない・判らない、改善活動は限界に近づき、行き詰まっている、といった改善活動における悩みも抱えている。そこで、生産効率向上への気づきを与える新しい手法として、VisuaLineが製造現場の革新を実現する。
3 VisuaLine とは?
VisuaLine とは、IoTを活用した異次元の見える化(複数特許出願済み)である。(図表2)生産状況のバイタルともいえる「生産ラインの波形」で表現し、熟練の経験・技を必要とする生産ラインの把握が、誰でも簡単にできるようになる。
1. 製造実績を、工程×時系列でグラフ化
縦軸を時間、横軸を工程とし、製造実績の時系列データを、折れ線で表示することにより、ラインの生産状況を一目で確認できる。線形が平行で間隔が狭いほど生産効率がよく、線形に乱れが出るところが生産の異常箇所であると読み取れる。
2. 設備イベントも同時にマッピング
製造時に発生したイベント情報(エラーメッセージ、センサー情報等)もグラフ上にマッピングすることができるため、製造実績とイベント情報を同時に可視化し、異常箇所の発生原因を読み取ることができる。
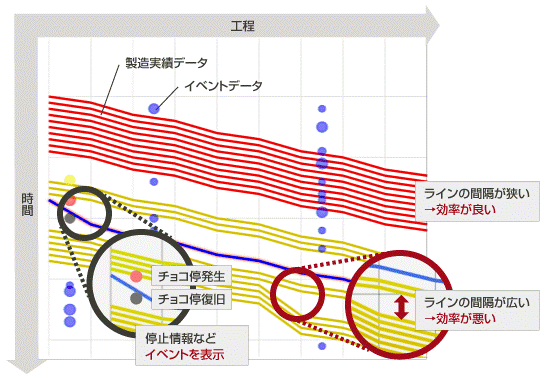
このような「生産ラインの波形」が生む効果は、
・製造上の異常箇所の発見や稼働実態の把握が容易に可能になる。
・新たな改善ポイントの発見や改善施策の立案をサポートできる。
・現場力を上げるためのコミュニケーションツールとして活用できる。
4 実証事例
VisuaLineは、富士通が製造現場とともに作り上げたソリューションであり、顧客との共同実証・社内実践により高い効果を実証している。以下2事例を紹介する。
4-1 オムロンとの共同実証事例
(1)導入前
導入前、以下のような課題を抱えていた。
・設備データを収集・現場へ提供しても、バラバラ・断片的で、うまく活用できない。
・エラーログから、潜在化した改善課題を熟練者の経験と勘で発掘していた。
・継続的に改善活動を続けているが、伸び悩んでいる。
(2)導入後
製造実績を設備イベントを収集した分析用データベースから、データを取り出して、グラフ状に展開して可視化した。(図表3)
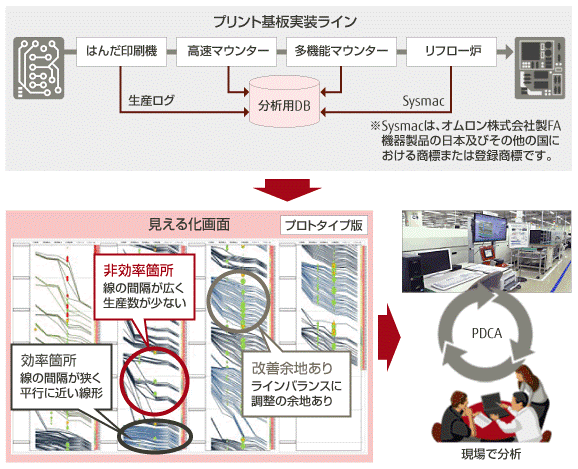
導入後の評価としてメリットが大きいものは、
1. 大きな改善効果
・製造現場の見える化により、改善ポイント把握の効率が6倍になった。
・改善ポイントの解消により、時間当たりの生産性が30%向上した。
2. 改善活動の革新
