開催日 | 2008年7月11日 |
---|---|
スピーカー | 本道 和樹 (経済産業省製造産業局政策企画官) |
モデレータ | 山田 正人 (RIETI総務副ディレクター) |
ダウンロード/関連リンク |
議事録
※講師のご意向により、掲載されている内容の引用・転載を禁じます
キーワードは「サプライチェーン」と「信頼」
「サプライチェーンマネージメント」という概念は80年代にアメリカで言い出されたもので決して新しいものではないが、今回「サプライチェーンの強化」ということをキーワードに持ち出した背景には、ものづくりが直面する課題の変化があります。サプライチェーンマネージメントの元来の主旨は、川上・川下を視野に入れ全体的なコスト削減と納期短縮など効率化を図ることにありました。しかし今日では、化学物質規制といった資源環境制約への対応、安全・安心への配慮、顧客に対する供給責任の遂行といった、単なる効率追求とは違う、顧客や社会との関係における「信頼の向上」という観点から、サプライチェーン全体を視野に入れたマネージメント、全体最適化がものづくり企業にも求められています。
サプライチェーンのアジア展開
近年、製造業はグローバル競争の激化とアジア地域の成長を背景に、アジアへの工場進出とサプライチェーン拡大を進めています。特にここ10年では、中国とASEAN諸国で日本製造業の現地法人が増えていると同時に、これらの現地法人が日本から調達する中間材の金額も急増しています。また、在アジア日系企業の販売先の内訳を見ると、2割が日本への輸出(逆輸入)、5割強が現地販売となっていて、後者の比率が少しずつ上がっている状況です。そうしたことからも、製造業のアジア展開が「低コスト製品を日本に逆輸入する」というより、「拡大するアジア市場の活力を取り込む」性格が強まっていることが伺えます。
アジア規模にサプライチェーンが広がる一方で、国内拠点数も2002年を底に件数・面積ともに回復傾向にあります。背景として、国内の景気回復に加え、優秀な人材の確保といった国内立地の意義が再評価されていることが挙げられます。特に最近の5年間では、素材、中間材、生産財の工場新設割合が高いとのアンケート結果になっています。
そのような中、国内外の生産拠点の使い分けについては、特に汎用品の量産については海外拠点を積極的に活用する傾向が見られ、今後内外の経営資源を戦略的に活用する動きはますます進んでいくものと見込まれます。また、こうした分業のあり方は、日ASEANのEPAなど制度的な変更によっても今後変わっていく可能性があります。
サプライチェーン拡大に伴う課題
今回の白書では、サプライチェーンのアジア展開が我が国経済にもたらすメリットについて述べる一方で、それに伴う課題についても分析を試みました。
- 基盤産業(素形材産業、等)の経営基盤強化
- 川上・川下を含めたサプライチェーンの強化
日本のものづくりを支える基盤産業も昨今、アジアとの激しい競争下に置かれています。自動車関係部品に関しては、技術面だけでなく、生産能力、納期遵守、機動的対応といった面でも日本の方が調達先から高い評価を得ています。しかし、電気機械分野ではその差が相対的に縮まりつつあります。また、現地日系企業による日本からの調達額自体は伸びていますが、調達全体に占める日本からの輸入の割合は右下がり状態にあり、現地のものづくりにおいて日本からの輸入に依存する要素が減ってきていることが伺えます。さらに、自動車分野においても、調達側の企業は今後日本からの輸入を減らしていく方針とのアンケート結果となっています。
国内の川中産業の状況
日系企業の現地調達割合が増加する一方で、日本の基盤産業は国内でもアジアとの競合に直面しています。
たとえば「日本の強み」の代名詞と思われている金型にしても、自動車等で使われるプレス用の金型では日本が依然として優位にありますが、金型全体の内需に占める輸入割合(輸入浸透率)は右上がりに増えている状況です。具体的には、プラスチック用の金型の輸入が増えており、特に対韓国で収支が赤字、それも近年拡大の傾向にあります。そうした状況から、国内企業はアジアの日系企業はもとより地場企業とも今後競争が激化すると見ています。
