Abstract
In April 2016, the "Seminar for Strengthening Competitiveness of SMEs by introducing IoT and AI" was launched by the author, in which nine model companies participated.
Outputs of IoT and AI investments have been measured for several companies in terms of increase in sales. The model companies for this research were all manufacturing companies. The model companies in this research included B to B, B to C, manufacturing service industry, and micro enterprises. Knowledge and experience were accumulated through this research in order to smoothly introduce IoT and AI to SMEs and produce significant increases in sales. Most importantly, the "procedural manual" for IoT and AI introduction to SMEs has nearly been completed. This output is probably the first of its kind in the world.
Some local governments which participated in this research as observers and learned the technical know-how to introduce new technologies are also starting to host some similar study groups since 2018. This movement is gradually spreading throughout Japan.
The "Digital Model City Project" started in 2020 in Ueda City, Nagano prefecture. By introducing digital technology to SMEs in Ueda City, company sales are expected to increase encouraging the development of SMEs in Ueda City.
1. Seminar held in Tokyo since April 2016
The following two conditions were required for the participation of model companies in this seminar:
1) Investment in IoT and AI
2) Disclosure of all "trial and error experience" gained while introducing IoT and AI. This kind of experience is not always shared in public, being considered "corporate trade secrets."
Instead of providing free consulting services in the form of a seminar to the participating model companies, it was requested that all "trial and error experience" be shared with SMEs throughout Japan. This seminar is in the public interest and aims to strengthen the competitiveness of all SMEs throughout the nation.
The following media have been used as means of disclosure of such "trial and error experience."
1) RIETI Policy Discussion Paper
*RIETI - The Research Institute of Economy Trade and Industry
2) Book Koichi Iwamoto and Yusuke Inoue (2017). "SME's Tried IoT" (Nikkan Kogyo Shimbun Publishing).
3) RIETI Webpage
4) Nationwide lectures, magazines, etc. by the author
The purpose of the seminar is as follows. The market for the fourth Industrial Revolution is expected to be large. Articles on IoT and AI appear in newspapers nearly every day. However, these articles concern only large companies, with no exceptions. Articles about the successful introduction of a full-scale IoT and AI system into Japanese SMEs are extremely rare.
The reason is simple; most presidents of SMEs do not understand the technology well enough. There are two main reasons for this. First, understanding IoT and AI technology is difficult. Second, the benefits to their company are not clear.
Generally, there are few SME presidents who are able to decide to invest in IoT and AI just by watching a "success story," or the final result of other companies. They will wonder if the same practice is applicable to their companies. They will also be concerned about the potential obstacles that other companies had to overcome before the final transition to new business models. These anxieties make it difficult to move a step forward toward investing in new technologies.
The purpose of the seminar is to share the "trial and error experience" that is normally kept inside the company. There is a lot of uncertainty and anxiety regarding new technologies, such as whether or not IoT and AI can be utilized, whether the technology can be controlled, whether investments can be recouped, and whether the current workforce can really learn to use them. Unless these concerns are addressed and solutions are found, SME presidents will not be able to decide whether to invest in IoT and AI.
Therefore, from April 2016, we organized and hosted the "The Seminar for reinforcing the competitiveness of SMEs through the introduction of IoT and AI," in which nine model companies participated.
By sharing the experiences of the model companies through the whole process from start to finish, including the trial and error process, presidents of SMEs across the country will be better informed about the benefit of introducing new technologies.
This Seminar adopted the case study approach used in MBA programs in which experiences of the model companies are analyzed. While there is no official consensus on which strategy is the gold standard of corporate management strategy, the case study approach is considered highly effective for learning lessons about the corporate management in companies that utilize new technologies.
Similarly, there is no standard management strategy when introducing IoT and AI to SMEs. We can only learn from the success of similar companies. Since such successful experiences are normally kept confidential, we decided to analyze the model companies in depth by adopting the case study method.
