The hollowing out of the Japanese manufacturing industry shows no signs of hitting bottom. For the first time in 51 years, the number of workers employed in the manufacturing sector fell below 10 million in December 2012. The economic policies of the government of Prime Minister Shinzo Abe are geared toward ending deflation, thereby achieving domestic demand expansion accompanied by wage increases. It is certainly important to increase wages for workers. However, a more important test for the policies is whether the resulting rise in prices will stimulate a boost in supply, hence an increase in labor demand to generate new employment. The number of workers employed in the manufacturing sector is no more than one-fourth of those in the service sector. Therefore, the decline of the manufacturing sector may not have any serious impact on the overall employment in Japan. This, however, is not the case in the local economies.
♦ ♦ ♦
Based on data from the Labour Force Survey of the Ministry of Internal Affairs and Communications, the figure below shows the changes in employment in the manufacturing and service sectors over the five years between 2007 and 2012 summarized for two types of economic regions, namely, "core regions" comprising Southern Kanto, Tokai, and Kinki and "peripheral regions" consisting of the others. Changes in the number of workers in the youth and elderly age groups are taken as "new entries" into and "exits" from the labor market respectively, whereas those in the number of workers in the age group in between are deemed to be attributable to changes in the economic conditions.
More specifically, the number of new entries of youth workers is calculated as the sum total of net changes over the five years between 2007 and 2012 in the number of workers in two age groups--the age group 20-24 in 2007 (who became the age group 25-29 in 2012) and the age group 15-19 (20-24)--plus the number of workers in the age group 15-19 in 2012. Likewise, the number of exits from the labor market is calculated by subtracting the number of workers aged 55 or older in 2007 from that of those aged 60 or older in 2012. Changes in the number of youth and elderly workers are obtained by netting the number of new entries and that of exits. Meanwhile, differences in the number of workers in the age group 25- 54 in 2007 and that of those in the age group 30-59 in 2012 are regarded as changes attributable to economic conditions. No distinction is made in terms of employment status, i.e., between permanent full-time workers and the others.
Observation through the three filters of age, sector, and region reveals the following trends. First, a decrease in the number of manufacturing workers attributable to economic conditions occurred in the peripheral regions on almost the same scale as in the core regions where industries are concentrated. Second, the core regions suffered a significantly greater decrease in the number of youth and elderly workers in the manufacturing sector than in the peripheral regions. In particular, the Southern Kanto region shows a significant gap between the number of new entries (100,000) and that of exits (390,000). This suggests that although the so-called baby boom generation reached their mandatory retirement age during this period, companies did not hire youth workers in a sufficient number to make up for the outgoing workers. The Southern Kanto region accounts for 55% of the decline in the number of youth and elderly workers in the manufacturing sector in the core regions.
Third, in the core regions, even though a total of approximately 800,000 jobs were lost in the manufacturing sector, a greater number of jobs were generated in the service sector. In contrast, in the peripheral regions, the service sector was unable to absorb the job losses in the manufacturing sector, and the overall number of jobs decreased under the direct impact of the hollowing out of industries.
Since services are non-tradable, the geographic scope of markets for service businesses is basically limited to the areas in and around where they are located. In peripheral regions with small populations, the decline of the manufacturing sector, i.e., industries that deal in tradable goods and are capable of bringing in demand from other areas, means the loss of the growth engine for the service sector. The figure does not include the primary industry, another important tradable goods sector for local economies. However, it is well known that the primary sector is in a pessimistic state. Now that Japan has undergone a structural change into a service-oriented economy, some people are calling for a demographic shift from the peripheral to the core regions where service jobs are available rather than trying to generate manufacturing jobs in the peripheral regions. This sounds like a reasonable idea.
However, the figure shows that the number of service jobs created in the core regions is barely enough to absorb the manufacturing job losses within the same regions. As such, Japanese service industries are far from being powerful enough to absorb the labor force in the peripheral regions and lead the entire national economy into growth. This means that putting the brakes on the decline of the manufacturing sector would bring significant benefits, particularly to local economies.
