解説者 | 中馬 宏之 (ファカルティフェロー/一橋大学イノベーション研究センター) |
---|---|
発行日/NO. | Research Digest No.0003 |
ダウンロード/関連リンク |
業務の専門化・複雑化により、各部署の視野が狭くなり、全体最適に向けて各自が能動的な役割を果たすことが難しくなる―。現代の企業組織が共通して抱えるこうした課題を端的に示す事例が、日本の半導体産業に見られると中馬教授は指摘している。本論文では、多くの製造や研究開発の現場での調査を通して見えてきた「競争力を左右する要因」について、半導体生産システムに焦点を当てて分析する。
技術力で勝る日本企業が負ける?
――今回の論文で半導体産業のフィールド調査を実施されていますが、半導体産業に注目するようになったきっかけは何ですか。
1999年に、RIETIの前身である通商産業研究所の方から興味深い話を聞きました。それまで半導体の露光装置は、ニコンやキヤノンといった日本メーカーが大きなシェアを握っていました。ところが、その頃台頭してきたオランダメーカーに比べて、急に旗色が悪くなってきたというのです。特許や研究論文数などでは日本勢が圧倒的に勝っているはずなのに、どうしてなのか。メーカーの人も首をかしげている状況でした。
ところが、もっと話を聞いてみると、半導体関連では、装置メーカーよりも、その装置を使ってチップをつくるデバイスメーカーの方が状況が深刻だったのです。その頃、ちょうどある半導体メーカーから製造現場に関する深い調査への誘いがあったこともあり、本格的な実態調査に着手しました。
――経済学者としては珍しく、生産の現場に入って聞き取りをされたわけですが、具体的な調査方法や発見した事を教えて下さ。
これまで、海外メーカーも含めて半導体関連では20~30社に足を運びました。あるメーカーでは、何カ月にもわたって調査し、クリーンルームに入るための自分専用のスーツも用意してもらいました。半導体は通常7~8の主要工程からなっており、各工程のリーダーである組長、実際にラインを動かしている班長、さらには、関連装置・プロセスのエンジニアなどから順番に話を聞きました。また、工場に来ている業務請負会社の担当エンジニアにも聞き取りしました。
そうした調査を繰り返すうちに、各製造工程を連動させていく上で何がカギとなっているのか、どのような問題が発生し誰がどう対処しているのか、といったことを学んでいきました。その中であるべき半導体生産システムの姿がより鮮明になってきますから、生産性を高めて業績を伸ばしている工場とそうでない工場で何が違うのかといったことにも、気がつくようになりました。
米国が先行、"部分と全体"の「見える化」
――そうしたフィールド調査の結果として、論文ではMES(Manufacturing Execution System:製造実行システム)の「活用度」に注目されています。これはどういうことですか。
MESは、SAPをはじめとするERPなどの計画系ソフトウェアとは異なり、逐次修正を旨とする実行のソフトウエアです。今や製造現場だけでなく、病院、原子力発電所などの複雑なシステムを要する所にも導入されつつあります。
日本の半導体メーカーの競争力が衰えたのは90 年代のことですが、その時代にもMES は導入されていました。しかし、海外メーカーとはそれを活かす思想に差があったのです。
DRAM(記憶保持動作が必要な随時書き込み読み出しメモリー)を例に取ると、90 年代前半にプロセス(製造)技術が急に高度化します。集積度が1MB(メガビット)から4MB へ移行してからです。微細化によるトランジスタ数の増加とともにDRAMの物理的な構造が複雑になり、装置・プロセス自体や装置間搬送システムの高度化・自動化が急速に進んだのです。
この時、米国では従来型の企業特殊的なMESを、「オープン・オブジェクト指向型」に高める動きが進行していました。TI(テキサス・インスツルメンツ)を中心とした研究プロジェクトが組まれ、次世代の半導体工場を開発すべく、米政府からの財政支援も投入されたのです。
「オープン・オブジェクト指向型」MESの特長は、各種装置を広範囲にネットワーク化し、各工程間の相互依存関係を、生産に携わる多くの人に分かりやすく示すことです。生産システム内の" 部分と全体"の関係をリアルタイムに近い形で「一目瞭然化」(見える化)するのです。