それを迎え撃つ国内基盤産業の状況は決して磐石とはいえません。近年の景気回復で基盤産業も増産・増益を享受しているところが少なくありませんが、利益水準に関しては、「黒字ではあるが設備投資、研究開発投資、人材育成は十分に行なえない」との回答、あるいはそれより悪い状況との回答が過半を占めています。つまり、当面は景気回復の追い風を受けても、中長期的な経営基盤は決して安定しているとはいえない状況です。素形材産業については、「簡単なものは中国に、ハイスペックな技術だけ日本に残ればよい」といった類の意見も聞かれますが、企業へのアンケートによれば「ハイスペックだけでなくロースペックな技術についても国内に必要」とする回答が実に7割に達しています。国内需要への迅速な対応や新製品開発のための試作に必要だからです。
日本のものづくりが中長期的に競争力を維持するには、電機、自動車といったセットメーカーだけが儲けるのではなく、川中の部品・素材メーカーも適正な利益を確保できる環境が必要です。そうした認識から、経済産業省は「下請適正取引等の推進のためのガイドライン」を昨年策定し、さらに今年4月から全国47都道府県に「下請かけこみ寺」を設置して相談に応じています(6月上旬までに500件弱の相談件数)。
また、中小企業が多くを占める素形材メーカーは、セットメーカーと比べて海外展開が遅れている傾向にあります。そこで政府としては、日本貿易振興機構(ジェトロ)による情報提供、FS支援、さらにはファンドによる現地法人設立支援、中小ものづくり高度化法に基づく技術開発支援を通じて、これらの海外進出を後押ししています。自治体レベルでも、海外展開を支援する動きがあります。
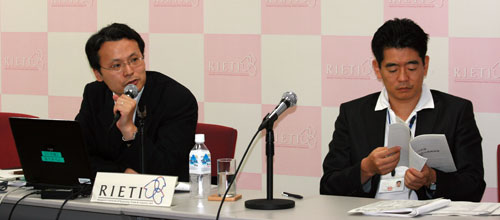
サプライチェーンをめぐる最近の変化
最近のサプライチェーンに関しては、コスト削減のための標準化が進む一方で、カスタマイズによる差別化という1つの変化が見られます。近年、いわゆる「ケイレツ」が崩れ、取引構造がメッシュ化したといわれますが、それは企業間取引がドライになったことを必ずしも意味しないと思います。たとえば液晶パネルフィルムや電子材料など、機能性化学といわれる分野では、設計・開発段階から素材メーカーと徹底したすり合わせをすることによって、製品の差別化(小型化、軽量化)を図り競争力を維持するセットメーカーも多く見られます。一見同じような素材でも、提供先によって少しずつカスタマイズした素材を提供しています。
サプライチェーンの地理的広がり、在庫の削減などが競争力強化につながる一方で、災害等による供給途絶、さらには取引先からの技術情報流出といったリスクにも対処する必要性が高まっています。
グローバル競争が激化する中、価格変動が激しい分野では、サプライチェーンの拡大に伴い在庫削減が進んでいます。こうしたサプライチェーンの効率化は、競争力向上につながる一方で、予期せぬ供給途絶リスクという脆弱性もはらんでいます。最近では、2007年7月の中越沖地震で自動車部品メーカーが被災したことによって自動車メーカー全12社の生産が一時停止したというショッキングな事例があります。そうした理由以外にも、寡占化が進む電子部品・機能性化学業界では、欧米等の企業から事業継続計画(BCP)の要請が寄せられる例もあります。そのための対策に関して、電器大手では「調達先の分散化」が回答の8割超を占めていますが、自動車大手では分散化以外に「調達先との事前協議」や「復旧支援の検討」という回答も目立ちます。単純に在庫を増やすのではなく、自社のサプライチェーンの強み、弱みや途絶のインパクトを踏まえて、競争力を損なわない対応を検討することが重要です。経済産業省としても、中小向けのBCP作成ウェブサイト等を通じて支援しています。このように、自社だけでなく、サプライチェーン全体を管理・強化していく視点が重要です。
信頼の回復
さらに今年のものづくり白書では「ものづくりへの信頼の回復」として、特に製品安全と偽装問題を取り上げています。近年、製品のリコールや事故報告の件数が急増するだけでなく、再生紙や鉄鋼での偽装問題が発覚する等、ものづくりに対する信頼を揺がす事件が相次いでいます。原因は一概にはいえませんが、競争激化と、それによるコスト・効率優先傾向ないしコンプライアンス軽視がその背景にあると見ています。また、製造スキルの低下といった人材面の問題、さらには組み込みソフトの使用拡大といったものづくり自体の高度化・複雑化も要因に考えられます。こうした中で製品安全を徹底するには、現場の品質管理も重要ですが、経営陣の主体的取組が不可欠であり、また設計・開発段階から予見可能な誤使用を視野に入れるなど設計思想も含めた取り組み強化が重要と思われます。さらに、アウトソーシング比率が高い企業・業種では、サプライチェーン全体で安全性を高めるような共同の取り組みが必要です。
資源・環境制約への対応