Nine model companies participated in the seminar:
1) The first phase (2016): We analyzed the "machine manufacturing industry", the core of SMEs in Japan: Nitto Electric Manufacture Co., Ltd., Shoda Manufacturing Co., Ltd., Daiichi Fab Tech Co., Ltd., Tokyo Electric Industry Co., Ltd. Two companies are B to C businesses, the other two B to B.
2) The second phase (2017): we expanded to the manufacturing service industry. Nippon Refine Co., Ltd., Metal Technology Co. Ltd., Shinohara Press Service Co., Ltd.
3) The third phase (2018-19): we further expanded to include smaller scale manufacturing industry: "Nonaka Industry Corporation" (40 persons) and "Fukai MFG Co., Ltd.," in order to target small companies with a few dozen employees.
2 Experience of IoT and AI investment of the model SMEs
2-1 "Tokyo Electric Industry Co., Ltd."
This company is a manufacturer of emergency electrical generators for disaster prevention. The company is responding well to increasing demand due to the increasing number of disasters in Japan. However, they face the following problems.
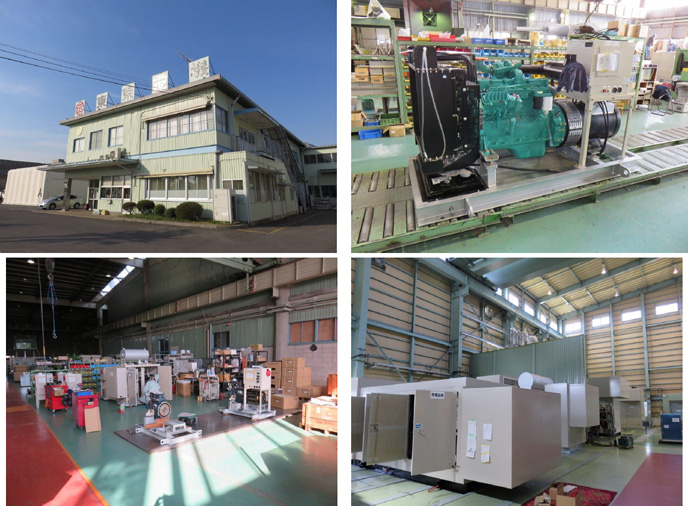
1 Solution utilizing IoT: inefficient data management and production system
In the design process of a power generator, the blueprint is created and stored on paper. The pre-sales inspection data is first written on paper then manually typed into the computer, which allowed for data entry errors.
The warehouses were full of paper blueprints and data management was extremely inefficient. In cases of unexpected customer orders, designers of the product frequently had to inquire about paper blueprints stored in the warehouse. Also, information sharing of the latest information during meetings was inconvenient and inefficient.
2 Solution utilizing IoT: information management by going paperless
The solution that would reduce paper and centralize information was achieved by using a production management system. After careful consideration by the task force on IoT, the company implemented a form processing system with a tablet terminal. The experiment started in September 2016 showed an improvement in productivity. Therefore, in March 2017 full-scale introduction started.
3 Investment vs. return
Double manual input was reduced due to the introduction of the tablet terminal. Smooth communication with customers and department heads was achieved thanks to the new ability to display and share data (such as drawings and photographs.)
The IoT investment cost approximately 4 million yen and required seven months to implement. It resulted in the reduction of work-hours. Even after one office worker retired, the production processes maintained operation without any problems (3 million yen in personnel expenses and 2 million yen in welfare expenses have been saved.) The investment made in new technologies by Tokyo Electric Co paid off within one year while achieving paperless operation, and the centralized information system was completed in seven months.
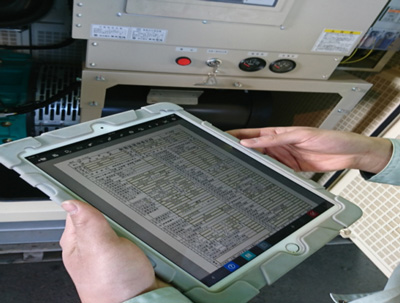
4 Effect
Before the IoT investment, customers had to visit the factory to inspect the performance of products visually and to confirm some important performance data and the all of detailed data were returned to the customers from the factory on paper in the mail some days later. Now, with the help of a tablet device, all of the detailed inspected data on products performance can be handed on to the customers before leaving the factory.
