自从“泡沫经济破灭”以来,人们经常用“失去的20年”来形容迄今为止的日本经济。但是,笔者首先想指出的是,虽然以20年来概括,但20世纪90年代的10年和2000年代的10年,日本的经济状况有相当大的差异。
这一差异从图表的宏观经济数据中也可以看出来。日本的实际国内生产总值(GDP)的增长率,从20世纪80年代的年均3~4%大幅度下降至90年代的0~1%。另一方面,在90年代,美国经济保持了2~4%的增长率,使日本经济的停滞感和闭塞感显得更为严重。
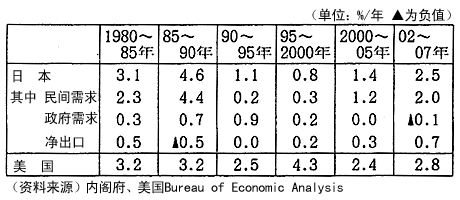
与此相比,到了2000年代前半期,日本经济增长率有所回升,特别是从2002年一直持续到2007年的长期繁荣期,超过了历史上的“伊奘诺景气”(1965年11月至1970年7月),增长率达到2.5%,虽然比美国低一些,但也实现了基本上与美国相同的增长。而且关于2002年以后日本的经济复苏,特别值得大书特书的是,正如公共需求的贡献度为负值所显示的那样,经济复苏的实现没有依靠财政动员。
2000年代经济复苏的特点,在供给方面也可以得到确认。根据一桥大学教授深尾京司和学习院大学宫川努教授的测算,全要素生产率对实际附加价值增长的贡献度,从1995年~2000年的年均0.2%上升至2000年~2005年的年均1.3%,这一上升可以说明两个5年期之间的实际附加价值增长率的上升。也就是说,从供给方面来看,2000年代的日本经济复苏完全是通过生产率上升实现的。
◆◆◆
不过,2000年代的日本经济复苏,虽说与美国相比差距不大,但依然低于美国,绝对水平也不高,这是事实。那么,我们应该怎样看待这种增长率的停滞呢?
关于20世纪90年代以后的美国经济增长,主流意见认为,其动力在于IT(信息技术)的普及带来了全要素生产率的上升。在2007年版的《美国总统经济顾问委员会年度报告》中,尤其对于90年代后半期以后的美国经济增长,强调指出了向IT资本的投资在流通和金融等多个产业非常活跃,在这些产业,全要素生产率大幅度上升。
另一方面,有多个研究结果显示出,日本进入2000年代以后,对IT资本的投资依然少于美国,而且IT投资提升全要素生产率的效果也比较小。IT对许多产业部门的生产工艺和技术革新(创新)产生影响,这一点与历史上的蒸气机和电力一样,属于典型的通用技术(GPT)。可以认为,90年代以后的日本经济增长相对较低,其中一个重要原因就是引进和普及IT这一新型通用技术的迟缓。
一般来说,通用技术从发明以后,到在经济领域广泛普及,再到实际上对生产率上升发挥作用,有相当长的时间差。美国斯坦福大学保罗·戴维(Paul David)教授从经济史的观点论述了这一问题。
戴维教授验证了在20世纪上半期,电力这一具有代表性的通用技术怎样改变了许多生产工艺,提高了生产率。在美国,19世纪末期,电力开始被利用于电灯方面,但是工厂动力使用电力比较迟缓,通过利用电力使产业的生产率上升,是在20世纪20年代以后。
戴维教授就这一时间差举出了两个原因:一个是使用电力需要废弃旧设备,为此付出成本;另一个是要想通过使用电力提高生产率,需要重新设计工厂组织等相关的创新。新型通用技术与经济和产业的各个方面相关联,因此如果成功地引进和普及,就可以产生巨大的效果。然而在另一方面,在到达这一目标之前,必须解决许多问题。
◆◆◆
明治以后日本经济发展的过程,在某种意义上说,也是通用技术的引进与普及的过程。幕府末期打开国门后,对于日本来说,在西欧发展起来的近代化工厂组织本身就是新型通用技术。在迅速引进新型通用技术,并出口产品,实现了增长的产业中,丝纺业(生丝制造业)具有代表性。
东京大学副教授中林真幸分析了日本丝纺业移植近代工厂组织的过程,明确指出,要想使工厂组织定型,提高生产率,需要解决若干课题。第一,丝纺业工厂要想具有改进产品的动机,就需要获得市场需求什么产品的信息,同时,根据该信息改进产品的成果将会给他们带来利益。可以充分满足这种条件的,是丝纺业工厂共同上市产品,联合起来形成公司,确立独自的商标(品牌),这就是一种创新。
第二,为了高效运营大规模工厂,以低成本生产高质量的生丝,工厂建立了独自的工资体制。这是一种“等级工资制”,对各个劳动者的工资,按照每个人的产品质量和物品的生产率等多个要素进行综合评价,决定其工资。通过这样的过程,日本丝纺业在20世纪初实现了大规模工厂高效生产,从1870年前桥藩首次引进西欧模式的成套设备以来,经过了大约30年的时间。
与第二次世界大战前的丝纺业相似的战后具有代表性的出口产业是汽车工业。正如丝纺业利用近代工厂组织这一通用技术一样,汽车工业体现了另一种新型通用技术。那就是把由许多零部件组成的产品,用流水线组装方式进行大量生产的技术,是在20世纪初由美国福特汽车公司创造的。
关于日本汽车工业移植福特生产体系的过程,东京大学教授和田一夫有详细的研究。和田教授强调,福特生产体系并非单纯的流水线组装,而是包括零部件兼容性、工厂设计和工资体制等相关要素在内的“体系(system)”。因此,日本汽车工业要想引进福特体系,就需要实现这些要素。经过反复摸索、解决这些课题的结果,创造出了一个同样的体系,即丰田汽车的“看板方式(Kanban system)”。
日本于20世纪30年代开始试行引进福特生产体系,确立“看板方式”是在60年代前半期。与近代化的工厂组织一样,移植福特生产体系也花费了大约30年的时间。
在日本经济的发展过程中,丝纺业和汽车工业的经验显示出,要想移植新型通用技术,把该技术与提高生产率相结合,就需要包括组织在内的各种相关领域的创新。而且,这些创新的结果,技术以不同于原型的形式固定下来,这种新型技术就成为日本产业的国际竞争力的源泉。
◆◆◆
IT是可与近代化工厂组织和大量生产技术相匹敌的大规模通用技术,不用说,进一步利用IT是今后实现日本经济持续增长的必经之路。另一方面,对照一下过去的经验可以知道,迄今为止,虽然IT的普及和提高生产率的效果都还不充分,但这既不是异常现象也不必悲观,这可以看作是在相关领域不断创新的同时,IT以日本固有的方式形成普及和使用条件的过程。
当前在政策上需要的是促进这一过程,至少不阻碍这一过程。例如,在急速老龄化的情况下,今后护理和医疗将成为需求增长的领域,同时也是利用IT提高生产率的潜力非常大的领域。但是在现行制度下,对于护理和医疗设施的经营者来说,即使引进新技术,提高生产率,也不会带来利益的增加,因此对引进新技术的积极性较低。在讨论“经济增长战略”时,应认真考虑这个问题。
2010年8月11日《日本经济新闻》