オムロンは、草津工場において、製造過程の「見える化」を行い、生産性を30%改善している。同社の吉川浄グローバルものづくり革新本部長にインタビューしたところ以下の通り。
1 オムロンのものづくり
2015年度のオムロンの事業は、グローバル連結で8,336億円であり、FA制御機器、スイッチ、リレーなどの電子部品、自動車搭載のコントローラなどBtoBビジネスが全売り上げの約7割を占めている。交通など社会システムに9%、健康医療機器のコンシューマー商品が13%、9%がソーラーパワーコンディショナー、スマホ用バックライトなどである。一番大きな事業でも数百億円規模であり、数億から数百億の事業が100ほどにのぼり、幅広く手がけている。テレビや自動車のような数千億円規模の事業はない。センシングとコントロールが当社の技術であり、ここからいろいろな事業を生み出してきた(図1)。
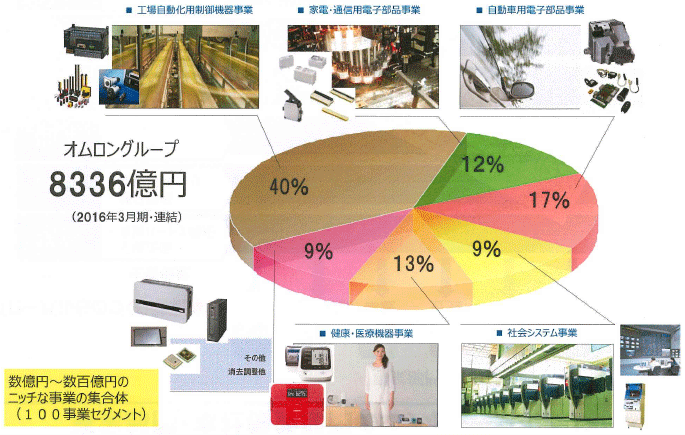
デジタル技術を活用してものづくりを進化させる領域は、エンジニアリングチェーンの革新により新商品開発を早める、製造プロセスそのものを改革して品質を上げコストを下げる、サプライチェーンの改革、商品そのものが新たな価値を生みもの、サービスと融合して新たな領域を生むものなど5つの領域がある(図2)。
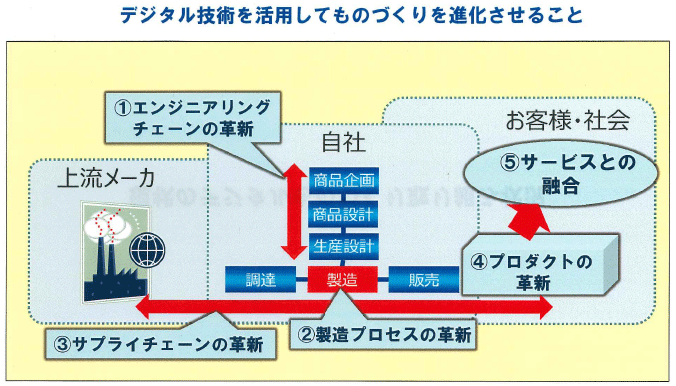
そのうち製造プロセスの取り組みでいえば、草津工場で行っている実装ラインの「見える化」は公開しており、ロボット革命イニシアティブ協議会で進めている「IoTユースケースマップ」にも掲載されている。実装工程の中の設備の情報を収集して、エンジニアが生産の状態を見えるように工夫することで、問題点を把握し、1年間で生産性が30%改善した。
1枚ずつのタイムラインという表現の仕方、すなわち「見せ方」の部分を富士通が開発した。情報収集のコントローラからマイクロソフトのSQLサーバーというデータベースに直結でデータを送るのはオムロンの技術である。データベースにリアルタイムに送っているデータをどのように見せたら現場の者が改善点がわかるか、というデータの表現の仕方を、富士通の協力を得て作り上げた。
我々はアイドリングストップと呼んでいるが、自動車が信号で止まるとエンジンが止まるのと同様、段取り替え、トラブルなどのとき、いままでは設備が止まっても後ろの方は電源が入ったまま、熱源はそのまま、コンプレッサーは動いたままであったのを、並んだ装置の状態を見て、待機電力まで下げる。どこまで下げれば、再稼働のときに立ち上がるか、というのはノウハウが必要だが、それを簡単な仕組みでコントロールする。実装ライン1本当たり、電力と空気を併せて2〜3割改善した。当社はニッチビジネスの集合体なので、1日に何十回となく段取り変えしている。スマホやパソコンのような量産型商品に比べ段取り変えが多く、設備の総合稼働率はそれほど高くない。だからこそ、このくらいのロスを改善できた。
実装ラインの「見える化」は、試行錯誤しながら行うもので、どういう風に見たいのか、こういう風に見ると問題が見えるのか、と言った現場知識に基づいた工夫が必要で、はIT専門家には難しい。現場20年の熟練作業員が要求する。このことから、ビッグデータをどう見たらものごとを判断できるのか、そこにはベテランの熟練者や技術者の技が必要だとわかった。そこが日本の強さである。「見える化」された画面を見て、どう改善すべきか、オムロンの熟練者が考える。
