Information
- Time and Date: 10:00 - 17:10, Tuesday, November 13, 2012
- Venue: Research Institute of Economy, Trade and Industry (RIETI), Tokyo
Summary
Mainstreaming Global Resilience: The Lessons from the Great East Japan Earthquake and the Great Floods in Thailand
FUJITA Masahisa (President & Chief Research Officer, RIETI / Professor, Konan University / Adjunct Professor, Institute of Economic Research, Kyoto University)
Supply Chain Disruptions Caused by the Great East Japan Earthquake
In order to build new production networks in Asia, many urgent tasks need to be completed. I would like to focus on the particular aspect of developing production networks, with lessons learned from the recent mega-disasters in Japan and Thailand.
Let me give you a brief overview of the Great East Japan Earthquake which occurred on March 11, 2011. It had a magnitude of 9.0, making it one of the strongest in history, and caused a tsunami surpassing 20 meters high, and hit several hundred kilometers of the Tohoku coastline on the eastern side of Japan. This was followed by a nuclear crisis categorized as level 7 on the International Nuclear Event Scale. Subsequently, a nationwide electricity shortage ensued and, finally, the collapse, both nationally and globally, of the industrial supply chain. That directly cost the lives of approximately 18,000 people. The economic and infrastructure damage was about $200 billion.
The direct damage induced indirect damage due to the collapse of the industrial supply chain (Figure 1). Japan's mining and manufacturing production in March was -15.5%, the biggest monthly drop in its history. Exports in April were -12% as well. The major disaster areas in Tohoku were Iwate, Miyagi, and Fukushima prefectures, in which 4.5% of the nation's population are located and account for 4% of the national GDP. Although their share of exports is just 1%, the initial damage in the disaster areas largely impacted the supply chain throughout Japan, parts of East Asia, and the rest of the world. The automobile industry, which creates its products by assembling 20,000-30,000 parts, including materials, electronics, and machinery, was the most affected sector, and it is unsurprising that it is vulnerable to supply chain disruptions.
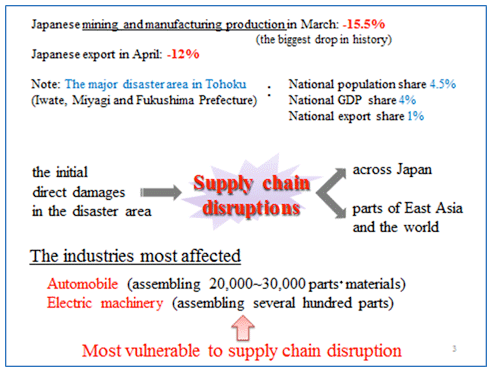
Due to rapid progress in IT and transport technology, together with the promotion of free trade through the World Trade Organization (WTO), free trade agreements (FTAs), and economic partnership agreements (EPAs), we have seen the globalization of production, trade, and investment, as well as the local agglomeration of production and consumption in major cities throughout Asia and the world. The flow of global production occurs within a very complex network. East Asia today is called the world's production center based on this supply chain network. The disasters in the Tohoku region and Thailand caused major disruptions in the supply chain throughout Asia, affecting major industrial agglomerations including those in Manila and Shanghai.
Why is there so much agglomeration of production throughout Asia? Agglomeration occurs through a snowball effect in principle. For example, the automotive, electronic, and machinery industries have production centers, suppliers, power plants, and material centers located near Bangkok. This is one of the biggest agglomeration for industries in the Association of Southeast Asian Nations (ASEAN) region. Production in the Bangkok area uses key parts made in South Korea, Taiwan, and Japan. Of equal importance is that Bangkok not only utilizes imported materials, but also produces major parts and materials exported to other Asian countries. If Japan, South Korea, or Taiwan experiences a major disaster, production in Bangkok is affected, and if Bangkok is met with a major disaster, all other Asian countries are affected subsequently.
Key factors for agglomeration are scale economies and low transport costs. Lower transport costs encourage more concentration of production activity at a limited number of locations, and this was the background of the disruptions that we saw in 2011. For example, looking specifically at the automobile industry, a typical car is assembled from 20,000-30,000 parts. Each key part is usually produced at either one or a few locations, thus, all of the parts are exchanged through a complex supply chain network that handles everything from their procurement to the delivery of finished products. Moreover, in order to minimize inventory stock, each production center adopts a just-in-time procurement policy. This is very efficient under normal conditions but is vulnerable to major disasters.