DRAMを含む半導体デバイスやそれらを生産するために必要な技術が不連続的に複雑化したことが、この種の新MESの存在意義を格段に高めることになりました。生産システムが高度に複雑化・自動化していきますと、さまざまな相互依存性が顕在化しますので、それまでは考慮の対象とする必要のなかった要因によっても深刻な問題が多く発生してきます。その時、全体の状況を把握しないまま、局所的な対応をすると、さまざまな想定外の混乱を生み出します。
新型のMESで部分と全体との関係が一目瞭然化されていればいるほど、各種の想定外のトラブルに迅速かつ的確に対応できるようになります。これは、別の言い方をすると、状況判断のためのデータを直近まで収集できることを意味しますので、最終調整のための決定を、ぎりぎりまで遅らせることを意味します。漠然とした「見込み」で動くのと比べて、ムリ・ムダ・ムラを的確に軽減できます。米大リーグの松井秀喜選手がホームランを打てるのは、球筋を最後の最後まで見極めて、鋭いスイングで振り抜くからだと言われています。それと同じことを実践できるのです。
日本は原価管理の「見える化」で出遅れ
――論文によると、米国の半導体メーカーが導入したMESは、米国流トヨタ生産システムのアイデアを組み入れたものということですが、日本企業がそれに乗り遅れた理由は何ですか。
それは2つの側面が指摘できると思います。1つは日本の生産現場が、米国と比べると、それぞれの工程に裁量権を多く持たせる「ボトムアップ」型だという点です。米国は「トップダウン」型に近いので、全体を統一的に管理するMESが入れやすかったのです。「ボトムアップ」型では、MESを効果的に利用するために、さまざまな階層で生産システムを自らの裁量で支えている人々の知識やノウハウの互換性や再利用性にきめ細かく配慮しなければなりません。
もう1つは、複雑化した生産システムの原価管理方法で遅れを取ってしまった点です。多くの日本のメーカーでは、外部に自らの経営状況を知らせる財務会計には熱心ですが、実際の生産に貢献するための「管理会計」がおろそかにされがちです。もちろん、日本でも優れたメーカーは、独自の優れた管理会計方式を持っています。トヨタ、京セラ、村田製作所、花王等々です。
複雑な生産システムに見合った管理会計システムがないと、コスト低減意欲が的確に発揮されません。通常の標準全部原価計算方式では、仕掛在庫や製品在庫は資産計上されてしまいます。このようなことの弊害が日本で広く認知されはじめたのは、2000年頃にキャッシュフロー会計が導入されてからです。日本の半導体メーカーが米国企業より、棚卸資産を多く抱えがちであったこと(売上高/棚卸資産額で示される"回転率"が低かったこと)は、以下の図からもわかります。
トヨタでは、昔から生産効率向上の最終目標が原価低減であることを認識しています。効率を上げるには、モノの流れの見える化だけでなく、原価の発生状況の見える化が不可欠です。
――そういった日本における認知の遅れが、90年代には現場の志気の低下を招いたと指摘されていますが、具体的にはどういうことですか。
さきほどお話ししたように、半導体産業では90年代に入り、生産システムが飛躍的に高度化・自動化しました。装置・プロセス技術の「ブラックボックス」化も進みました。
その結果、それまで生産現場で主流だった熟練技術工主導での進捗管理や問題発見・解決が難しくなったのです。そのため、進捗管理や問題発見・解決の多くをエンジニアが担うシステムに移行しようとしました。そうなると、熟練技能工には裁量を働かせる余地がなくなり、自らの貢献度が急減します。その結果、起きたのが労働意欲の低下です。次表は、日本の製造業の強みとも言えたQC(品質管理)活動が半導体工場で衰えたことを如実に物語っています。
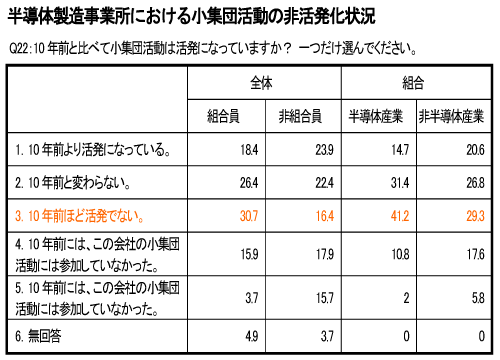
知識・ノウハウの共有・交換がカギに
――論文の中で、改革を進めるユニークな日本企業を紹介されていますね。
日本電気と日立製作所のDRAM部門が統合して99年末に発足したエルピーダメモリの子会社の1つである広島エルピーダメモリです。2003年の終わり頃から生産システム改革に取り組んでいます。