画面のなかで、密度が薄く、生産性が低い箇所は、「待ち」が発生している。それは、たとえば、装置が部品を取るときにミスをして、リトライしている。ノズルの状態が不安定になってくると、何度も取り直ししている。また基板に部品を乗せる際にバランスがとれていなかったがためにバランスロスが生じていた。それがタイムラインを見ることで簡単にわかるようになった。すると装置をどう直せばいいかがわかる。
これまでは、機械が動いていながらリトライするところまでは把握していなかった。そうしたリトライが発生していることがわからなかった。なぜなら結果として部品は取れていたから。装置のメッシュの管理の仕方が荒かった。明確に設備がトラブルしてメンテしないといけないという状態はわかるが、その前段階でリトライが発生する。この生産ラインは、自動ラインなので、元々、人がほとんどいないが、この設備を担当していた現場の担当者は、まさかこれほどまでに悪いとは思っていなかった、と言っていた。最初、これを見たとき、「えっ」と驚いていた。一番の肝は、自分たちができると思っていた以上の改善が出来た、というところ。このラインは飽くなき改善をしていて、従来も毎年生産性を継続的に少しづつ向上させてきた。それが「見える化」により一気に30%改善した。「ここが空いている」というのが明確になった。現場の人間にとっては全てやり尽くしていると思っていたが、新たな視点を導入すると一気に進む。そういうところは、まだまだあらゆるところにある。知恵が沸く領域がまだまだある(図3、図4)。
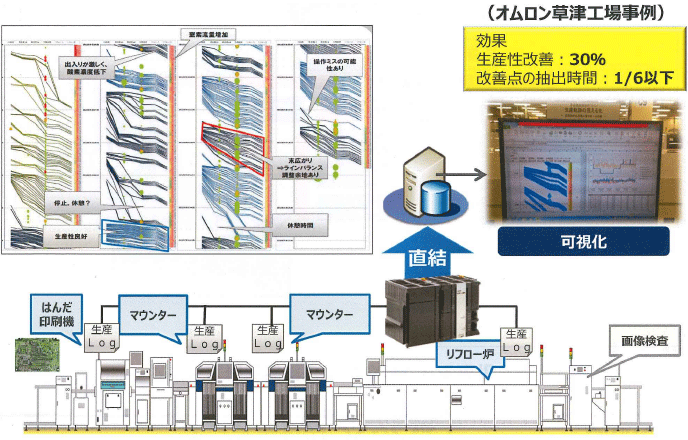
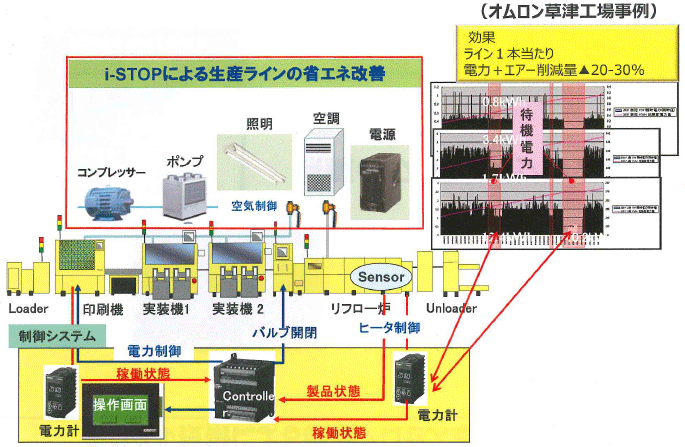
元々、PLCやシーケンサーと呼ばれる設備のコントローラがあったが、2011年にオムロンはオートメーション・コントローラを作った。これはデータを全て扱えるようになっている。ここからデータを上げやすくしている。従来のPLCは機器をコントロールする機能はあったが、そのデータを上げるプログラムを組むのは至難だった。我々は、この商品をうまく活用した事例として紹介している。ファンクション・ブロックと呼ばれるライブラリを利用することで、いろいろなデータが実用的なカイゼンに活用できるようになる。草津工場に見学に来られている方々は、是非、これをやりたいという話をされている。
現場で、収集、分析、アクションをするような「脊髄反射」の領域と、経営レベルの見方をする領域がある。「脊髄反射」をする領域は、日本の得意なところで重要な領域である。
現場のノウハウをデジタル技術で「見える化」するが、外に対してはブラックボックスにしたい。そうすると同じ設備を使っていても、我々の方が生産性を高められる。どこかではドイツがいうように企業間連携が起き、そこでは標準化がなされる。だが出来るだけ現場のノウハウをブラックボックス化し、現場の価値を閉じ込めて、競争力を高めるのが日本らしい進め方ではないか。
2 雇用との関係