Japanese Automobile Industry was Most Affected by the Earthquake
Roughly 10 million cars are produced in Japan per year, with half of those sold domestically. Japanese automakers produce 13 million cars annually overseas, which require key parts made in Japan as well. There are three automotive production agglomerations in Japan. The main one is the Tokai region, which extends from Tokyo to Nagoya. Another agglomeration in the Kyushu region has existed since 1980 as well as a new one in the Tohoku region since 1990. In the Tohoku region, factories in the northeast suffered from the tsunami, and the central region's factories as well as the highways of the south were affected by the Great East Japan Earthquake. Some plants took more than a year and a half to recover, while others did not sustain any serious losses but were unable to continue operations because of a lack of procuring parts from elsewhere.
Looking at the automobile production index from 2008 to 2011, it appears that the Great East Japan Earthquake and the Lehman Brothers collapse affected Japan's automobile industry equally (Figure 2). Both led to a production growth rate of -50%. The automobile production trend in Tohoku is synchronized to the overall trend of automobile production in Japan. Although only the Tohoku region was directly damaged, the total Japanese automobile production growth rate fell to -50% because of supply change disruptions.
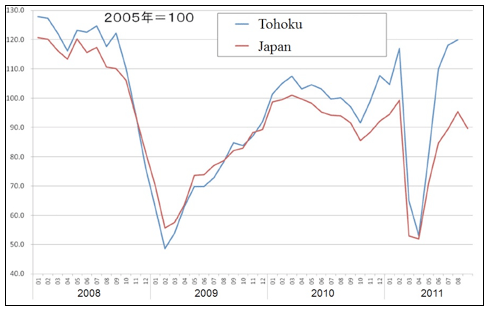
Shifting to Thailand, great floods occurred in September 2011. The Bangkok region is one of the biggest agglomerations of automobile and electronics manufacturing in the ASEAN region. Most large Japanese electronic and automobile companies operate plants in the area and are supported by other plants that produce the most important parts. There are more than 1,300 Japanese firms in the area.
How did the Great East Japan Earthquake and the floods affect Thailand's economy? Automobile production in Thailand in May 2011 was -25% because of a shortage of parts from Japan. It slowly recovered up until September, but then dropped sharply to -85% in November because of the floods (Figure 3).
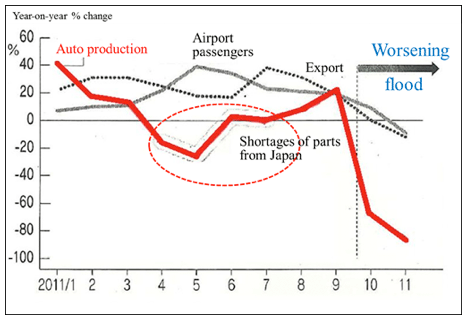
Examining the Global Impact of the Great East Japan Earthquake and Thailand's Floods
What was the global impact of these mega-disasters? Japan exports numerous materials and parts, as does Thailand. Thailand exports parts throughout ASEAN. Transport costs, broadly defined, are low in this region thanks to tariff agreements among other reasons. As manufacturers try to maximize economies of scale, each key part is produced in a specific country. In the case of the automobile industry, Thailand specializes in frame parts, panels, electronics, interior parts, engine parts, and others. The Philippines, for example, mostly produces parts such as engine fuel systems, emissions systems, electric parts, suspension parts, and manual transmissions. A disaster in any country affects the entire production system since the parts are exchanged between the countries.
We can understand the global impact of the Great East Japan Earthquake and Thailand's floods by looking at production data from Japan, the Guangdong region in China, Thailand, and the United States (Figure 4). Up until March 11, Japan's production grew normally. After the earthquake, the automobile production growth rate in Japan fell to -85.7%. Production recovered gradually but decreased suddenly in September due to the floods in Thailand. Looking at statistics from Guangdong, production growth in April was -39%, and it recovered in August but dropped significantly in September again because of the floods in Thailand. Examining Thailand, because of the Great East Japan Earthquake and the shortage of parts, the production growth rate was -25% in May. This rate recovered until September but sharply fell to -85%. Looking at the United States, the Great East Japan Earthquake caused the production growth rate to drop, with the biggest drop in July, when the growth rate turned negative. The impact of the floods in Thailand was less significant for the United States.
The biggest drop in the production growth rate in Japan was in March, and in China, it was in April. In Thailand, this was seen a month later, in May, and in the United States, it was in July. The greater the distance from Japan, the longer it took for the disaster to affect the country in question. This is likely because the further the distance of the production center, the more inventory stock it held.