This new business style appealed to customers and improved their reputation in the small world of the emergency power generator industry. While the industry's sales of emergency power generator as a whole increased by +2% in 2018 compared with the previous year, that of the sale by the Tokyo Denki Co. increased by +10%.
5 Impact on motivation of employees
The introduction of IoT benefited Tokyo Electric Co. by enhancing the motivation for customer service. By giving tablets to each employee, and installing a projector in the meeting room, employees were more effectively able to communicate with customers while receiving immediate customer feedback.
During factory tours, it became more common for staff to greet the touring customers in a friendly manner. The employees say they are greatly encouraged by customers saying "Tokyo Electric has become a different company." It was a surprise to the participants in the seminar. In addition to the direct effect of IoT, it helped change the work environment.
6 The next step
The next step for Tokyo Electric is to install a communication device in the electric generator so that it can wirelessly transmit operational data that is useful for maintenance and other after-sales services. Such higher value-added products will help differentiate their products from those of other companies. This line of product is now available for sale and will be marketed soon.
7 The next-next step
The next-next step is to put QR codes on the company products. Development is now underway so that when a maintenance worker visits the customer, information such as the circuit diagram, past operational data, and maintenance data stored in the company's main server can be retrieved from his/her tablet through the QR code.
2-2 Daiichi Fab Tech Co.
This company has 27 employees and annual sales of 300 million yen. They are a Tier 3 parts manufacturer, performing metalwork using the latest processing machinery, such as 3D CO2 lasers and YAG composite machines.
The goal of the company in joining the seminar was to improve the capacity utilization rate of production facilities. The capacity utilization rate of the production facilities fluctuates greatly with quantity of customer orders. Half-finished parts were piled up in front of specific equipment which was in full operation, while other equipment was left idle.
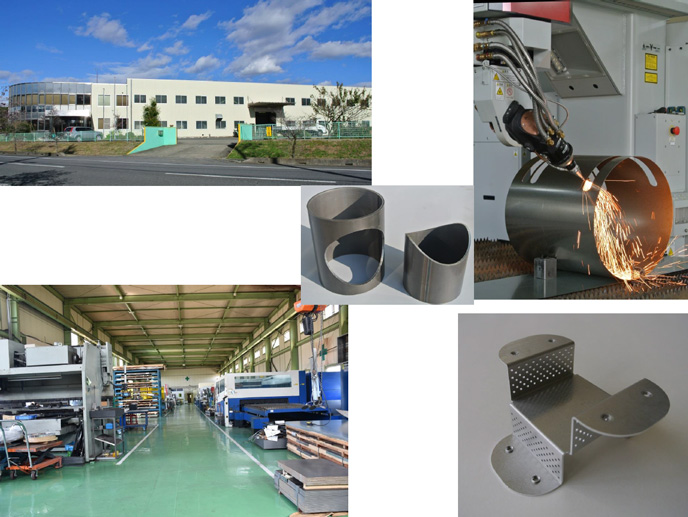
1 Solution through IoT: data collection and personnel training
In order to collect data using IoT, personnel training was found necessary. The company was not sure how to collect what type of data. The company consisted of a president, two female office workers and a number of technicians/machine operators, but it lacked IT engineers. Thus, this IoT project was assigned to one of the female office workers. She joined a technical course offered by the Industrial Technology Institute of Ibaraki Prefecture.
2 Investment vs. return
In the company factory, there are about 30 machines in total. The entire flow of parts operates smoothly if the three machines used in the first stage of metal processing operate without a problem. Therefore, they borrowed 800,000-yen worth of sensors from the Industrial Technology Institute and installed them on the three machines and began to measure the operating rate.