ラインで働いている人は変わっていない。スループットが上がっている。オムロンはグローバルに工場を持っているので、草津工場の生産性が上がれば、生産性と物流コストの足し算の結果、中国で作って日本市場に納入することと日本で生産して日本市場に納入することのどちらがいいのか、生産性が高まると日本で作って日本市場に納入する比率が増える。草津工場のベテランのエンジニアは、世界の工場に助言できるようになる。海外でベテランがいない工場を指導するなど活躍の場が広がる。
直近の事例では、今、血圧計の生産を変えようとしている。オムロンは血圧計では世界でNO.1であり、これまではほぼ全量を大連で生産し、世界に供給していたが、ここ数年で、ベトナム、中国、日本の3拠点に変えた。これまでは日本での生産を縮小して中国での生産を拡大することでコストダウンを図ってきた。だが最近では日本でロボットでの自動組み立てを作り、日本に生産を戻しつつある。今や中国で生産した場合と比べて、コストがプラスマイナス数%の範囲に収まっている。Made in Japanのプレミアム商品が作れるようになった。その分、中国での単純労働が減って、自動化されたことは確かだが、日本の生産性が上がると、競争力を持ち、日本に仕事が戻ってくる。
草津工場では、雇用環境や仕事の内容はほとんど変わっていない。ラインのオペレーションは委託先が、技術的改良はオムロンが行っているという点も変わっていない。社員に対して何か特別な教育や訓練をしていない。サーバーにデータを吸い上げるところまでは当社の生産技術が出来る。収集したデータをどのように表示するとわかりやすく「見える化」できるかという領域について外部パートナーの協力を得て進めた。当社では、これからそのようなことができるIT エンジニアが必要になる。当社の生産技術は200人いるが、ITを用いて情報解析ができる人間は4〜5人くらいしかいない。現場もわかり、ITを使えるという人間を増やしていかないといけない。外部から180〜300万円/月のSEを入れても割に合わない。これからは生産技術がITを使えないといけないことは痛いほど感じている。エンジニアの絶対数が足りなくなる。データを吸い上げることと、そのデータを「見える化」することは違う。IT 技術者をどこから確保してくるか、IT の知識をどう学ばせるか、を考えないといけない。IT技術者も現場と対話ができなければ役に立たないが、そのような人はなかなかいない。
当社は中国で約30%生産している。中国で人件費が上がってきている中で、生産性をどう高めていくかという検討をしている。今試みていることは、中国ではセルラインによる生産をしているので、そのセルラインの状態を、同様に、「見える化」しようとしている。セルラインの設備の状態も「見える化」する。これまでは、設備が止まれば、ラインのリーダーがボタンを押すと、生産技術者が来て修理し、再立ち上げした。これまで中国で作り上げてきた役割分担である。それが、ラインの状態が「見える化」されると、ラインの女性リーダーがセルラインの4〜5名の仕事の割り振りを再検討することができる。これまでは専門の人間が時間を測ってラインのバランス設計をし、ラインリーダーと生産技術者が役割分担していたが、よりもう一歩、ITツールを見て、ラインリーダーが生産性改善のバランスまで出来るようになる。さらに設備がとまったときの一時対応が可能になる。すると生産性が格段に上がってくる。それはITツールを使った人の能力の拡張であり、より上位側に仕事ができるようになると生産性が上がる。そのような試みをしようとしている。