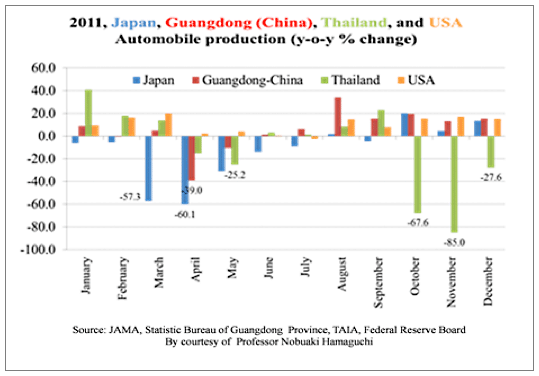
The quake and floods affected other ASEAN countries, specifically Indonesia, Malaysia, and the Philippines (Figure 5). In Thailand, the biggest drops in production growth occurred in May and November, and in Malaysia, it was in April, at -25%, which is the same level as in Thailand. Indonesia saw strong domestic production up until last March, but its growth rate dropped off significantly and turned negative due to the Great East Japan Earthquake. It recovered strongly in September but dropped again sharply in October due to the floods. The Philippines was perhaps the country that was most impacted and which suffered the most from both disasters. The Great East Japan Earthquake caused the production growth rate to drop to -57% in May, and the Thailand floods led to a drop to -40% in December. We can see that if there is a major disaster in either Japan or Thailand, all ASEAN countries are significantly affected.
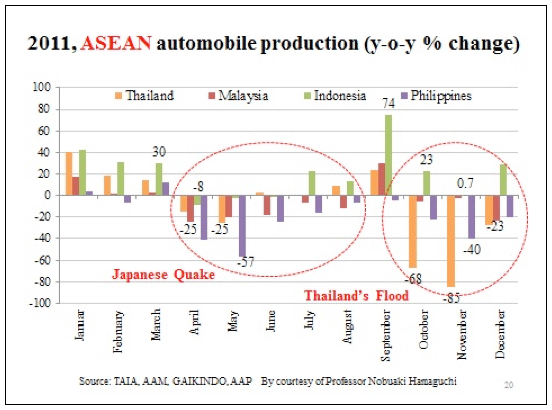
This does not only affect the automobile industry. For instance, consider the weekly average prices of hard disk drives. The price of a hard disk drive is the same throughout the world in principle. On October 1, the price of a hard disk drive was about 5,000 yen. However, by the end of the month, the price had tripled. Thailand produces about 45% of the world's hard disk drives, hence the loss in production greatly impacted this industry.
How Can we Enhance the Resiliency of the Global Supply Chains?
What is the solution to these issues? We need international cooperation to promote the resiliency of the global supply chains. We must first recognize that no place in the world is risk free. There is the potential that supply chains may be disrupted due to a major disaster, including human-induced ones such as conflicts. For instance, the recent political conflict between China and Japan has affected sales. Japanese automobile sales in China post-tsunami dropped by 50%, and sales post-floods dropped by 50%. Due to the current political conflict, sales have dropped by about 50%. We must consider all of the possible sources of supply chain disruptions, which can be at any node or link, from materials to consumers at any location in the world. In order to enhance the resiliency of the global supply chain, we need major international cooperation. We must use economies of scale as much as possible, but we must also disperse risk.
Automobile production tends to utilize tens of thousands of small companies that support major production networks. Because small companies are vulnerable to major disasters, group-wide cooperation is indispensable. There are many ways in which individual enterprises can enhance risk management, such as through the virtual and actual dispersion of key plants, standardization of parts and materials, diversification of supplies, and utilization of disaster insurance. Particularly in developing countries, regional cooperation, including regional or national government infrastructure improvements, is essential. Of utmost importance for these countries is to prevent urban flooding and ensure a stable electric supply. In the long run, we must decentralize the overconcentration of economic and political functions in capital cities such as Tokyo, Seoul, and Taipei. We need more resilient and nationwide systems.
International cooperation is essential to the enhancement of resiliency in developing countries. During the 1950s and 1960s, major typhoons greatly impacted our production systems. Japan subsequently developed infrastructure such as water systems and electrical systems to address this due to the great assistance received from the World Bank and the International Monetary Fund among others. This same process should be carried out in major developing countries throughout the world. We also need a more comprehensive global insurance system.
A concrete example of supply chain risk mitigation is a proposal from the Thai government to develop sister industrial clusters. According to this proposal, during normal times, each production cluster will focus on its own special products. However, in the case of a major disaster, the region's sister cluster would step in to provide backup production of common parts. Such country-to-country cooperation is very important. While we compete with each other during normal times, we should cooperate in times of disasters.
There is a strong production network in East Asia. The next step for the global supply chain will be to connect South Asia and Southeast Asia to East Asia. After that, we must incorporate Africa. South Asia and Africa cannot build sufficient infrastructure to mitigate major disasters on their own. International cooperation is essential as is cooperation on innovation toward upgrading our brainpower networks. The lessons of Japan and Thailand are that we should work to move the supply chain toward higher value production and greater safety.