3 The next step
The company succeeded in collecting data from the three machines. The final aim was to maximize the production capacities of all machines using the collected data.
To this end, the president began to show the previous day's operation rate data to workers at the daily morning meeting to warn them not to accumulate half-finished parts in one place. After this practice started, the utilization rates began to level off and the company's order capacity increased. The sales increased by 30% (about 90 million yen) in 2018.
4 The next-next step
The company is planning to market this system which they have successfully adopted in their company.
2-3 Nitto Electric Equipment Co.
Nitto, a manufacturing company, introduced RPA to the design department. In general, RPA is commonly used for office work in the general affairs section in particular and often used in the banking industry. Therefore, it was thought that RPA would be difficult to introduce in the manufacturing industry. Nitto adopted it in the design section of the company.
RPA was adopted so that employees can concentrate on creative work, while RPA takes over repetitive work. RPA is used to output the drawings from CAD data. Before RPA was implemented, the same job had to be done manually. Since the introduction of RPA, designers only need to save the drawing data in a computer folder which RPA prints automatically based on the set schedule.
RPA is managed with a task scheduler, which is the most important part in this system. If the data is input by 15:00, RPA automatically starts printing. Otherwise, designers need to do the printing by themselves. Each diagram takes approximately 20 minutes to print. After introducing RPA, 20 hours per month is saved per design worker.
3. My impression of the seminar
Impression 1
Our seminar analyzing 9 model companies was held in Tokyo, the capital city of Japan. With this limited number of models, it is impossible to represent all SMEs throughout Japan. Some local governments that participated in this seminar are now starting similar seminars in their local prefectures. This practice will be a step forward in spreading information regarding the benefit of introducing IoT and AI throughout Japan.
Japan is "a country of SMEs" where 99.7% of the companies are SMEs. If the productivity of SMEs does not improve, the overall productivity of Japan will also not improve. Consequently, the improvement of productivity using information and communications technology is an urgent issue during the fourth industrial revolution.
Impression 2
One significant achievement of this seminar was that the model companies became more aware of the fact that they were now seen as "pioneers in the IoT and AI field" as media exposure and lecture requests increased, in addition to the initial benefits seen in improved productivity resulting from investment in IoT and AI.
4. The Seminar for reinforcing the competitiveness of SMEs through the introduction of IoT and AI to be carried out in Ueda City in Nagano starting from 2020
"The Seminar for reinforcing the competitiveness of SMEs through the introduction of IoT and AI." started in April 2016 and did not limit the targets of the model companies by location. From 2020, a new project was launched to carry out the industrial development of a specific city, by introducing IoT and AI to model companies located in the specific city. In other words, promotion of regional economies was added as a new objective in this project.
As a first step of this project, a seminar was held with three target companies from Ueda-City, Nagano prefecture in attendance. The strategy to realize the promotion of the regional economy was as follows:
The model companies of Ueda-City invest in IoT and AI during 2020. Their results are measured, and "trial and error experiences" are shared with other companies in the city in order to promote IoT and AI investment. Since this seminar was held in the public interest, the participating companies received free IoT consultations in exchange for expertise gained and an agreement to disclose any such expertise in the public interest during this project.
5. Difficulties in Introducing IoT and AI to SMEs
1) Discussion start in parallel
The initial stance of the SMEs tended to be doubtful of the benefits of implementing IoT, or how IoT can be utilized within their organization. The initial stance for the IoT system providers is that they are used to receiving orders from large companies with pre-determined specific specifications. Therefore, it is necessary for them to determine the concrete needs of the SMEs, and develop an order based on those specifications. Both parties to the discussion tend to start in parallel lines that do not meet without some effort. In order to move forward, minimum levels of mutual understanding are necessary in order to work towards compromise. If the efforts are abandoned early on, the discussion becomes fruitless.
2) (Unidentified Company) Failure to Concretely Understand Actual Current Issues
SMEs have vague parameters in term of their needs. They want to increase sales, productivity, value added and market share, and to reduce costs and improve quality. IoT cannot be effectively introduced using such vague parameters.