同社では管理職から技能工、エンジニア、請負工までが四六時中参照する「バイブル」的な管理指標(WIP Status Report)があります。同社のMESの利用方法の特長は、工場内の"部門と全体"の関係をユニークに一目瞭然化することに加え、一目瞭然化された状況をうまく全員にフィードバックして人々の間のコミュニケーション効率を格段に高めている点にあります。
工場内で想定内・想定外の問題が生じたとしましょう。その時に常に、問題の発見、原因、解決方法をすぐに見いだすことは大変に難しいことです。そのためには、工場内に散在する様々な知識・ノウハウを持った人々を迅速に結集する必要があります。同社のMES の利用方法は、そうした知恵の結集が広範囲にわたって自律的に生まれやすいように工夫されています。
――コミュニケーション効率の向上や知識・ノウハウの結集について、同社が具体的にどういった工夫をしているのか教えてください。
広島エルピーダの例は、ボトムアップ型の日本流生産現場と、全体の統制・管理を図るというトップダウン型を融合させたものと言え、海外にもないユニークな仕組みになっています(下図)。
たとえばですが、生産現場には、「スーパーバイザー」と呼ばれる各工程を横に束ねる人々がいます。海外のみならず多くの日本の半導体工場では、スーパーバイザーにあたる仕事はエンジニアが担っています。一方、同社では熟練工がスーパーバイザーとして活躍しています。日本の生産システムは"組長ライン"で成り立っていると言われるように、組長的な熟練技能工の高度な進捗管理や問題発見・解決能力が重要な役割を果たしています。広島エルピーダでは、MESがもたらした一目瞭然化便益を有効利用することにより、極めて日本的な生産システムを作り上げています。
論文の副題に掲げた「メタ摺り合わせ」の「メタ」とは、心理学の「メタ認知」のメタで、自分の行動を客観視するという意味です。広島エルピーダのように、MESによる一目瞭然化便益をうまく使うと、末端のオペレータや請負工でさえ、ワンランク高い視点から自らが担っている作業の全体への影響・貢献度を認知することができきます。そして、多くの人々が、自らを取り巻く部分と全体の関係を同じ視点から認知できるようになると、すべての人々の力を合わせた以上の力が発揮されるようになります。そういう力が、競争力向上の決め手になるのです。ただ、日本の製造業全体では、このようなMESの有効利用によって、一目瞭然化の便益を意図的に取り入れるような傾向はありません。その意味では、まだ改善の余地が大きいと思います。
一目瞭然化便益を有効利用した経済活性化
――この研究の政策面での含意、今後の方向性についてお聞かせ下さい。
1つは、ITを駆使した一目瞭然化便益を、政策形成プロセスにも意図的に利用すべきだということです。一方的に政策目標が掲げられても、各省庁・各部局が局所的に動いたのでは、全体最適を達成できません。一目瞭然化便益の有効利用は、縦割りの弊害打破に不可欠です。
もう1つは、ITによる一目瞭然化便益を有効利用するためのシステム研究・開発を国が積極的に支援するということも考えられます。大きな外部効果をもたらすからです。先に紹介しました米国政府支援による新MES開発は、その一例と言えます。
現代の日本では、各種の専門家達のナレッジの互換性・再利用性を高めて新たなナレッジの創造速度を上げることが強く要請されています。本論の視点に基づき、そのための仕組の研究をさらに深めたいと思っています。
解説者紹介
一橋大学経済学部卒業、ニューヨーク州立大学バッファロー校Ph.D.(経済学)。東京都立大学経済学部助教授等を経て、99年から一橋大学イノベーション研究センター教授。製造業の競争力規定要因などを研究。2002年よりRIETI ファカルティフェロー。最近の代表論文は"Increasing complexity and limits of organization in the microlithography industry: implications for science-based industries" Research Policy, Vol. 35, No. 3, 2006 など。