・設備データを可視化、現場の新たな活用方法を実現できた。
・生産全体の無駄が、誰にでも発見可能になった。
・視覚的に新たな改善ポイントを発見、改善の成果も検証が可能になった。
3. 現場の社員の意識変化
・ものづくりに前向きにとりくむようになった。
・他のチームとも、情報共有が進んだ。
4-2 富士通社内実践事例
富士通アイ・ネットワークシステムズ株式会社(FINET)山梨工場の北1号棟で実証が行われた。(図表4)
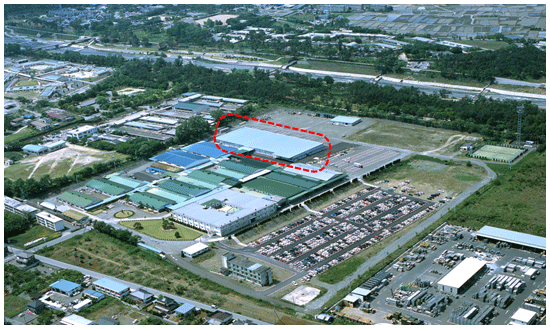
同工場ではPBX(構内交換機)等のネットワーク製品を生産しており、今回IoT取組を適用したのはPCB(プリント基板)製造ラインのSMT(表面実装)工程である。大量生産のラインもあれば多品種少量生産のラインもある。
1. 導入前
「見える化」を導入する前は、現場の製造状況がデジタルに把握できておらず、どこにボトルネックがあるのかを把握しづらかった。また問題の判別・対応までに時間がかかっていた。
2. 導入後(改善効果など)
1. 停止時間を全体で25%削減
・エラーによる製造遅れを発見することが可能となり、早めの対応で停止時間の削減を達成した。
2. 原因分析と対策のスピードアップ化
・1日遅れで把握していたライン実績を数分後に確認できるようになった。
・問題発生の現場で対応し、結果の振り返りも可能である。
3. 新たな気づきによる改善
・改善効果の実感により作業意欲が向上した。
・新たな施策(可視化ツールの充実・他ラインへの展開)による効果拡大を目指す。
見える化による課題解決のポイントは、製造作業を撮影し、ライン状況の表示グラフと時系列で連動させることで、人の動き・設備の状況を確認できるようになり、究極の現場の可視化を実現した。(図表5)
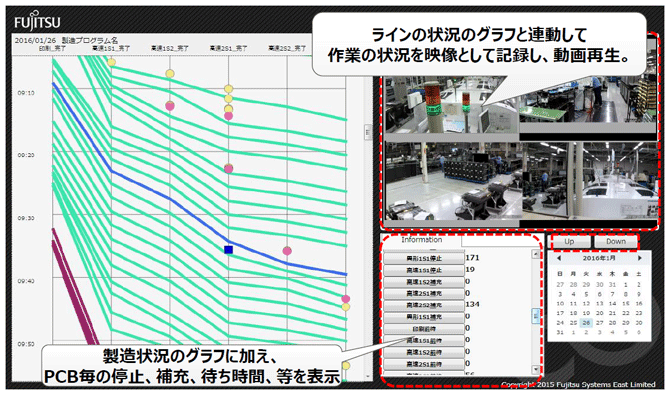
5 製造現場へのIoT導入を手軽に
VisuaLineが実現するIoTには、導入までに特別な(膨大な)準備作業は不要である。現時点で取得できている製造実績データ・工程データを活用し現場の可視ができるため、"すぐに活用する"ことができ、また"すぐに結果(効果)を実感する"ことができる。
この結果(効果)を積み重ねながら、取得する現場のデータを増やし、適用範囲を広げていくことで、効果が増大していく。
VisuaLineによって、製造現場におけるIoTは"遠い将来の構想"ではなく、すでに"現場にとって身近なもの"なのである。