特にものづくりに関連する事柄として、REACH(リーチ)規則が2007年欧州で施行されたことを始め世界的に化学物質規制が強化される傾向を背景に、高リスク化学物質の排除・削減が調達条件として重要視されるようになっています。その対応如何によって取引拡大に成功した企業がある一方で、取引停止に至ったケースもある等、環境制約への対応は企業経営を左右する問題になっています。
また、資源制約がますます高まる中でさらなる省資源化を図るには、個々の企業だけでは限界があるため、川上・川下の企業間連携がより一層重要になります。昨今の資源高は製造業にとって試練ではありますが、逆に日本の強みが活かせる場面でもあり、企業間連携をテコに競争力を強化するチャンスにもなると考えています。
ものづくり強化に向けた人材育成
今日、正社員に加えて、パート、期間工、派遣、請負といった多様な就業形態の人々がものづくり現場を支えています。また、非正規労働者の役割も、従来のような単純作業だけでなく、一定の専門性ないし判断力が求められる業務にも拡大しています。非正規人材の活用については、突発的な業務量の増大に対応できるようになった、正社員が高度な業務に専念できるようになった、といったプラスの評価がある一方で、ノウハウの蓄積・伝承や欠勤・離職への対応といった面での課題も指摘されています。
今後のものづくり基盤の底上げを図るためにも、非正社員に対して正社員と同等の能力開発機会を確保する等、就業形態の多様化に対応した人材マネージメントが必要です。実際に、非正社員の正社員登用やパートの待遇改善に乗り出した企業もあります。政府としても、厚生労働省中心にジョブカード制度等によりニートの正規労働者としての就労を促進する一方で、経済産業省においても人材投資促進税制の改正等ものづくり人材の育成に力を入れています。
質疑応答
- Q:
中国の外資政策・優遇策が昨今非常に変わってきていますが、そうした変化はサプライチェーンにどう影響してくるのでしょうか。
また、石油価格の上昇はサプライチェーンにどういった影響を与えるのでしょうか。
- A:
数年前から、中国ともう1つの国(例:ASEAN諸国)に生産拠点を分散化する「チャイナプラスワン」の動きがいわれていますが、ご指摘の外資政策、さらに労働法制の強化によって、こうした動きに拍車がかかる可能性もあります。また、日本-ASEAN間経済連携協定(EPA)も分業体制をダイナミックに変える要素となり得ます。
原油に限らず資源価格の高騰によって、日本メーカーの分業体制に変化が生じることは十分に考えられます。たとえば鉄鋼では、日本の鉄鋼メーカーがブラジルで高炉を作る動きが出ています。
- Q:
特に調達のメッシュ化が進む電機・電子分野で欧米メーカーのEMS比率が非常に高くなっている印象です。そのような中、日本のセットメーカーに代わって、台湾や韓国の液晶メーカーが日本のサプライヤーの得意先になりつつあると思われます。
それに関連して、新興市場といわれる国々でシェアを拡大しているのは主に欧米メーカーだと聞きます。日本の部材メーカーやセットメーカーが国際的競争力を高めるには、どうした施策が必要でしょうか。
- A:
新興国と一口にいっても国によって状況は違います。たとえばブラジルでは、日本ブランドよりもサムソン等の韓国メーカーの方が浸透しています。一方、インドなどでは特に高級品部門で日本ブランドは根強い人気があると聞いています。ブラジルのような市場に関しては、「良いものを作れば売れる」という日本の論理が必ずしも通用しない面もあり、ブランド戦略の見直しが必要と思われます。
海外のセットメーカー(最近では電器分野)が国内外でシェアを伸ばした場合、日本の部材メーカーと供給関係を結ぶことから、すり合わせ等を通じて国内企業の独自技術が流出することを懸念する声もあります。そうした状況に陥らないためにも、日本のセットメーカーにもう少しがんばっていただきたいところです。
- Q:
サービス業の生産性の低さが昨今問題視されていますが、RIETIの研究では製造業の生産性もかなり低いとの結論に達しています。今回の白書でサプライチェーンを取り上げたのは1つの見識だとは思いますが、次回は生産性低迷の一因といわれるITの戦略的活用の欠如といった問題に焦点を当てていただきたいと思います。
- A:
生産性については中小企業白書で取り上げる関係から、今回はあまり焦点を当てないことにしたという経緯があります。私自身も特に中小ものづくり企業の生産性はまだまだ改善の余地があるところがあると見ています。
この議事録はRIETI編集部の責任でまとめたものです。