The introduction of IoT will move forward when the company develops specific, concrete definitions of their issues and how IoT can be specifically utilized to resolve those issues and reach their goals. But for years, many SMEs have failed to concretely grasp the issues they face as they actually are. The IoT system provider can explain past successful cases, but this usually does not match the present customer's needs. Each company's issues and their solutions are different.
3) First resistance encountered
The workers in a factory take pride in doing their job properly. When the idea of IoT adoption is brought up, the workers often interpret this as the management seeing their work as "faulty." It is thus safe to assume that an IoT system provider faces resistance by factory workers in their initial meetings. IoT investment thus requires strong leadership by the president.
4) Presidents must decide
After discovering the actual issues facing the company, many solutions are discussed. But the final solutions must be decided by the president of the company. This is because for SMEs, IoT adoption brings significant internal changes to the company, including internal systems and employee training, while at the same time requiring redesign of the organization. This internal situation is kept confidential from non-management personnel and only the president decides the investment amount. Only the president can lead his or her employees in a leadership role. The IoT system provider will not be able to find the best system or implement it without the president's decision.
5) Need to assume labor-intensive production in a factory
The production lines in factories of large companies are becoming increasingly automated. Because of the high volume of value-added products produced there, it is less expensive to automate than maintain the cost of labor. However, many of the production lines in SMEs are not highly automated and manual manufacturing is done by the factory workers. The labor costs for relatively small production output are cheaper than implementing full-scale automation. When considering introduction of IoT into SME production sites in a factory, it is often necessary to assume production by laborers instead of fully automated systems.
At sites where labor-intensive production is carried out by workers, there are no electrical signals connecting the production process, which is a prerequisite for digitalizing and collecting data in a factory. Current IoT systems are designed for large and highly developed factories; they are built on the assumption that electric signals are ubiquitous in the workplace.
6) No Systems engineer
SMEs usually don't employ system engineers in the company. Even companies that claim to be IT-enabled often just buy and use business management software packages for their office work. They have no experience in development, operation, maintenance or updating systems for the factory. It is therefore difficult to communicate between SMEs and an IoT system provider, and after implementing IoT, there is no one to maintain it in a typical SME. It is quite surprising, but few people in the SME world understand the importance of IoT investments. Even now, many presidents say that filling out a piece of paper or just a phone call and a fax is enough.
6. Conclusion
In 2013, Germany announced the Industry 4.0 initiative. In 2014-15, I was invited by many organizations located in non-central cities in Japan to give seminars on IoT. Despite the success stories I presented in my presentations, none of the presidents of the SMEs in those areas implemented IoT.
I interviewed them on their reasons for not intending to implement IoT during a reception after the seminar. Based on this information, I set up a study group in April 2016. The purpose was to identify the difficulties facing these enterprises by conducting case studies using actual model cases.
The presidents of the SMEs I interviewed simply said that they were not sure if they should implement it, but I did not understand what they were not sure about. Therefore, by dealing with actual model cases in the study group, I wanted to clarify the unknowns and obstacles to introducing IoT and AI to SMEs.
Once the issues are clarified, progress towards introduction of IoT may be possible from the president's perspective.
By having nine actual companies serve as models, it became clear what discussion is necessary when attempting to implement IoT and AI in SMEs.
This study group was a model study group held in the capital Tokyo, but similar initiatives were launched by several local governments since 2018, drawing on the management expertise accumulated by the initial study group.
At present, based on the results of these local governments' efforts, other local governments are following suit. If this initiative expands, it will eventually spread across all of Japan.
This is the objective the study group has aimed for since the beginning.
Japan is "a country of SMEs", with 99.7% of the companies being SMEs. Without increasing the productivity of SMEs, Japan's overall productivity will not increase. Increasing productivity through IoT and AI, which has evolved greatly, is something that is finally achievable.
The original text in Japanese was posted on August 24, 2020.