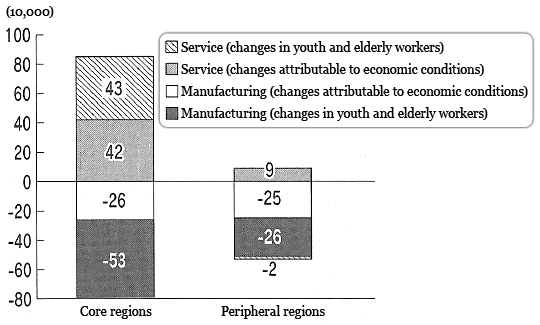
♦ ♦ ♦
In considering ways to restore the manufacturing sector, the United States serves as a good reference. The country that had transformed into a post-industrial economy long ahead of Japan is now witnessing the return of manufacturing from overseas in a phenomenon referred to as the "manufacturing renaissance." It is also called "reshoring" in contrast to "offshoring" which refers to the outflow of manufacturing from the United States to overseas.
A survey conducted by a supply-chain research group from the Massachusetts Institute of Technology (MIT) found that the shorter time to market, rising costs in host countries, and the need to ensure strict quality control for products are among the top reasons for reshoring.
The Economist pointed to the changing climate in China--i.e., soaring wages for local workers and managers, tighter labor regulations, and frequent occurrence of labor disputes--as a force driving American manufacturing back home. In addition, some important developments in the United States were also cited as contributing factors. Specifically, labor unions are now showing greater flexibility and willingness to accept lower wages for the sake of keeping jobs at home, and this, combined with the high productivity of American workers in general, resulted in greater labor force competitiveness, while energy prices are expected to fall with an increase in shale gas production.
The Boston Consulting Group published an interesting report, "Made in America, Again," in 2011. As factors inducing American manufacturers to move their production closer to the market, it pointed to higher transpacific shipping rates due to rising oil prices, the costs of keeping inventories for mass production and mass transportation, difficulty to respond quickly to changes in market trends, and greater awareness of the risk of large-scale natural disasters.
Technological innovation enabling the small-lot production of a wide variety of products at low cost, as exemplified by the development of three-dimensional (3D) printers that eliminated the need to use expensive molding tools, will likely further reduce the advantage of offshoring and bring production closer to the market. Reshoring destinations tend to be concentrated in the southern states, where labor and land are affordable and natural gas prices are relatively cheap, and this suggests that local economies are most likely to reap benefits from manufacturing reshoring.
♦ ♦ ♦
Looked at from the perspective of spatial economics, the area in which I specialize, the hollowing out of the Japanese manufacturing sector can be summarized as a phenomenon driven by the following three factors: low production costs overseas, insufficient domestic demand, and easy access to the domestic market from overseas. In terms of narrowing disparities in manufacturing costs across the world and rising international distribution costs, Japan is in the same situation as the United States. Therefore, we can expect to see the full-fledged return of the manufacturing industry as a result of the yen's further depreciation and eventual stabilization at an appropriate level.
However, there are also some differences between Japan and the United States. First, cost factors unique to Japan are not limited to the strong yen. Cheap energy, a major factor making the United States cost competitive, is not available. Indeed, Japan's energy costs have been rising following the wake of the nuclear accident in March 2011. High corporate tax rates are another disadvantage. On the other hand, the presence of manufacturing clusters in Japan and extensive production networks across East Asia, which provides easy access to parts and components, is a major advantage for Japanese manufacturers. By reexamining all positive and negative factors affecting manufacturing costs, Japan should create an enabling environment that facilitates the return of manufacturing.
Second, putting an early end to the ongoing deflation is essential because Japanese manufacturers had moved operations overseas not only to avoid high costs here but also because of the lack of sufficient domestic demand due to years of deflation. As a way to take advantage of overseas demand effectively, it is also important to make vigorous efforts to enter into free trade agreements.
Third, as demand recovers, consumer preferences are expected to become more diverse with their focus shifting away from standardized low-price products easily available from overseas to more sophisticated and differentiated products. This points to the need for more fine-tuned responses in the future, hence greater advantage to manufacturing in Japan. Those companies geared toward competing in prices through relocation to low-wage countries and mass production need to shift their strategies to focus on product differentiation and technological innovation that can enable the efficient small-lot production of a wide variety of products.
In order to make its own version of manufacturing renaissance happen, Japan must overcome all of the above-discussed challenges in the areas of costs, demand, and approaches to markets. The government and industries must work together and forge a common vision for a balanced economic renaissance in post-deflation Japan so as to create jobs in the local regions.
* Translated by RIETI.
March 21, 2013 Nihon Keizai Shimbun